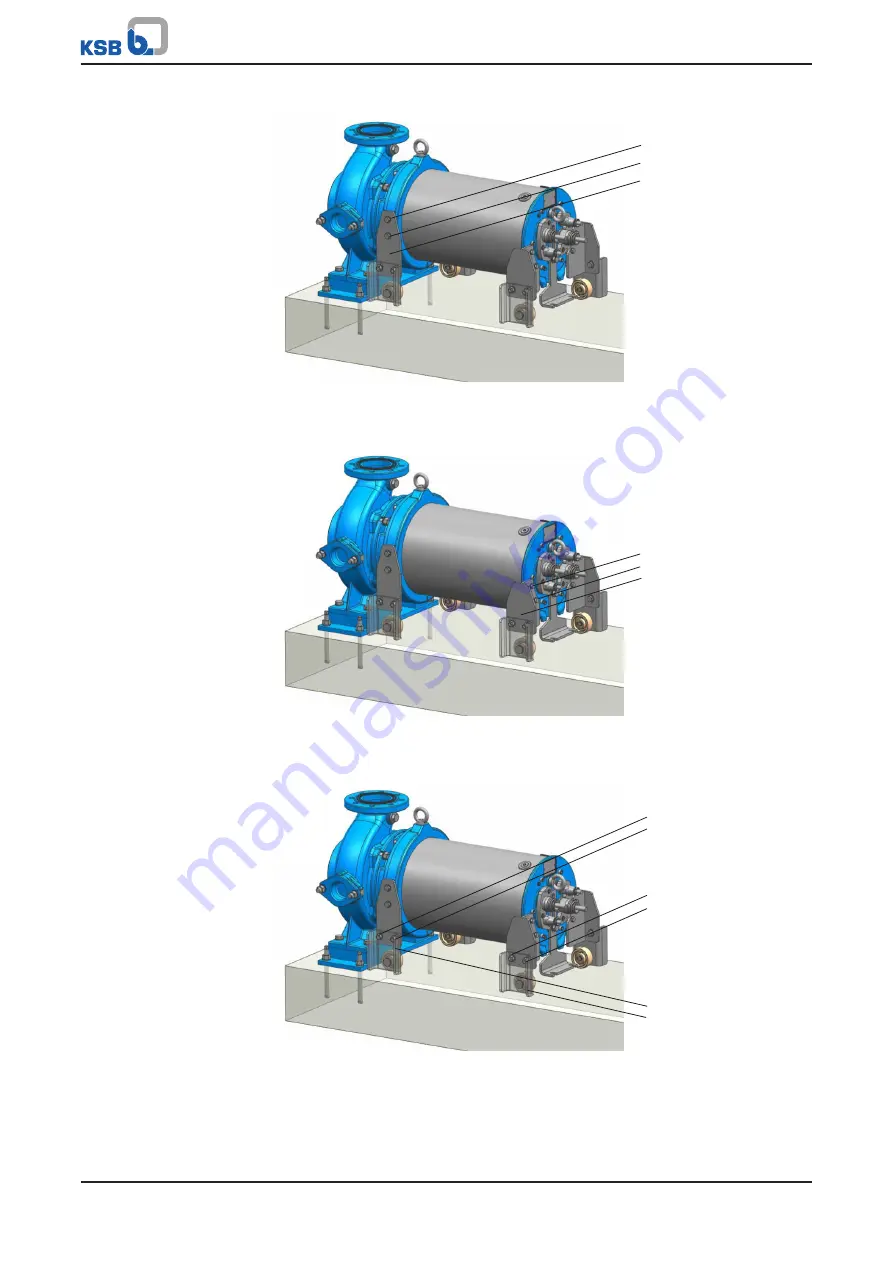
5 Installation at Site
17 of 32
AmaSlide
2553.870/01-EN
82-5.01
901.57/550.57
901.57/550.57
Fig. 5:
Fitting the pump-end adapters on both sides
6. Tighten hexagon head bolts/discs 901.57/550.57 at both adapters 82-5.01.
82-5.02
901.58/550.58
901.58/550.58
Fig. 6:
Fitting the motor-end adapters on both sides
7. Tighten hexagon head bolts/discs 901.58/550.58 at both adapters 82-5.02.
55-1
901.62/550.62/920.62
901.62/550.62/920.62
901.62/550.62/920.62
901.62/550.62/920.62
55-1
Fig. 7:
Positioning the guide plates with rollers on both sides
8. Position hexagon head bolts/nuts 901.62/550.62/920.62 at the four guide plates
55-1 but do not tighten them yet.