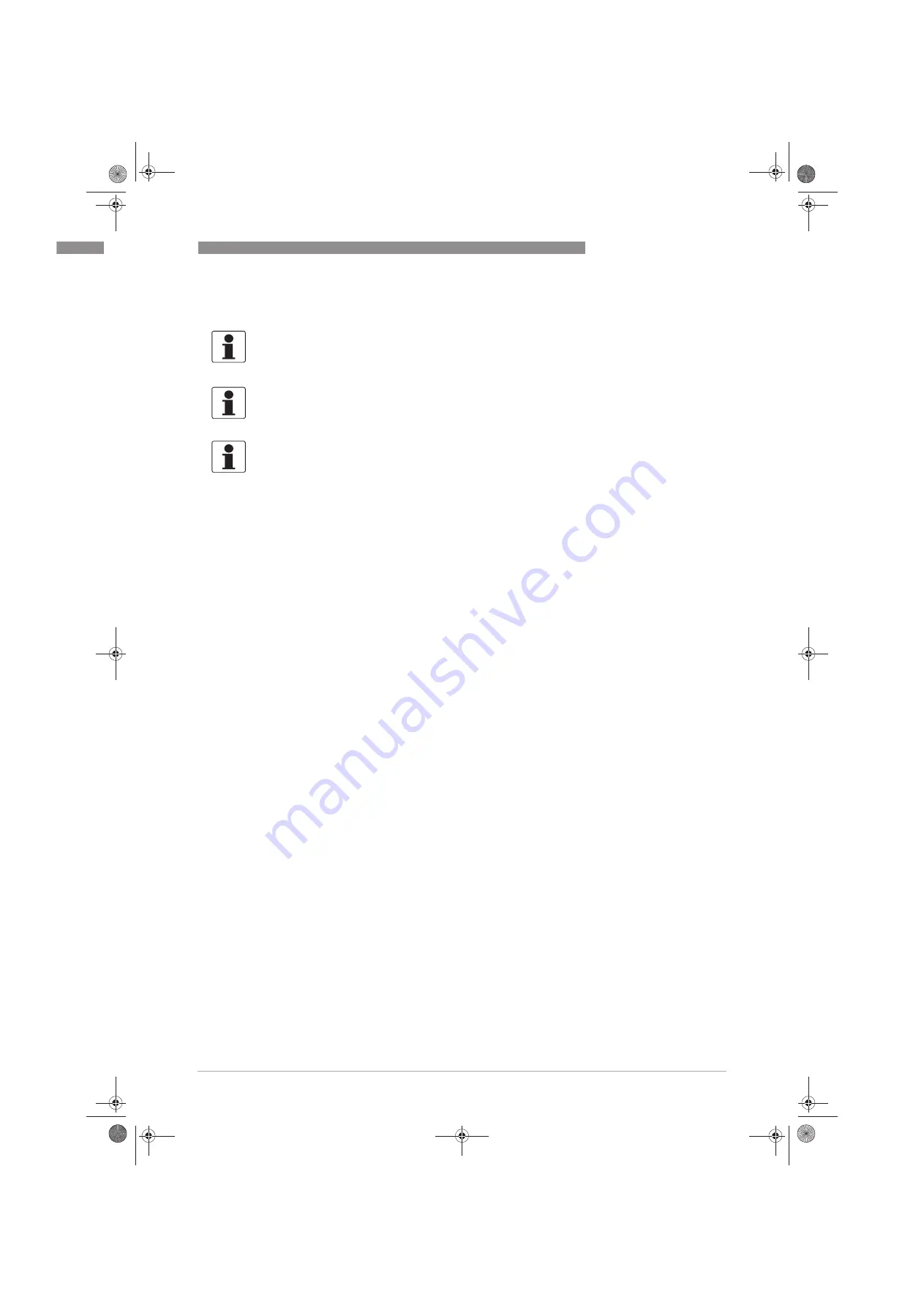
INSTALLATION
3
13
OPTIMASS 2000
www.krohne.com
08/2014 - 4000810003- MA OPTIMASS 2000 R03 en
Installation
3.1 General notes on installation
3.2 Storage
•
Store the device in a dry and dust-free location.
•
Avoid direct exposure to the sun.
•
Store the device in its original packing.
•
Do not allow the ambient temperature to fall below -50
°
C / -58
°
F or rise above +85
°
C /
+185
°
F.
INFORMATION!
Inspect the packaging carefully for damages or signs of rough handling. Report damage to the
carrier and to the local office of the manufacturer.
INFORMATION!
Do a check of the packing list to make sure that you have all the elements given in the order.
INFORMATION!
Look at the device nameplate to ensure that the device is delivered according to your order.
Check for the correct supply voltage printed on the nameplate.
MA_OPTIMASS_2000_en_150206_4000810003_R03.book Page 13 Wednesday, September 30, 2015 5:42 PM