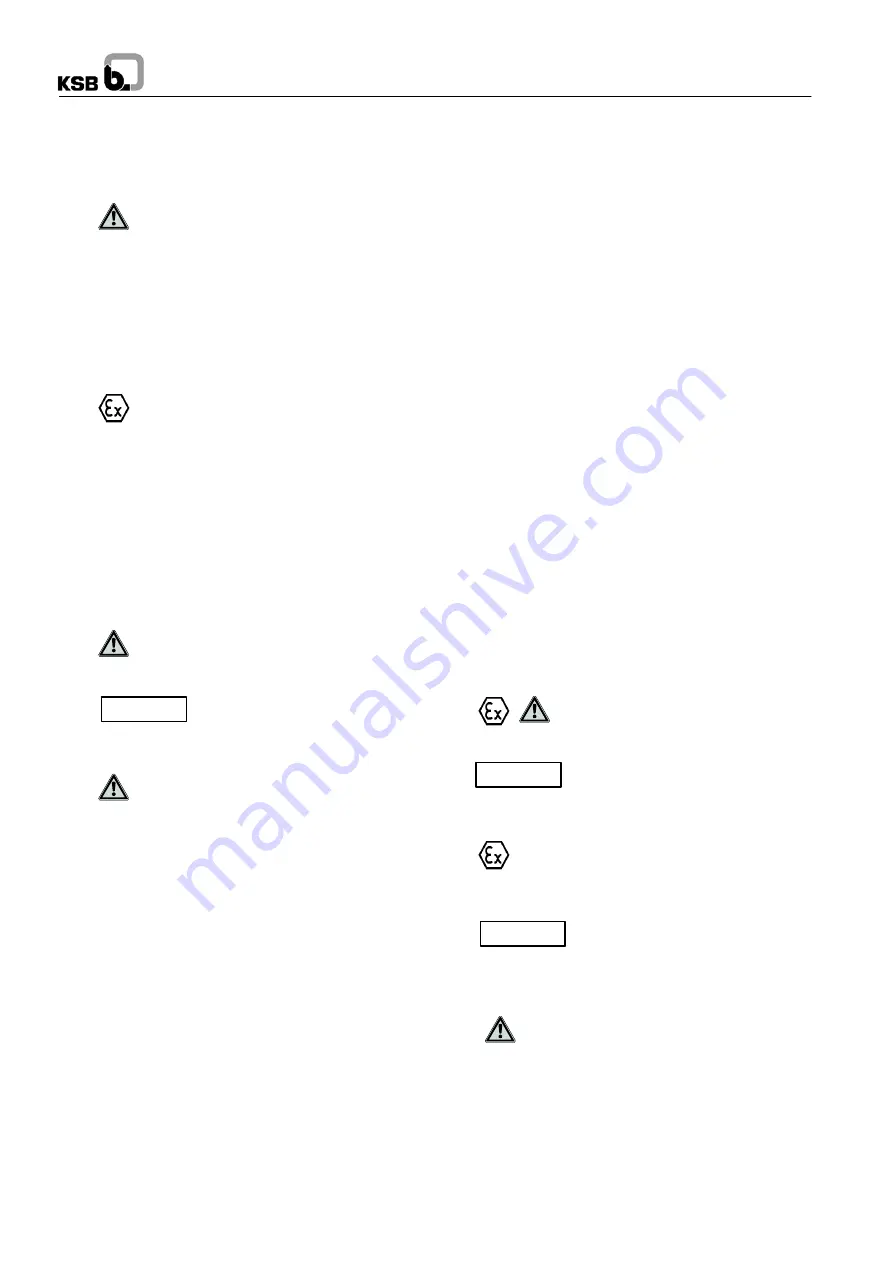
Note
Note
Caution
Secochem-Ex
18
2.a Removing the pump set from the piping
-- Undo the flanged connections.
-- Undo the pump foot bolts, if applicable.
-- Remove the pump from the piping and place on a
clean and level surface.
Fluid residues may escape! Risk of personal
injury! Collect and properly dispose of any fluid
residues which might escape!
-- Set the pump set down onto the motor section and the
pump foot and secure against tipping over.
2.b Removing the back pull-out unit
-- Undo hexagon nuts 920.01.
-- Use forcing screws to push the complete back pull--out
unit out of casing 102.
-- Take care to prevent the impeller from colliding with the
sides of the pump casing.
