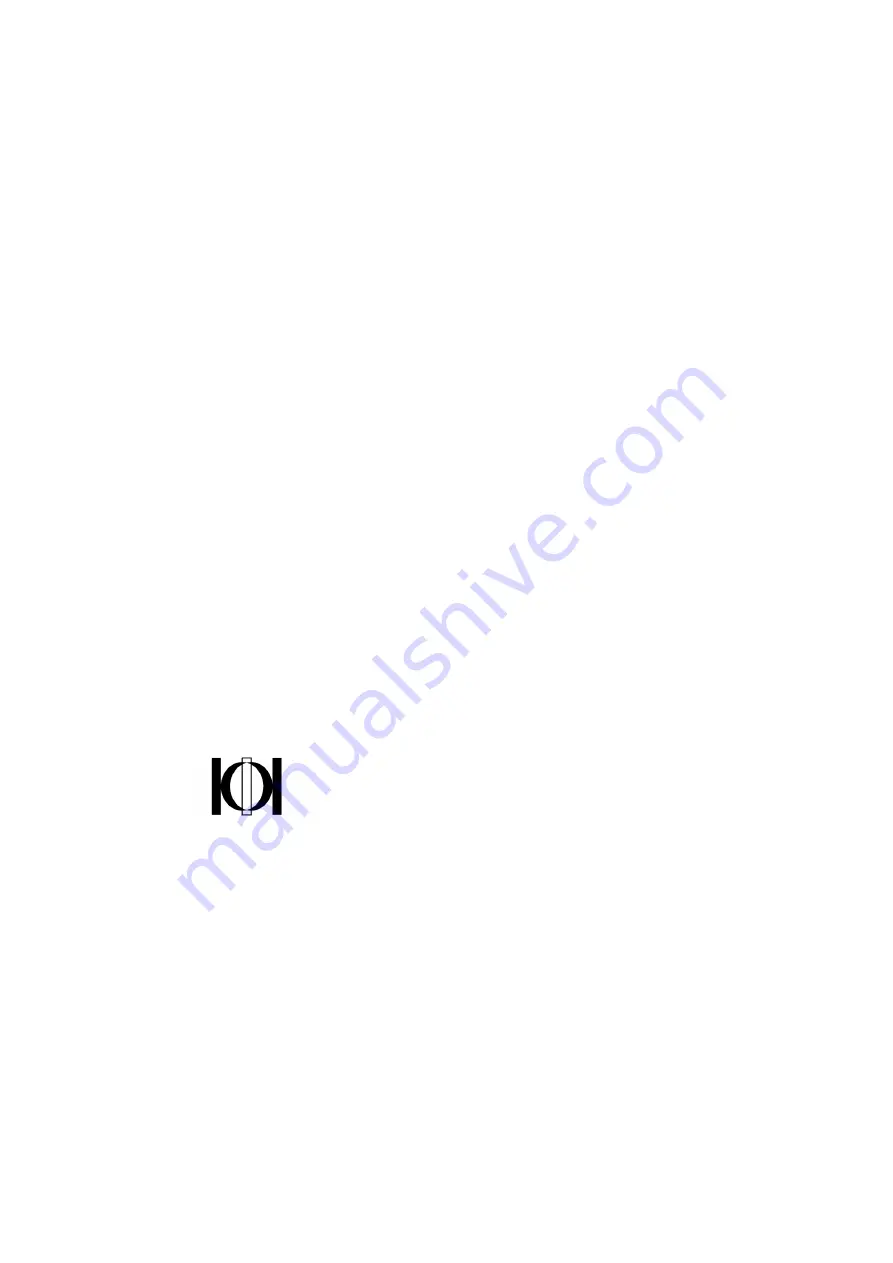
ISO 9001 CERTIFIED
TAIWAN BUSINESS DEPARTMENT:
8FL.,No. 276, Sec.1,Ta-Tung Rd., Hsi-Chih City, Taipei Hsien 221,Taiwan
TEL:886-2-2647-5855 FAX:886-2-2643-1151
CHINA BUSINESS DEPARTMENT:
No. 4, Lane 185, Huan-Ho St., Hsi-Chih City, Taipei Hsien 221,Taiwan
TEL:886-2-2694-8799 FAX:886-2-2694-6657
INTERNATIONAL BUSINESS DEPARTMENT:
No. 4, Lane 185, Huan-Ho St., Hsi-Chih City, Taipei Hsien 221,Taiwan
TEL:886-2-2694-8799 FAX:886-2-2694-6657
KP3828 Series
Maintenance Manual
VER 2.6.
4
9
-2006
KPOWERSCIENCE CO.,LTD.
Summary of Contents for KP3828 Series
Page 4: ...Chapter 1 Overview ...
Page 5: ...1 1 1 1 External View External View ...
Page 17: ...Chapter 2 Principles ...
Page 40: ...Chapter 3 Installation ...
Page 47: ...3 7 Step 13 Remove the nut from the drum shaft Fig 3 7 Nut ...
Page 59: ...3 19 Fig 3 19 AC power terminal box AC cable Breaker Turn on AC power terminal box KMPU board ...
Page 65: ...Chapter 4 Electrical System ...
Page 72: ...Chapter 5 Adjustments ...
Page 88: ...5 16 Fig 5 16 Fig 5 17 ...
Page 90: ...Chapter 6 Periodic Maintenance ...
Page 96: ...6 6 6 3 3 Developing Unit Hopper Area Fig 6 3 6 3 4 Cleaning Unit Area Fig 6 4 Cleaning unit ...
Page 105: ...6 15 2 Wipe the drum surface with the special cloth Fig 6 14 Drum Special cloth ...
Page 113: ...Chapter 7 Parts Replacement ...
Page 172: ...Chapter 8 Troubleshooting ...
Page 230: ...Appendix I KMPU Circuit Diagram ...