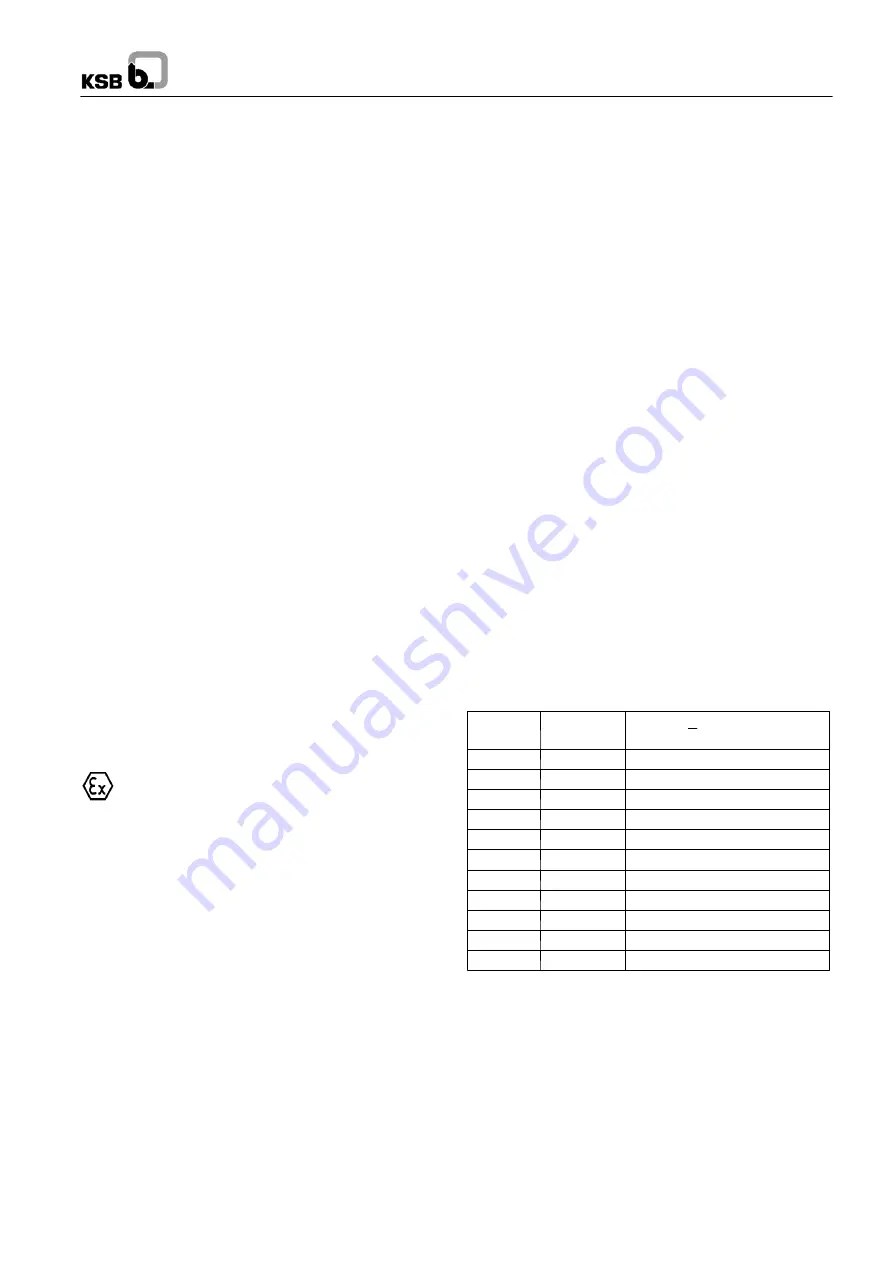
L
Secochem-Ex
9
4.3.1
Functional description
The Secochem-Ex (SCX) pump is a seal-less canned motor
pump. Fig. 3 illustrates its general design.
The hydraulic system and the motor are firmly connected and
form a close-coupled unit. Both impeller (1) and rotor (2) are
arranged on a common shaft (3) running in plain bearings (4
and 5) which are lubricated by the medium handled. The rotor
space is sealed off towards the stator space by the can (6). The
can, made of corrosion-resistant material, rests on the stator (7)
and the support sleeves (8) to compensate the forces resulting
from the pressure within the rotor space.