Watch out for possibly hazardous medium
residues (protective clothing). Collect and
properly dispose of any medium residues which might
escape!
-- Set the back pull--out unit down on the motor section
onto a clean surface in such a way that the impeller and
the shaft/rotor do not touch the surface. Secure the back
pull--out unit against tipping over.
2.c Dismantling the pump casing
If the complete pump set has been removed from the
piping, dismantle the pump casing as follows:
-- Place the pump set in a clean and level assembly area.
-- Undo hexagon nuts 920.01 and remove the pump
casing.
Watch out for possibly hazardous medium
residues (protective clothing). Collect and
properly dispose of any medium residues which might
escape!
Both for safety reasons and for easier
handling, we recommend to place the
motor section vertically (impeller pointing upwards) onto
a suitable base when dismantling the unit. Close drain
connection 11 E.
Make sure the unit cannot tip over during
dismantling and reassembly! Risk of personal
injury!
3
Dismantling the impeller
Hold the impeller with a belt wrench at the impeller eye.
Undo impeller nut 920.95 and disc 550.87. Then remove
the impeller with a suitable pull-off device.
4.
Dismantling the rotor
-- Motors DE 90
Pull off cup springs 950.23 and thrust bearing 314.01.
Undo hex. nuts 920.04 and pull off casing cover 161. Take
off taper lock ring 515.04. Remove U-ring 411.87. Pull rotor
818 carefully out of the rotor space.
-- Motors DE 112 and 132
Undo nuts 920.15 and take casing cover 161 off bearing
bracket lantern 344, remove taper lock ring 515.04. Pull
cup springs 950.23 and thrust bearing 314.01 off the rotor.
Undo nuts 920.04 and remove bearing bracket lantern
344. Remove U-rings 411.11/.87. Pull rotor 818 carefully
out of the rotor space.
-- Motors DE 160 and 200
Pull off cup springs 950.23 and thrust bearing 314.01.
Remove socket head cap screws 914.07. Use jacking
thread to pull bearing ring carrier 391.01 out of casing
cover 161.
Undo hex. nuts 920.04 and lift off casing cover 161.
Remove U-ring 411.87. Pull rotor 818 carefully out of the
rotor space.
General:
Do not tilt the rotor when pulling it out, to prevent damage
to the motor end plain bearing or the can. Larger motors
are best dismantled in vertical position. For this purpose,
a lifting eye nut is fitted to the rotor instead of impeller nut
920.95. A crane can be used now to pull the rotor carefully
out of the rotor space.
5.
Dismantling the bearings
Pull bearing sleeve 529.21 and thrust bearing 314.02 off
the rotor.
Remove hex. socket head cap screw 914.80 or hex. nut
920.80 on DE 160/200 (Caution! Left-hand thread!) as well
as cup springs 950.11.
Pull taper lock rings 515.23, 515.24 and bearing sleeve
529.06 off the shaft end.
Remove nut 920.36 and pull off bearing carrier 382.
(Caution! Left-hand thread!)
Remove U-ring 411.48 and O-ring 412.22.
6.
Checking the can and the motor winding
Inspect the can for damage after having removed the rotor.
Use a suitable measuring instrument to measure the
insulation resistance of the motor winding (e.g. 1000 V
magneto). The resistance towards ground shall not be
less than 5 M
.
If the can is found to be damaged and/or the insulation
resistance of the motor winding is too low, there may be
leaks in the can.
If no damage can be found, proceed as described in
item 9.
Watch out for possibly hazardous medium
residues (protective clothing). Collect and
properly dispose of any medium residues which might
escape!
Both for safety reasons and for easier
handling, we recommend to place the
motor section vertically (impeller pointing upwards) onto a
suitable base when dismantling the unit. Close drain
connection 11 E.
Further dismantling of the drive section will affect
the flameproof enclosure of the motor and result in
the temporary suspension of the explosionproof status of
the pump set. The applicable regulations of EC directive
94/9/EC shall be observed.
Further dismantling, e.g. of terminal box
base 81-36 and cover 812, is only
required if the can or winding have been damaged and
other unit components have to be cleaned.
Normally, the motor unit should not be re-used in this
case.
In the event of a can defect, hazardous vapours
and liquids may escape from the stator space!
Take the necessary precautions (wear protective
glasses/clothes, collect residues) when removing
terminal box base 81-36 and cover 812.