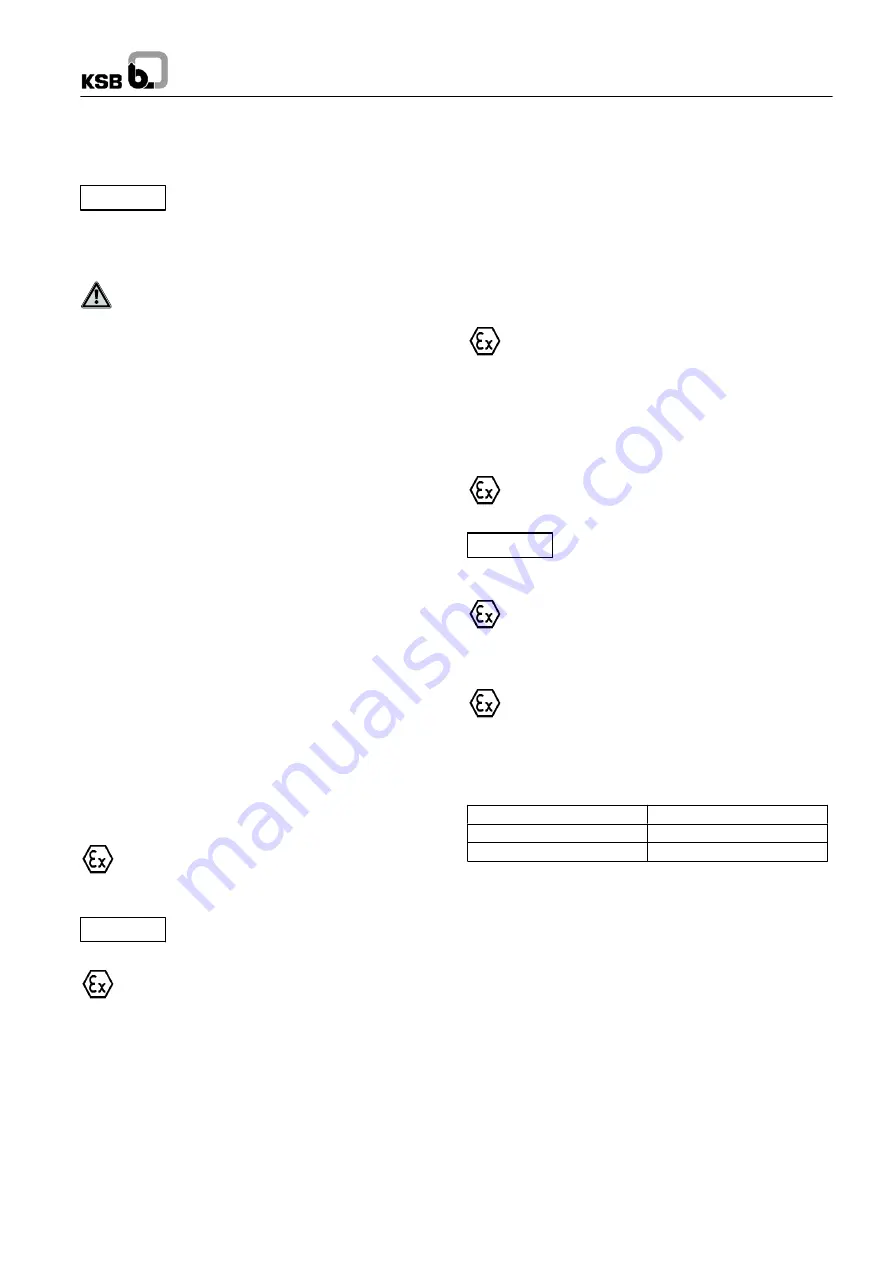
Caution
Caution
Caution
Secochem-Ex
15
6.1.2
Checking the direction of rotation
When the unit has been connected to the electric power supply,
verify the following (local and national regulations have to be
taken into account separately):
For trouble-free operation of the pump, the
correct direction of rotation of the impeller is of
paramount importance. If running in the wrong direction of
rotation, the pump cannot reach its duty point; vibrations and
overheating will be the consequence. The pump set might be
damaged.
