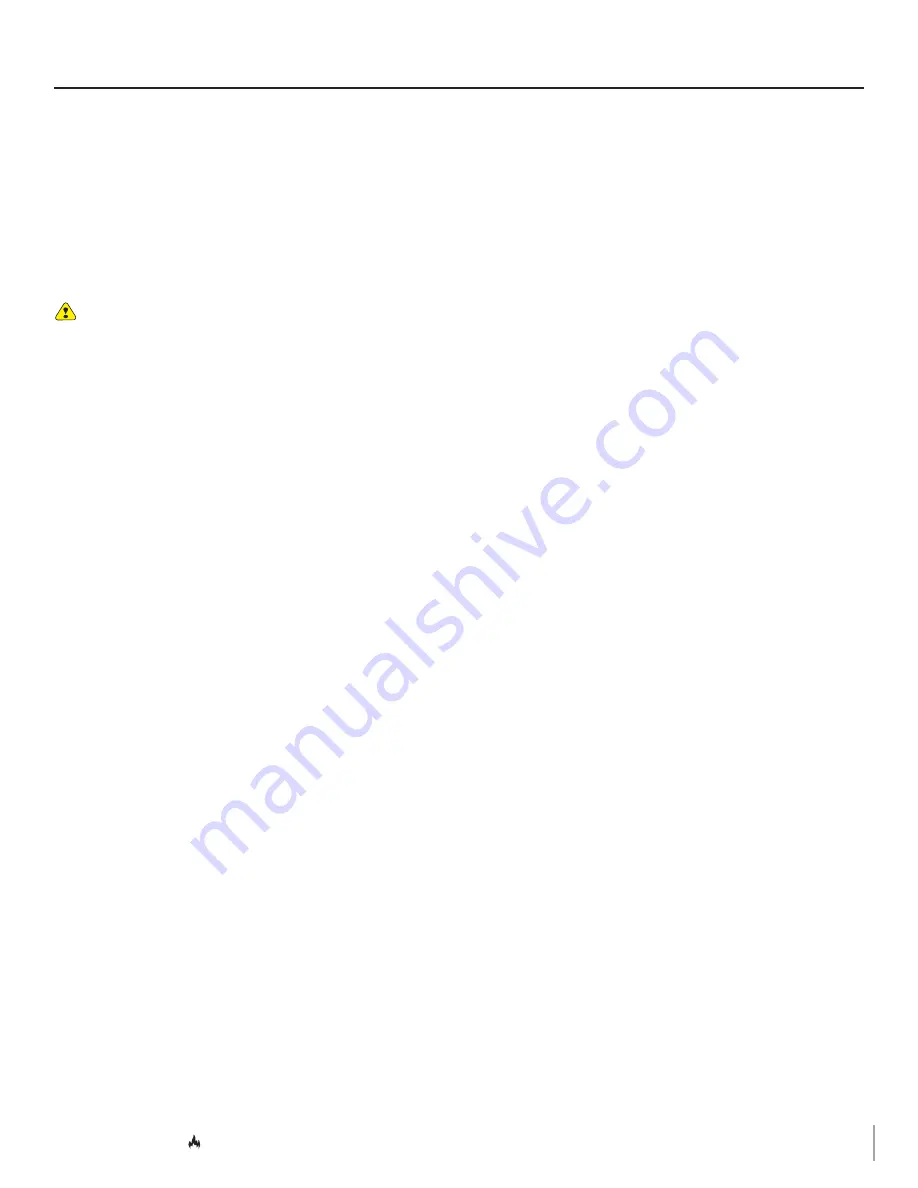
Appliance Certification–Requirements for Massachusetts
SECTION 1
INTRODUCTION
#SFD-36
R.6 February 2022
#SFD-36
R.6 February 2022
7
HUSSONG MFG. CO., INC.
KOZY HEAT FIREPLACES
1.1 Appliance Certification
Laboratory: PFS in Cottage Grove, Wisconsin
Standards:
ANSI Z21.88-2017/CSA 2.33-2017, Vented Gas Fireplace Heaters
CSA 2.17 2017, Gas-Fired Appliances for Use at High Altitudes
This installation must conform with local codes, or in the absence of
local codes, with the National Fuel Gas Code, ANSI Z223.1/NFPA 54, or
the Natural Gas and Propane Installation Code, CSA B149.1.
