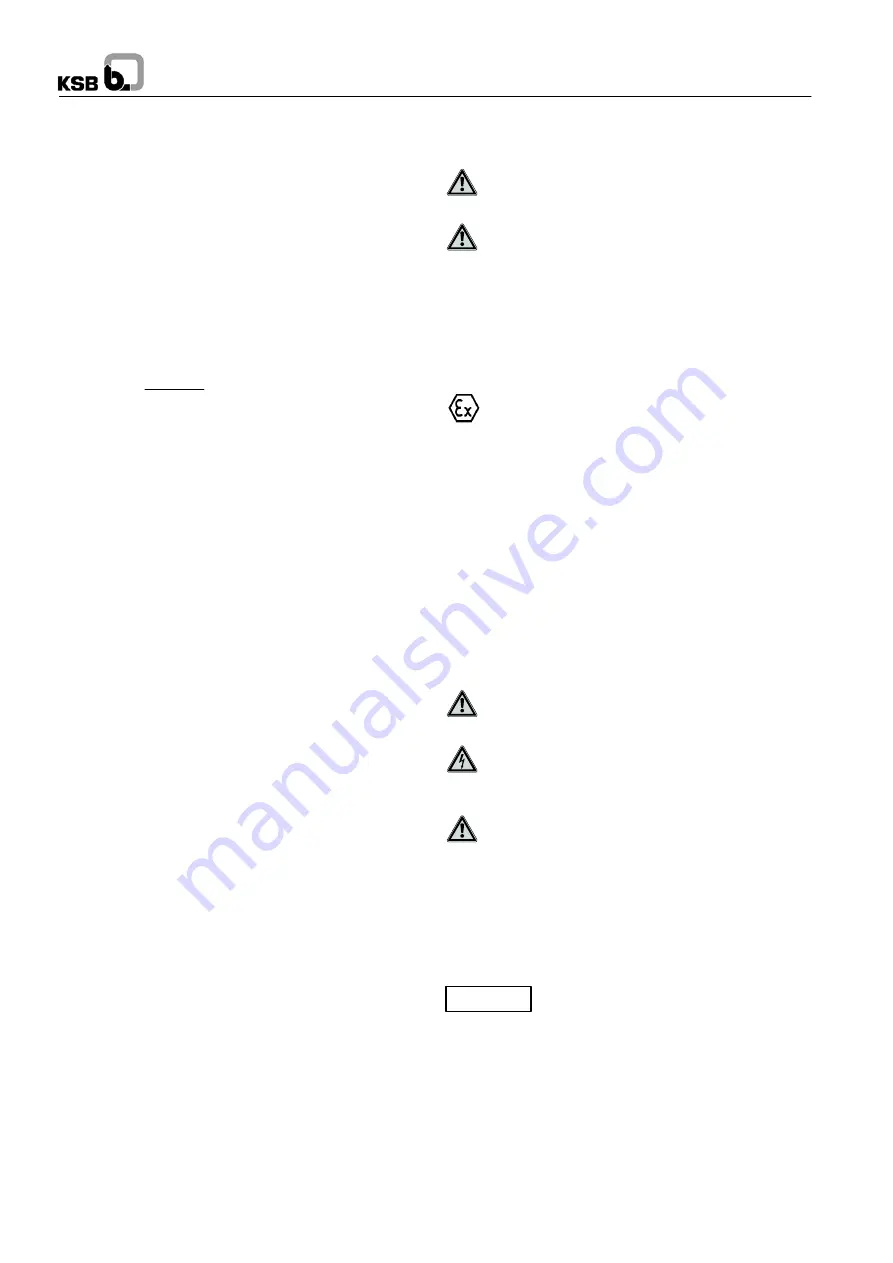
Caution
Secochem-Ex
16
6.2.5
Minimum/maximum flow
Unless specified otherwise in the characteristic curves or on the
data sheets, the following applies:
Q
min
=
0.05 x Q
opt
for short operation
Q
min
= 0.3 x Q
opt
for continuous operation
Q
max
= 1.1 x Q
opt
for 2-pole operation
Q
opt
= optimum efficiency
The data refer to water and water-like liquids. However, if the
physical properties of the media handled are different from
water, the calculation formula below must be used to check if an
additional heat build-up may lead to a dangerous temperature
increase at the pump surface. If necessary, the minimum flow
must be increased.