Before checking the direction of rotation make sure that
there is no foreign matter in the pump casing. The pump
set must be adequately secured against overturning.
Never hold your hands or any other objects into the pump!
Owing to the special design features of this pump set, the
direction of rotation can only be checked indirectly.
Proceed as follows:
-- Start up the pump as described in section 6.1.5.
Close the shut-off valve in the discharge line and check
whether the head achieved corresponds to the shutoff head
indicated in the pump performance curve. (Not longer than
1 min.).
-- If the head achieved is more than 10 % lower than is to be
expected, switch off the pump set, take the necessary
precautions (disconnect the pump set from the power
supply, etc.), check the electrical connection as per section
5.5, and correct, if necessary.
-- Interchange terminals to determine whether a higher
pressure gauge reading is reached, which corresponds to
the correct direction of rotation.
6.1.3
Cleaning the plant piping
The cleaning operation mode and duration for flushing and
pickling service must be matched to the casing and seal
materials used.
6.1.4
Start-up strainer
If a start-up strainer has been fitted to protect the pumps against
dirt and/or to retain contamination from the plant, the strainer’s
contamination level must be monitored by measuring the
differential pressure so as to ensure adequate inlet pressure for
the pump.
6.1.5
Start-up
Pump operation with the shut-off valves in the discharge
and suction pipes closed is not permitted. The
permissible pressure and temperature limits might be
exceeded. In extreme cases, the pump may burst.
Open the barrier liquid feed, if any, and adjust
the barrier liquid pressure in line with the data
sheet.
The proper functioning of the barrier pressure unit shall
be monitored.
Make sure that the pump is always started up with the
suction-side shut-off valve fully open and the discharge-side
shut-off valve slightly open! Only after the pump has reached
full rotational speed shall the shut-off valve in the discharge line
be opened further and adjusted to comply with the duty point.
Check the direction of rotation, if necessary (cf. 6.1.2).
6.1.6
Shutdown
Close the shut-off valve in the discharge line. If the discharge
line is equipped with a non-return or check valve, the shut-off
element may remain open if there is backpressure.
Switch off the pump unit, then shut down the barrier liquid
system (if connected).
For prolonged shutdowns, also close the shut-off valve in the
suction line.
In the event of prolonged shutdowns, liquids which change their
physical condition due to changes in concentration,
polymerization, crystallization, solidification, etc. must be
drained from the pump and the motor. If applicable, flush the
pump via connection 11 E and close again in line with section
7.3.
6.2
Operating limits
The pump’s/unit’s application limits regarding pressure,
temperature, speed and motor data are stated on the
data sheet and must be strictly adhered to, also to safeguard
explosion protection.
If a data sheet is not available, contact KSB!
6.2.1
Temperature of the medium handled, ambient
temperature
Do not operate the pump at fluid temperatures (T
M
)
exceeding those specified in the data sheet or on the
name plate.
Motor power P
2
depends on the temperature of
the medium handled. It decreases as
temperatures increase. Damage resulting from disregarding
this warning will not be covered by the KSB warranty.
If the pump is used in hazardous areas, ambient
temperature shall be between -20
C and +40
C.
6.2.2
Switching frequency
A combination of temperature sensors embedded in the
winding (e.g. PTC thermistors) and tripping unit is
permitted as sole overload protection arrangement for motors
not operated in S1 mode
.
To prevent high temperature increases in the motor and
excessive loads on the pump set, the switching frequency shall
not exceed the following number of start-ups per hour (S).
Motor rating (kW)
max. S (start-ups/h)
up to 15
60
> 15 to 55
30
6.2.3
Density of medium handled
The power input of the pump will increase in proportion to the
density and viscosity of the medium handled. To avoid
overloading of the pump set, the density and viscosity of the
medium must comply with the data specified in the purchase
order.
6.2.4
Abrasive media
When the pump handles liquids containing abrasive
substances, increased wear of the wetted pump components
is to be expected. The intervals recommended for servicing and
maintenance shall be shortened.
If the medium handled contains magnetic particles, appropriate
measures (e.g. magnetic separator) shall be taken to prevent
them from entering the rotor space.