1.2 California Proposition 65 Warning
WARNING:
This product can expose you to chemicals including
Carbon Monoxide, that is an externally vented by-product of fuel
combustion, which is [are] known to the State of California to cause
birth defects or other reproductive harm. For more information, visit
www.P65Warnings.ca.gov.
1.3 Requirements for the
Commonwealth of Massachusetts
The following requirements reference various Massachusetts and
national codes not contained in this manual.
For all sidewall horizontally vented gas fueled equipment installed
in every dwelling, building or structure used in whole or in part for
residential purposes, including those owned or operated by the
Commonwealth and where the side wall exhaust vent termination
is less than (7) feet above finished grade in the area of the venting,
including but not limited to decks and porches, the following
requirements shall be satisfied:
1.3.1 Installation of Carbon Monoxide Detectors
At time of installation of side wall horizontally vented gas fueled
equipment, the installing plumber or gas-fitter shall observe that
a hard wired carbon monoxide detector with an alarm and battery
back-up is installed on the floor level where the gas equipment is
to be installed. In addition, the installing plumber or gas-fitter shall
observe that a battery operated or hard wired carbon monoxide
detector is installed on each additional level of the dwelling, building
or structure served by the side wall horizontal vented gas fueled
equipment. It shall be the responsibility of the property owner
to secure the services of qualified licensed professionals for the
installation of hard wired carbon monoxide detectors.
In the event that the side wall horizontally vented gas fueled
equipment is installed in a crawl space or attic, the hard wired carbon
monoxide detector with alarm and battery back-up may be installed
on the next adjacent floor level. In the event that the requirements
of this subdivision can not be met at the time of completion of
installation, the owner shall have a period of thirty (30) days to
comply with the above requirements; provided, however, that during
said thirty (30) day period, a battery operated carbon monoxide
detector with an alarm shall be installed.
1.3.2 Approved Carbon Monoxide Detectors
Each carbon monoxide detector as required in accordance with the
above provisions shall comply with NFPA 720 and be ANSI/UL 2034
listed and IAS certified.
1.3.3 Signage
A metal or plastic identification plate shall be permanently mounted
to the exterior of the building at a minimum of eight (8) feet
above grade directly in line with the exhaust vent terminal for the
horizontally vented gas fueled heating appliance or equipment. The
sign shall read, in print no less the one-half inch (½) in size, “GAS VENT
DIRECTLY BELOW. KEEP CLEAR OF ALL OBSTRUCTIONS”.
1.3.4 Inspection
The state or local gas inspector of the side wall horizontally vented
gas fueled equipment shall not approve the installation unless, upon
inspection, the inspector observes carbon monoxide detectors and
signage installed in accordance with the provisions of 248 CMR 5.08
(2) (a) 1 through 4.
1.3.5 Exemptions
The following equipment is exempt from 248 CMR 5.08 (2) (a) 1
through 4: The equipment listed in Chapter 10 entitled “Equipment
Not Required To Be Vented” in the most current edition of NFPA 54 as
adopted by the Board; and Product Approved side wall horizontally
vented gas fueled equipment installed in a room or structure separate
from the dwelling, building or structure used in whole or in part for
residential purposes.
1.3.6 Manufacturer Requirements
1.3.6.1 Gas Equipment Venting System Provided
When the manufacturer of Product Approved side wall horizontally
vented gas equipment provides a venting system design or venting
system components with the equipment, the instructions provided
by the manufacturer for installation of the equipment and the
venting system shall include:
•
Detailed instructions for the installation of the venting system
design or the venting system components; and
•
A complete parts list for the venting system design or
venting system.
1.3.7 Gas Equipment Venting
System NOT Provided
When the manufacturer of Product Approved side wall horizontally
vented gas equipment does not provide the parts for venting the
flue gases, but identifies “special venting systems”, the following
requirements shall be satisfied by the manufacturer:
•
The referenced “special venting systems” instructions shall
be included with the appliance or equipment installation
instructions and;
•
The “special venting systems” shall be Product Approved by the
Board, and the instructions for that system shall include a parts
list and detailed installation instructions.
A copy of all installation instructions for all Product Approved
side wall horizontally vented gas fueled equipment, all venting
instructions, all parts lists for venting instructions, and/or all venting
design instructions shall remain with the appliance or equipment at
the completion of the installation.
1.0 INTRODUCTION