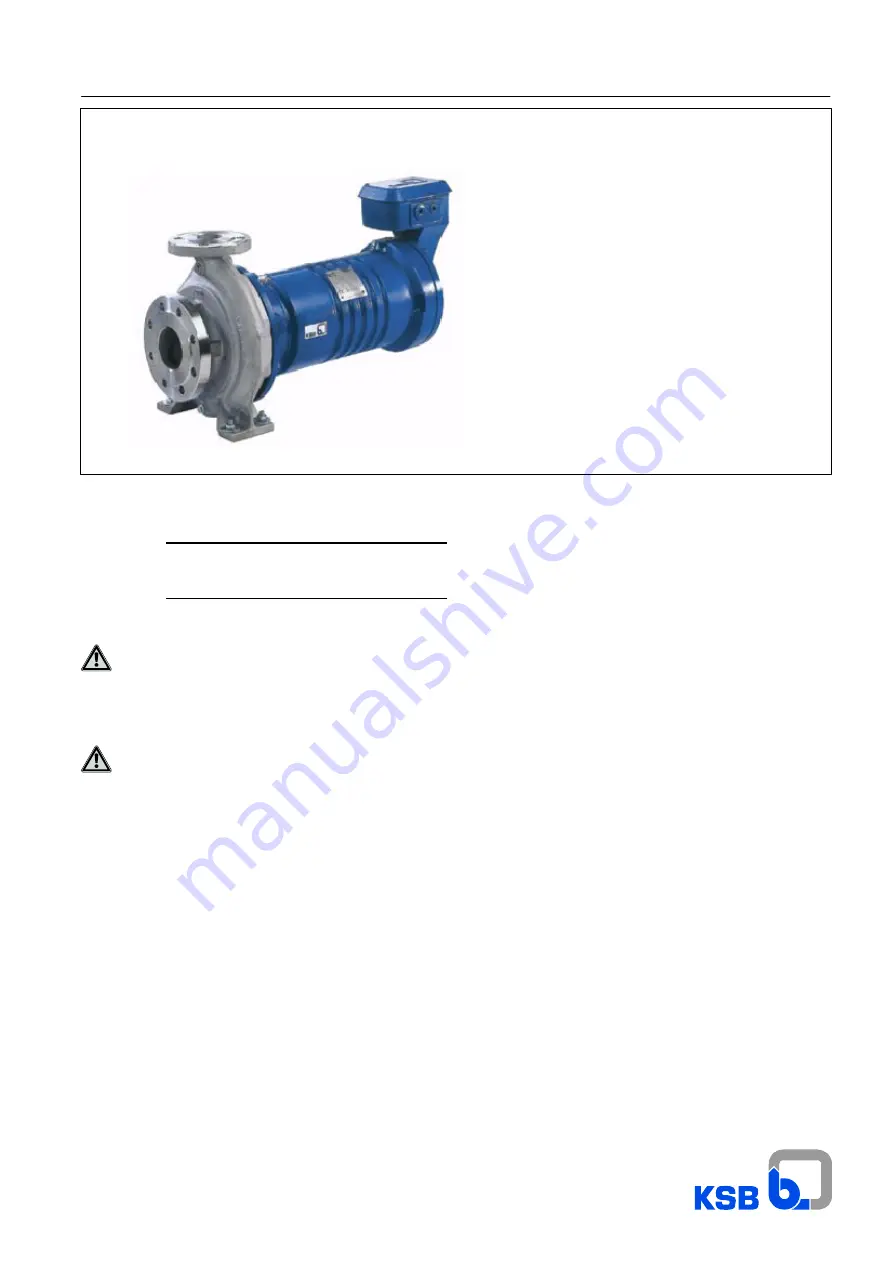
Secochem-Ex
Original operating instructions
2939.8/10-EN
Explosion-proof Standardized
Chemical Pump
with canned motor
Connection dimensions to EN 22 858/ISO 2858
Explosion protection as per directive 94/9/EC
Order No.:
Type series:
These operating instructions contain fundamental
information and precautionary notes. Please read
the manual thoroughly prior to installation of unit,
electrical connection and commissioning. It is imperative
to comply with all other operating instructions referring to
components of individual units.
This manual shall always be kept close to the unit’s
location of operation or directly on the pump set.