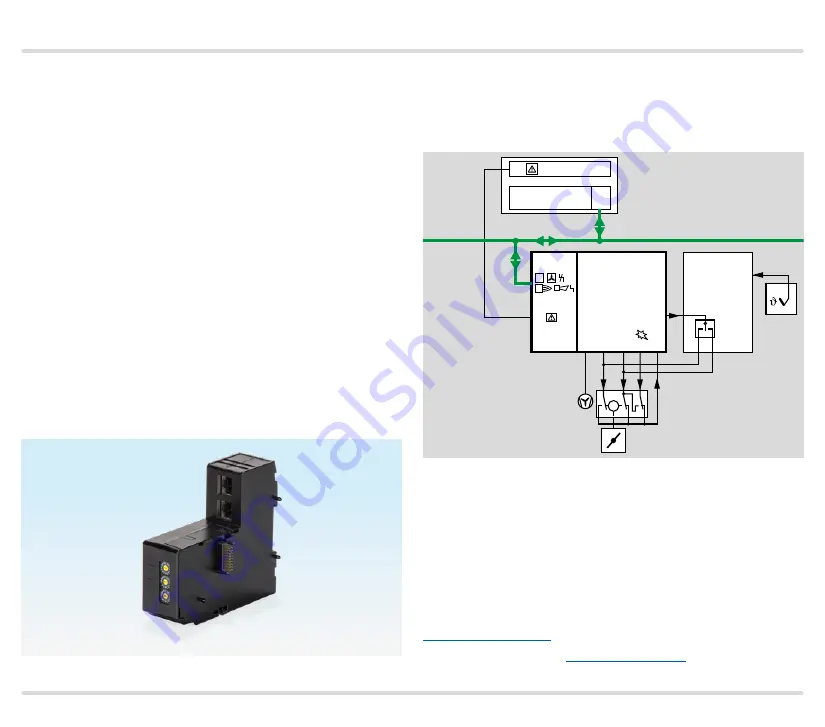
FCU 500, FCU 505 · Edition 02.17
60
Fieldbus communication via Ethernet
9 .1 FCU and bus module BCM
The optional bus module BCM 500 is required to inte-
grate the FCU in a fieldbus system (Profinet IO or Mod-
bus TCP).
Control signals (for start, reset and air actuator control),
signal states from the device inputs and outputs and
information about the device status (operating states
and current program step), warnings and faults can be
transferred via the bus module between the FCU and
PLC.
Bus module BCM 500 has two RJ45 connection sock-
ets for connection to the fieldbus on its front. The con-
nection sockets are combined with an internal 2-port
switch. This allows the BCM 500 together with the FCU
to be integrated in various network topologies (star, tree
or line topology). Requirements such as Auto Negotia-
tion and Auto Crossover are satisfied.
Safety-related signals and interlocks (e.g. safety in-
terlock) must be routed independently of the fieldbus
communication direct from the FCU to the burner con-
trol units (e.g. BCU) and vice versa.
FCU
BCM
BUS
L1,
L1,
56
M
ϑ
PROFINET/MODBUS TCP
53
58
55 52
54
90°
➔
0
0
➔
90°
3PS
PLC
Temperature
controller
All network components which connect the automation
system and the field devices must be certified for field-
bus use.
For information on planning and the structure of a net-
work and the components to be used (e.g. cables, lines
and switches)
for Profinet, see Profinet Installation Guide at
www.profibus.com,
for Modbus TCP, see www.modbus.org.