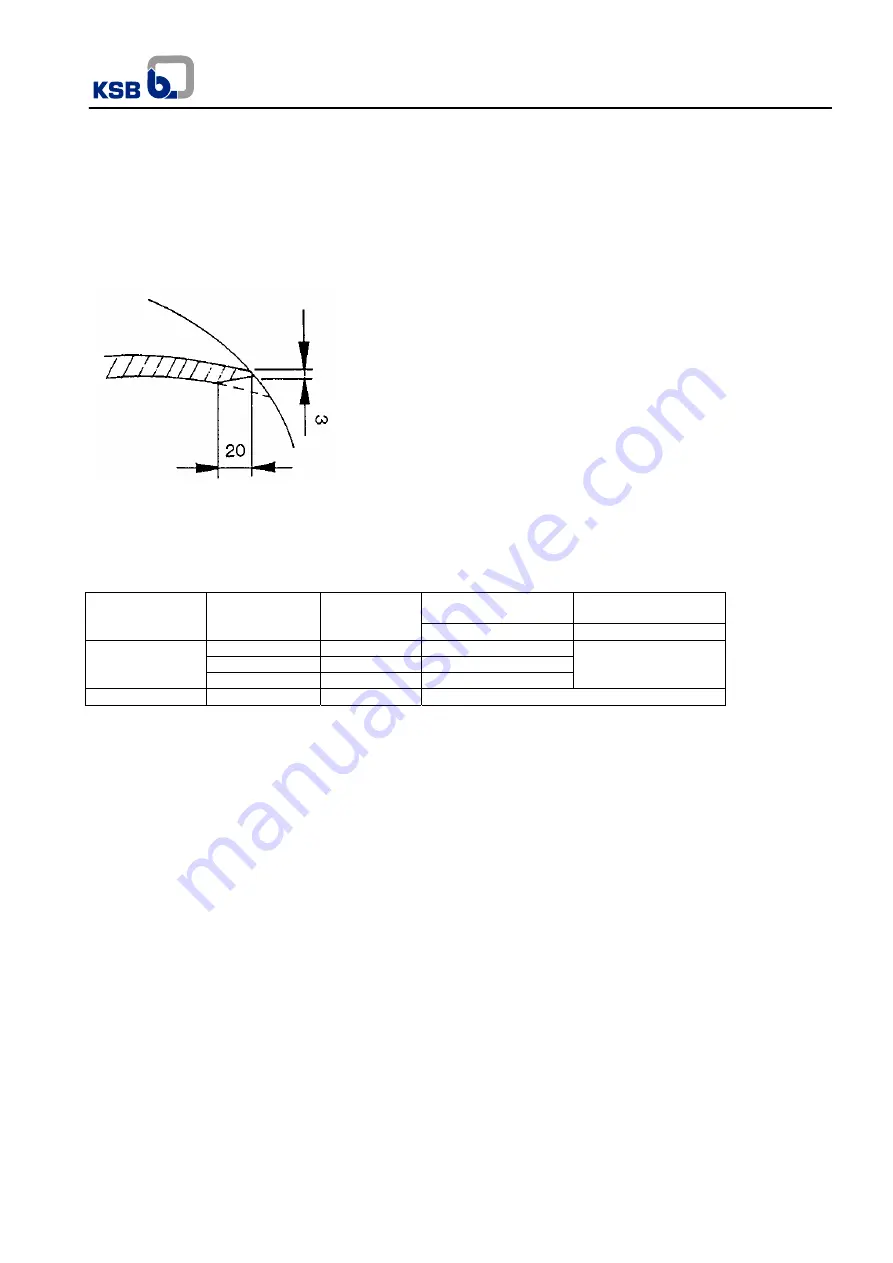
15
Meganorm
14. Special recommendations
14.1 Machining of the impeller external diameter
All impellers made of stainless steel have their vanes
adjusted (sharpened) at the outlet area of the liquid being
pumped, according to the illustration on fig.17, when the
impellers have been trimmed in their external diameter by
machining.
(0.787”)
Fig. 17 - Adjusting the Impeller Vanes
14.2 Shaft run-out on the impeller region
Verify the shaft run-out. Arrange the bearing bracket
mounted with the shaft on vertical position and check
the run-out on the shaft end with a dial comparator
within the maximum limit of 0,05 mm (0,002”).
15. Pressure limit X Maximum temperature
ANSI B16.1 Flange
125 #
ANSI B16.1 Flange
250 #
Shaft sealing
Temperature
º F
Temperature
º C
Pressure [ bar ] / [psi]
Pressure [ bar ] / [psi]
-18,4 up to 149
- 28 up to 65
12 / 174
199
93
11 / 160
Gland packing
221
105
10 / 145
16 / 232
Mechanical seal
194
90
10 / 145
Table 7
16. Wearing areas maintenance
Change the wear rings of volute casing and / or casing cover
(if any) when they are wornout and the impeller in good
condition.
KSB and Dealer Network supply wear rings to repair or as
spare parts to be applied for KSB Meganorm pumps.
These wear rings are supplied with suitable tolerance of the
outside diameter and 2mm (0,05”) of extra material of the
inside diameter.
16.1 When the exchange mist be made
The wear ring exchange must be made when the
clearance between the impeller and the wear ring is
three times longer than the original clearance that is
0,3mm (0,01”).
Note: KSB reserves the right to modify the information presented in this manual without prior notice.
(0.12”)