The bearings are lubricated by the medium handled in the rotor
space. When the pump is started up, the medium enters the
rotor space through the bores (9, 10) and vents the rotor space
through a bore in the shaft.
The partial flow tapped from the medium flow through the bores
(9 u. 10) surrounds the rotor during pump operation and enters
an axial bore provided at the rear end of the rotor shaft. The axial
bore ends at the front face of the impeller-side shaft end.
The pressure difference between the bores (9 and 10) and the
outlet of the axial bore through the shaft at the impeller-side
shaft end results in a continuous partial flow of pumped product.
As this partial flow passes through the circular clearance
between the rotor and the can, it dissipates the heat losses
generated in the motor.
The intensive exchange of liquid from the hydraulic space to the
rotor space and back to the suction side of the hydraulic system
at the same time ensures sufficient lubrication of the plain
bearings.
The pump set is connected to the electric power supply via the
terminal box (11).
Depending on the technical version, additional equipment such
as temperature sensors for monitoring the rotor space
temperature (PT100) and/or PTC resistors for monitoring the
winding temperature can be provided in the motor.
4.3.2
Pump casing
Radially split, consisting of volute casing and casing cover.
The connection dimensions at the volute casing are in
accordance with DIN EN 22858 / ISO 2858.
For handling combustible media, the pump casing must
be made of ductile material with a maximum magnesium
content of 7.5 % (see EN 13463-1). This is a standard feature
in all KSB supplies.
4.3.3
Impeller type
Closed radial impeller with multiple vanes. Axial thrust is
balanced by back vanes.
4.3.4
Drive
Explosion-proof three-phase asynchronous canned motor,
type of protection IP 55 (EN 60034-5). Explosion-protection as
per directive 94/9/EC and EN 60034-1. Stator space in
“flameproof enclosure”, terminal box in “increased safety”. The
rotor space must be filled with the liquid to be pumped at all
times.
The motors are suitable for frequency inverter operation in the
frequency range from 25 Hz (min.) to 50 or 60 Hz (max.),
depending on the nominal motor frequency they are designed
for. To ensure explosion protection, the PTC resistors in the
motor winding must be connected, This prevents an
inadmissible heat build-up in the motor.
General motor data:
Starting method:
all motors d.o.l.
Voltages:
50 Hz: 400V, 500V, 690V
1)
60 Hz: 480V, 600V
Voltage tolerance:
+/- 10 %
Explosion protection:
directive 94/9/EC
Identification:
II 2 G Ex de IIC T.. Gb
3)
Temperature class (T..):
T6, T5, T4 or T3
Enclosure EN 60034:
IP 55
Thermal class:
H
Operating mode:
S1
2)
Monitoring:
PTC (optional)
Frequency inverter operation: possible in combination
with PTC:
Motor supply voltage limits:
du/dt
< 1000 V/
s
Û
< 1000 V
4)
Ambient temperature of
motor:
--20
_
C to +40
_
C
1) 690 V not available for motors 12, 22, 402 and 552
2) See also Section 6.2.2, ”Switching frequency”
3) See also Section 2.10.1, ”Marking”
4) At motor size DE 200: Û < 890 V
For specific motor data please refer to the data sheet!
4.3.5
Bearings
The shaft runs in product-lubricated plain bearings. Axial
movement of the rotor is limited by thrust bearings.
4.3.6
Noise characteristics
Motor code Motor size
DE
Surface sound pressure level
pA [dB]
1)
12
90.2-1.1
49
22
90.2-2.2
49
42
112.2-4
52
52
112.2-5.5
53
72
132.2-7.5
55
112
132.2-11
58
152
132.2-15
60
222
160.2-22
65
302
160.2-30
67
402
200.2-40
69
552
200.2-55
70
1) Spatial average value; as per ISO 3744 and EN 12639.
Applies within the operating range of the pump of Q/Q
opt
= 0.8 - 1.1 and
in non-cavitating pump operation. If noise levels are to be guaranteed,
add an allowance of 3 dB for measurement and manufacturing
tolerance.