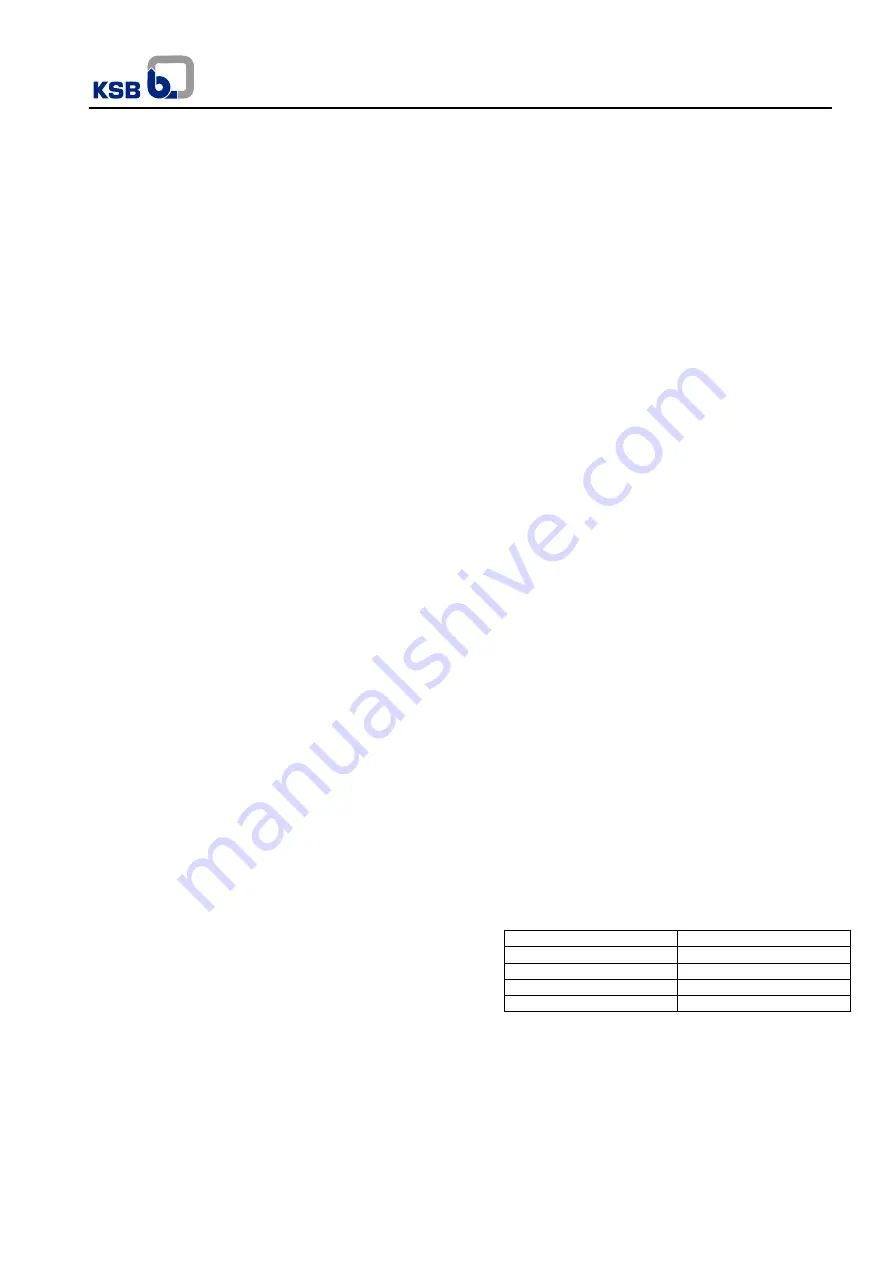
9
Meganorm
b) Motor current consumption (amperage) must be controlled
as well as network voltage value.
c) Assure that suction pressure value corresponds to the
designed one.
d) Assure that pump runs vibration-free and without unusual
noises. Vibration criteria in accordance to Hydraulic
Institute.
e) Check bearing temperature that may reach 122ºF (50ºC)
over ambient temperature. However the sum of bearing
temperature and ambient temperature should not exceed
197ºF (90ºC).
f) Adjust the packing by tightening gland cover nuts about 1/6
turn. Like any new packing, it is required a certain period to
set. The new packing should be checked during the first 5
to 8 hours of operation and in the event of leakage in
excess, the gland cover nuts should be tightened about 1/6
turn again. During normal operation, packing should drip.
When packing reach the set stage, a weekly inspection
should be enough. The procedure mentioned above should
be practiced every 15 minutes over the first 2 hours of
operation. If all tests pass, new checking should be carried
out every hour, until the first 5 to 8 running hours (pumps
with packing).
g) At the operation beginning, the pump with mechanical seal
may have a little leakage through that. This leakage must
stop after sealing faces accomodation.
10.3
Operation supervision
Depending on the availability of personal and on the
importance of the pump, we recommend the following
supervision.
In case of any irregularity, the maintenance
supervisor should be called immediately
.
10.3.1 Weekly
supervision
Check:
a) Operating point of the pump.
b) Electric motor consumed current and network voltage.
c) Suction
pressure.
d) Vibrations and irregular noises.
e) Oil level.
f) Packing
leakage.
10.3.2
Monthly supervision
Check:
a) Oil change interval. Consult chapter 11.2.
b) Bearings temperature.
10.3.3 Semestral
supervision
Check:
a) Fixing bolts on pump, driver and base.
b) Alignment of the motor-pump assembly.
c) Coupling lubrication (if any).
d) Replace packing if necessary (if any).
e) Check the mechanical seal (if any), if their sealing
faces are worn-out, scratched or broken. Replace it if
necessary.
10.3.4 Annual
supervision
a) Disassemble the pump for maintenance. After
cleaning, inspect condition of ball and roller bearings
(very carefully), radial seal rings, gaskets, o-rings,
impellers, internal areas of the volute casing (check
also thickness), wear areas and coupling.
10.4 Shutdown
procedure
Follow in sequence these instructions:
a) Shut off pump discharge valve.
b) Turn off the driver and observe the gradual and
smooth stop of the rotating assembly.
c) Close the suction valve (if any).
d) Close the auxiliary pipelines (if there is no restriction).
11. Maintenance
11.1 Bearing
maintenance
Maintenance purpose here is to increase bearing system
useful life as long as possible. While pump is operating,
the maintenance consists in controlling the ball bearings
temperature and the bearing bracket oil level.
The pumps are delivered from the factory without oil
in the bearing bracket.
NOTE:
Table of oil quantity to fill KSB MEGANORM
pumps bearing bracket.
Bearing Bracket
Oil quantity - ml (in
3
)
A 30
100 (6.10)
A 40
170 (10.37)
A 50
200 (12.2)
A 60
480 (29.30)
Table 4