T
o
= T
f
+
g * H
=
* ( 1 -
)
c *
c
Specific heat
[J / kg K]
g
Acceleration due to gravity
[m/s
2
]
H
Pump head
[m]
T
f
Temperature of medium handled
[
C]
T
f
Temperature of casing surface
[
C]
Pump efficiency at duty point
[--]
Temperature difference
[
C]
6.3
Shutdown / storage / preservation
Each KSB pump leaves the factory carefully assembled. If
commissioning is to take place some time after delivery, we
recommend that the following measures be taken for pump
storage.
6.3.1
Storage of new pumps
-- New pumps are supplied by our factory duly prepared for
storage. Maximum protection for up to 12 months, if the
pump is properly stored indoors.
-- Store the pump in a dry and protected location.
6.3.2
Measures to be taken for prolonged shutdown
1.
The pump remains filled and installed (periodic check
of operation)
In order to make sure that the pump is always ready for
instant start-up, start up the pump set regularly once a
month or once every 3 months for a short time (approx.
5 minutes) during prolonged shutdown periods, provided
the medium does not change during pump shutdown
(freeze, polymerize, etc.). The instructions set forth in
section 6.1 ”Commissioning” shall be adhered to.
2. The pump is removed from the pipe and stored
Before putting the pump into storage, carry out all checks
specified in paragraphs 7.1 to 7.4. Then apply appropriate
preservatives:
-- Spray-coat the inside wall of the pump casing, and in
particular the impeller clearance areas, with a
preservative. Spray the preservative through the
suction and discharge nozzles. It is advisable to close
the pump nozzles (e.g. with plastic caps or similar).
-- Do not fill the pump with preservative!
6.4
Returning to service after storage
Before returning the pump to service, carry out all checks and
maintenance work specified in sections 7.1 and 7.2.
In addition, the instructions laid down in the sections on
”Installation at site” (5) and ”Commissioning” (6) must be
observed.
Immediately following completion of the work, all
safety-relevant and protective devices must be
re-installed and/or re-activated.
7
Servicing / Maintenance
7.1
General instructions
Sparks produced during servicing work
Explosion hazard!
The safety regulations in force at the place of
installation!
Always perform maintenance work on
explosion--proof pump sets outside potentially
explosive atmospheres.
The operator is responsible for ensuring that all maintenance,
inspection and installation work be performed by authorized,
qualified specialist personnel who are thoroughly familiar with
the manual.
If properly handled and operated in line with its design data, this
pump set is maintenance-free. The unit only has to be checked
in the case of rough running, noise, vibrations > 3.0 mm/s v
eff
,
motor cutout or similar.
A regular maintenance schedule will help avoid expensive
repairs and contribute to trouble-free, reliable operation of the
pump with a minimum of maintenance expenditure and work.
The pump must have cooled down to ambient
temperature, pump pressure must have been
released and the pump must have been drained.
Work on the unit must only be carried out with the
electrical connections disconnected. Make sure
that the pump set cannot be switched on accidentally
(danger of life!).
Pumps handling liquids posing health hazards
must be decontaminated. When draining the
medium see to it that there is no risk to persons or the
environment. All relevant laws must be adhered to (danger
of life)!
7.2
Servicing / Inspection
7.2.1
Supervision of operation
The pump must run quietly and free from
vibrations at all times. The pump must never be
allowed to run dry.
Examples of monitoring systems in the plant which may prevent
the pump from running dry if liquid feed should be interrupted:
1. Pressure switch
2. Flow control unit
3. Level control unit (for rotor space)
4. Level control unit (for plant system)
5. Pump power monitoring unit
6. Current control unit
In most cases, a well-proven monitoring system is already
installed in the plant.