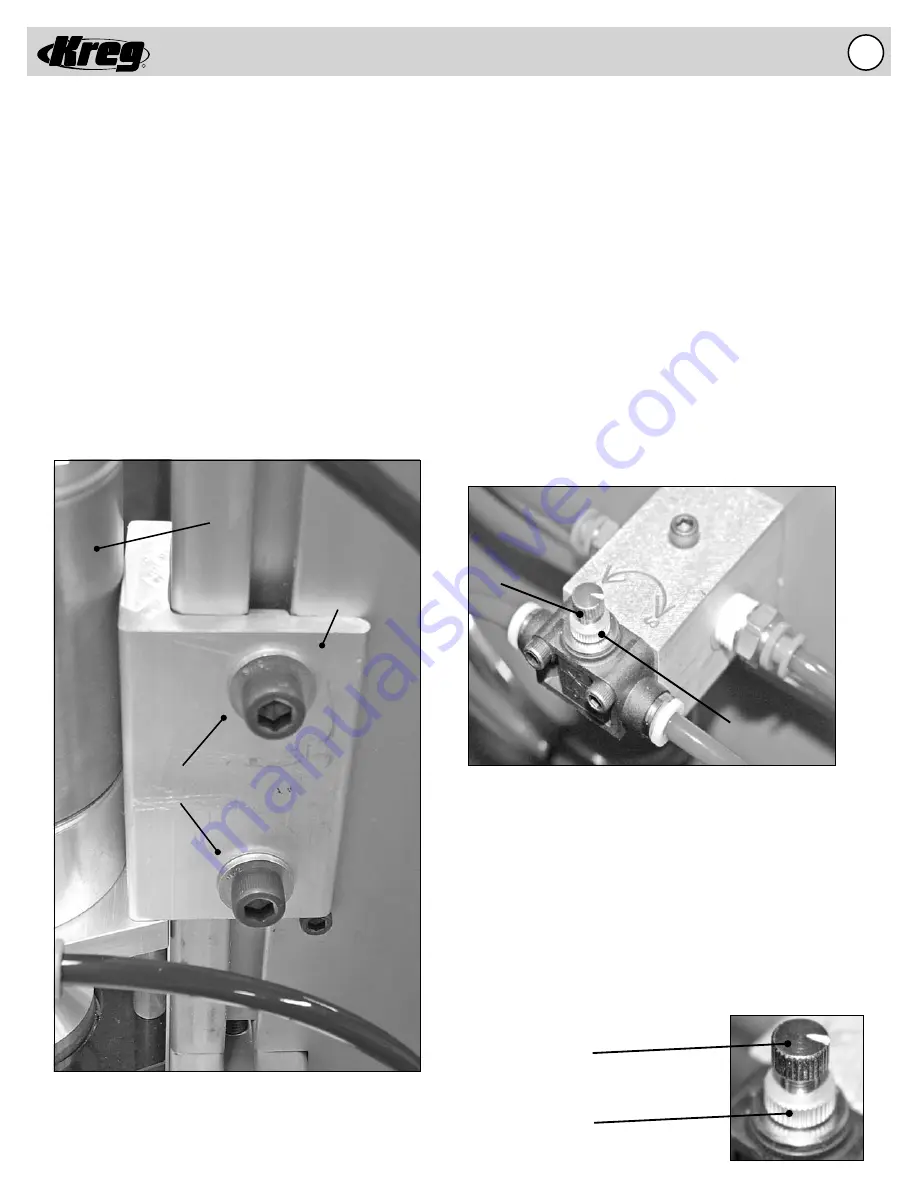
R
DK1100 TP/FP
18
Feed Rate Flow Control
The Feed Rate Control Valve allows the user to adjust the speed at
which the drill bit advances into the material. The factory setting of
this valve will maintain a consistent feed rate for various thicknesses
of different materials to optimize Drill Bit life. The Feed Rate Control
Valve should only be adjusted when a faster or slower rate of
Drill Bit feed is desired. This adjustment is only recommended for
experienced users that consistently drill the same thickness of the
same type of material on a daily basis. The Feed Rate Control Valve
is adjusted by loosening the Locking Collar and rotating the Screw
in the direction of the desired change in feed rate. “F” corresponds
to a Faster feed rate, “S” corresponds to a Slower feed rate. Make
these adjustments carefully as only a slight change in position will
result in a large change of feed rate. Make certain to tighten the
Locking Collar to prevent the Screw from accidentally drifting or
vibrating out of adjustment. If you have changed the setting on the
Feed Rate Control Valve and want to put it back to factory settings,
please follow these simple directions to do so. Turn the locking collar
(counter-clockwise) to loosen it up, then tighten the screw all the way
down (clockwise) to start over. To reset it to the factory setting, turn
the screw (counter-clockwise) 4 complete turns for our DK1100 TP
and DK1100 FP machines. Then tighten the locking collar back down
(clockwise) to prevent the Screw from accidentally drifting or vibrating
out of adjustment.
Clamping Duration Control
Clamping Duration Control allows the user to adjust the duration
that the pneumatic clamp engages the material before, during,
and after the drilling operation is performed. The factory setting of
this valve will maintain the correct amount of time that the material
is clamped while drilling. If the work piece lifts off of the Drill Guide
Plate during drilling then the Clamping Duration Control will need
to be adjusted. Loosen the Locking Collar and turn the Screw in
the clockwise direction to increase the duration (more clamping
time). Turning the Screw in the counter-clockwise direction
decreases the duration (less clamping time). Make certain to
tighten the Locking Collar to prevent the Screw from accidentally
drifting or vibrating out of adjustment.
Locking
Collar
Screw
Screw
Locking
Collar
Adjusting the Clamping Cylinder Height
The Clamping Cylinder can be adjusted for material of different
thicknesses. The factory setting will clamp materials of
approximate thicknesses between 1/2” and 3/4”. For materials
thicker than 7/8”, the Clamping Cylinder will need to be moved
upward to allow the material to locate below the Clamp Pad.
Before adjusting the Clamping Cylinder make certain your
machine is DISCONNECTED from the AIR SUPPLY and/or
ELECTRICAL SUPPLY. Cycle the machine via the foot switch
several times to remove air from the system. Without an air
supply or electrical supply you can be certain the Clamping
Cylinder will not accidentally engage or the drill bit will not rotate
while you are performing maintenance.
Step 1: Loosen the (4) Socket-head Cap Screws (two on each
side) located on the Clamping Cylinder Bracket.
Step 2: Adjust the Clamping Cylinder to allow the material to
pass under the Clamp Pad.
Step 3: Tighten the (4) Socket-head Cap Screws to lock the
Clamping Cylinder in position.
Socket-head
Cap Screws
Clamping Cylinder
Bracket
Clamping Cylinder
Summary of Contents for DK1100 FE
Page 21: ...R NOTES 20...
Page 22: ...R NOTES 21...
Page 23: ...R NOTES 22...
Page 24: ...Kreg Tool Company 201 Campus Drive Huxley IA 50124 800 447 8638 www kregtool com R...