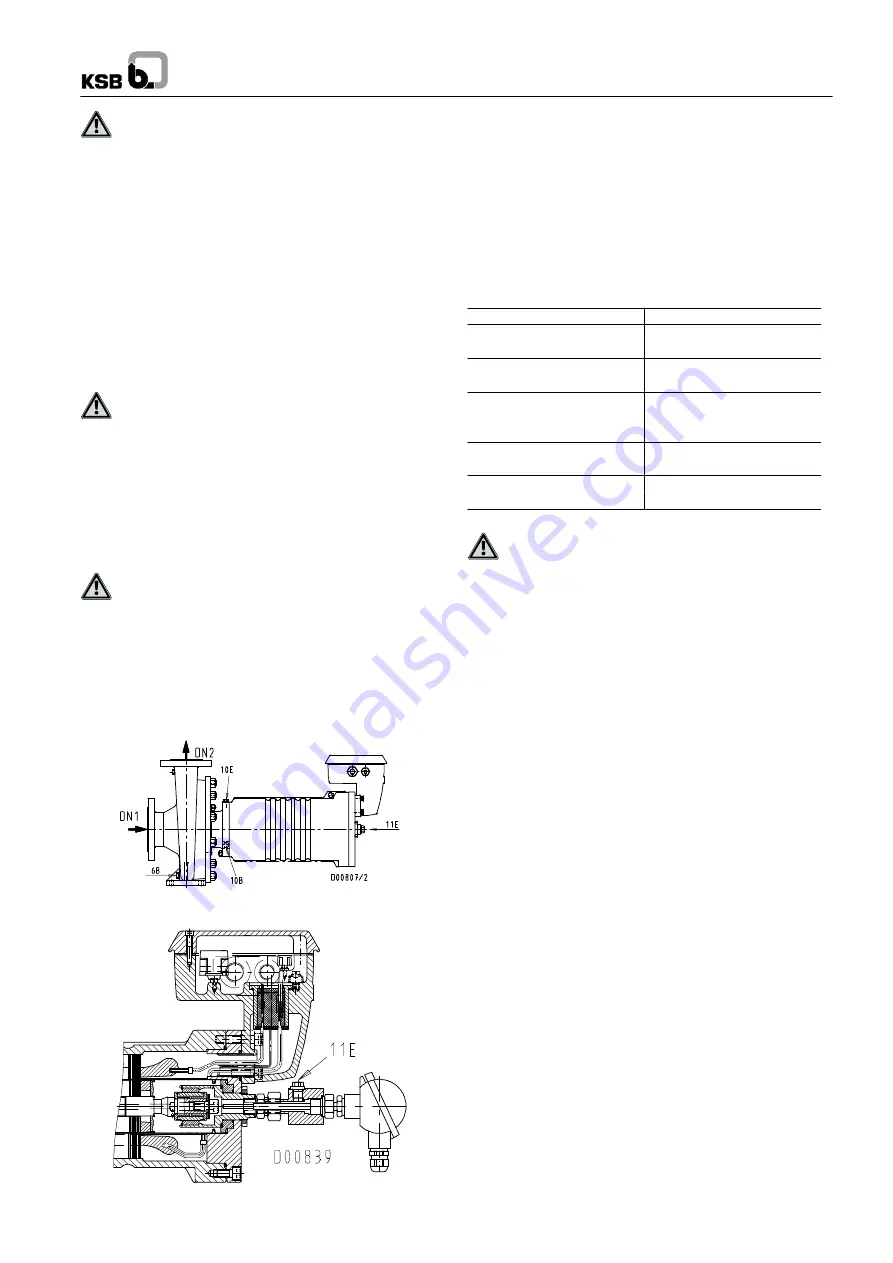
Secochem-Ex
17
Prolonged operation against a closed shut-off valve is
not permitted. When operating the pump set against a
closed shut-off valve in the discharge line for a short period of
time, the permissible pressure and temperature limits must not
be exceeded.
