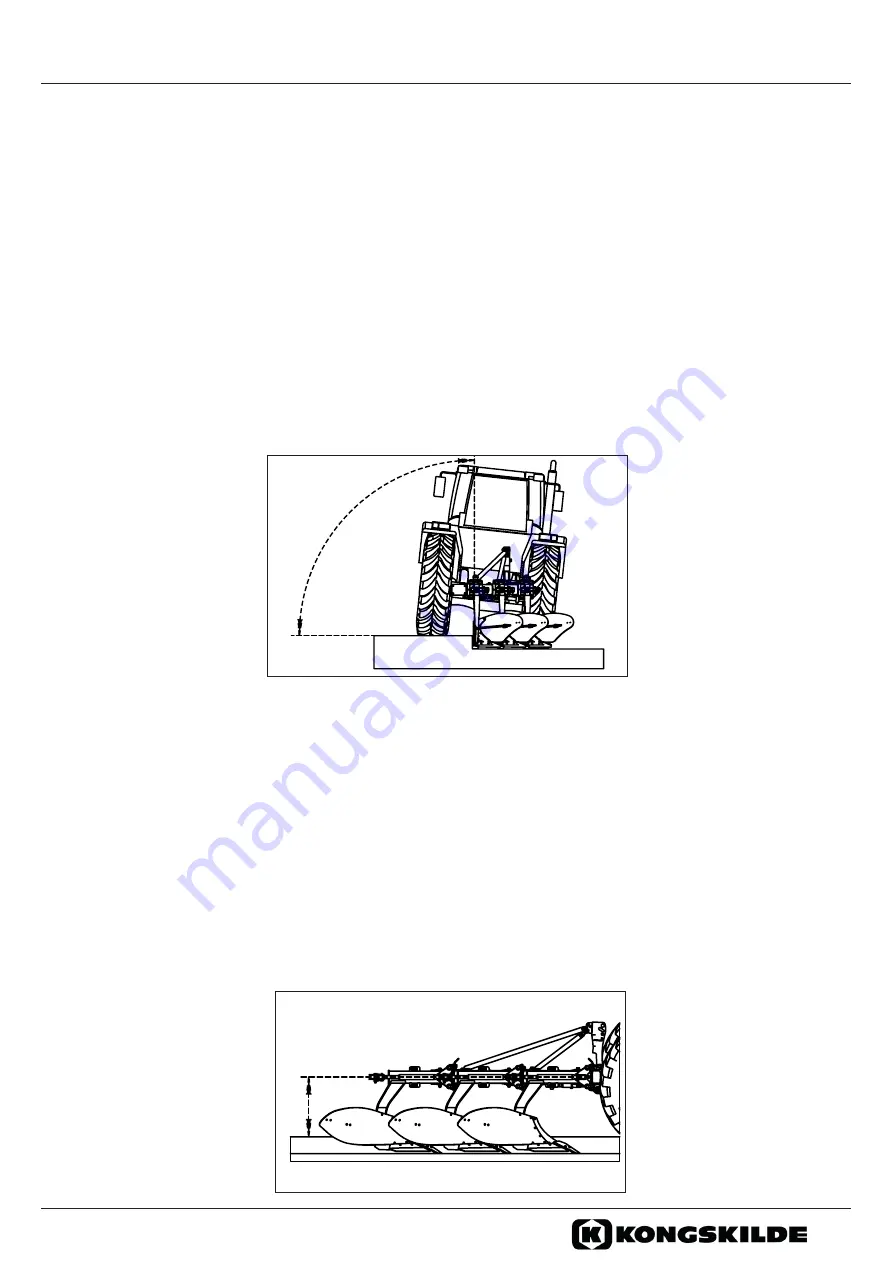
13
3. BASIC SETTINGS
3. BASIC SETTINGS
BASIC SETTINGS OF THE PLOUGH
The basic setting can be started when the desired ploughing depth has been reached and
when the tractor wheels are running in a furrow with the same depth.
1. VERTICAL ADJUSTMENT
The beams should be at right angle (90 °) to the ground. If necessary, make adjustments
by using the right-hand lower link of the tractor. The vertical setting can be checked by
observing the plough from the rear.
2. HORIZONTAL AND DEPTH ADJUSTMENTS
Mount the top link so that it is 5 - 10 cm lower on the tractor than on the plough when in
working position. The top link can be mounted in three positions on the plough. The slotted
centre hole can be used on tractors equipped with lower link sensing hydraulic system, and
it should be used with large ploughs. For ploughing in hard conditions using ploughs with
3-4 plough bodys, the top link should be attached in a fixed position to prevent the rear
plough body from working too shallow.
Adjust the length of the top link so that the depth of ploughing is the same for the first and
last bodies. The frame will now run parallel to the ground.
90°
ll