The shut-off elements and the auxiliary feed lines must not be
closed during operation.
Check all flange connections for tightness and re-tighten, if
necessary.
7.2.2
Bearings
The plain bearings only need to be checked if vibrations
exceeding 3.0 mm/s v
eff
, unusual noise and an increase in
power input occur while operating conditions remain
unchanged.
7.3
Drainage / Disposal
If the pump was used for handling liquids posing health
hazards, see to it that there is no risk to persons or the
environment when draining the medium. All relevant laws must
be heeded. If required, wear safety clothing and a protective
mask!
If the media handled by the pumps leave residues which might
lead to corrosion when coming into contact with atmospheric
humidity, or which might ignite when coming into contact with
oxygen, then the unit must be flushed through, neutralized, and
then for drying purposes anhydrous gas must be blown through
the pump.
Before draining the pump, secure it so as to make sure
it cannot be switched on accidentally. The shut-off
valves in the suction and discharge lines as well as the auxiliary
feed lines (e.g. barrier liquid) must be closed.
The pump must have cooled down to ambient temperature.
To drain the medium handled from the standard pump design
(internal circulation), use connection 6 B, or connection 10 B to
also drain the rotor space of pumps with barrier liquid feed
(motor cooling by means of external liquid feed or partial flow
from main flow filter). See Fig. 14.
Fig. 14(without temperature measuring point in the rotor
space)
Fig. 15(with temperature measuring point in the rotor space)
After drainage, the pump set can be flushed through. To flush
the pump, also open connection 11 E and connect the flushing
device.
Connection 11 E (G 1/2) see Fig. 14
Connection 11 E (G 1/4) see Fig. 15
Flush the pump set towards the suction side for a few minutes.
Assess the condition of the drained liquid with a view to the
safety regulations governing the application in question
(concentration, colour, smell, etc.). The pumped product is
largely removed from the pump in this way. Refer to the liquid
contents of the drive section given in table 7.3 for orientation.
Liquid content of the drive section (rotor space)
Motor size DE
Content (litres)
90.2-1.1
0.3
90.2-2.2
0.3
112.2-4
1.1
112.2-5.5
0.8
132.2-7.5
1.7
132.2-11
1.7
132.2-15
1.2
160.2-22
2.8
160.2-30
2.8
200.2-40
7.6
200.2-55
5.5
Table 7.3
Prior to sending the unit in for inspection/repairs, if any,
or dismantling it (cf. 7.4), make sure it is flushed
carefully, and see to it that any liquid residues are drained and
properly disposed of.
For further details please refer to the certificate of
decontamination in Section 11, which must be completed and
added to the shipping documents.
7.4
Dismantling
7.4.1
Fundamental instructions and recommendations
Repair and maintenance work to the pump must only be carried
out by specially trained personnel, using
original spare parts
.
Important information on the dimensions of the flameproof
joints: section 2.7, page 5.
Observe the safety regulations laid down in section 7.1.
Dismantling and reassembly must always be carried out in
accordance with the relevant general assembly drawing.
The general assembly drawing and other relevant
documents are found in the annex. The dismantling
sequence can be derived from the general assembly
drawing.
In case of damage you can always contact our service
departments.
7.4.2
Dismantling (general)
1.
Disconnecting the electrical connections
Remove the cover of the terminal box. Then disconnect
the main and auxiliary connections.
Unscrew the screwed inserts of the two cable glands (one
half remains in the base of the terminal box) and remove
the cables.
2.
Removing the pump set/back pull-out unit from the
piping and dismantling the pump casing
After draining and flushing the pump set as described in
section 7.3, close connections 11 E, 6 B and, if applicable,
10 B again.
If the complete pump set is to be removed from the piping,
proceed as described in para. 2a.
If the pump casing is to remain installed in the piping,
however, and only the back pull-out unit is to be removed,
proceed as described in para. 2b.