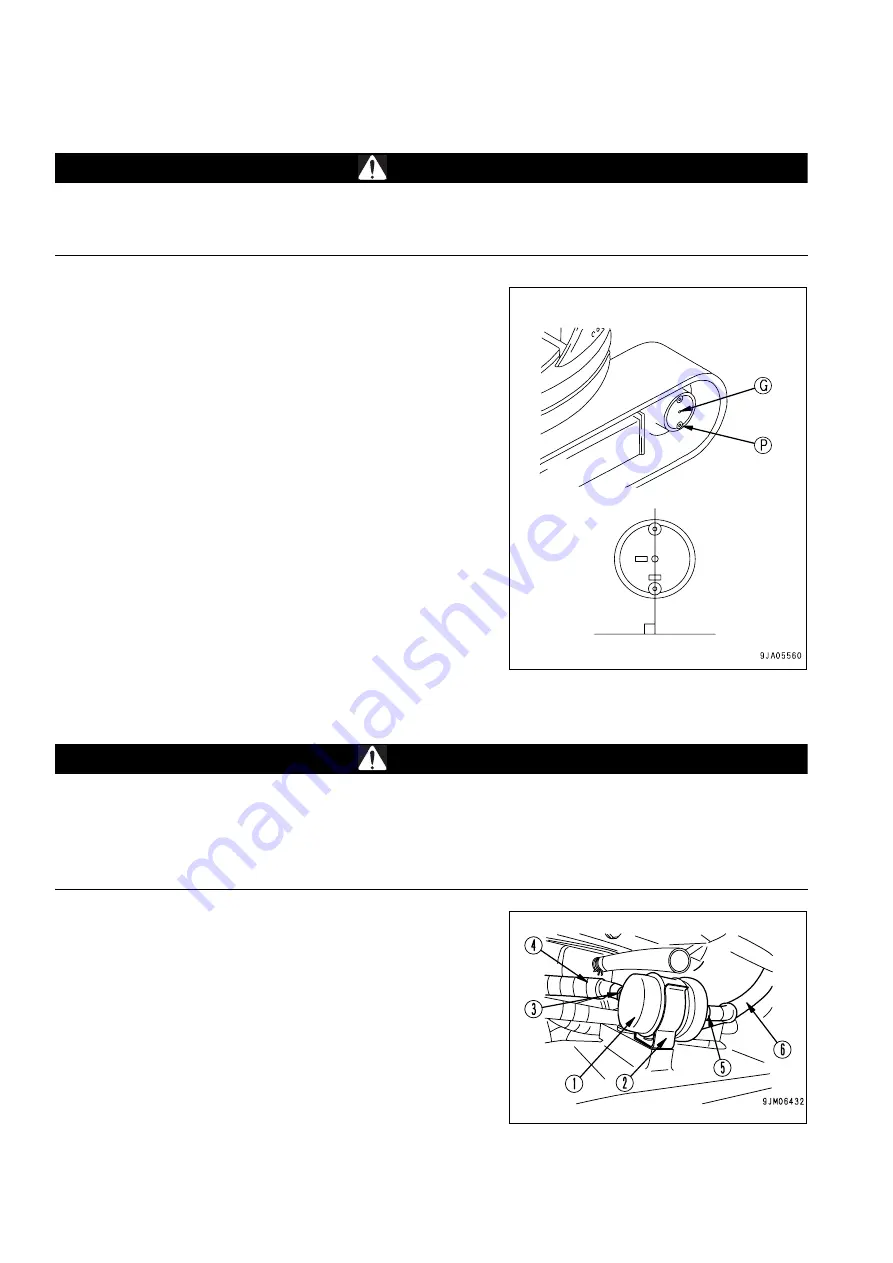
MAINTENANCE PROCEDURES
212
WEAM009500
4.9.5.d
CHECKING THE OIL LEVEL IN THE FINAL REDUCTION GEARS
WARNING
q
Soon after the machine has been stopped, the engine oil is very hot and may cause burns; let the oil
cool down to 40÷45° C before carrying out any check.
q
Loosen the cap slowly to release any residual pressure.
1.
The check must be carried out on each reduction gear, with
the drain plug (P) in low position and perpendicular to the
ground. If necessary, move the machine slightly until reach-
ing the specified position, which is indispensable for an accu-
rate check.
2.
This is a visual check and serves to make sure that the lubri-
cant reaches the height of the hole (G); if this is not the case,
top up by proceeding as explained in paragraph "4.9.6.b
CHANGING THE OIL IN THE FINAL REDUCTION GEARS"
and using the oil prescribed in the lubricant chart (see "4.4
FUEL, COOLANT AND LUBRICANTS").
4.9.5.e
CHANGING THE FUEL PUMP PREFILTER
WARNING
q
Change the prefilter after work, when the engine has cooled down to 40÷45°C.
q
During these operations some fuel may be spilled; clean the dirty areas immediately, in order to prevent
any risk of slipping or fire.
q
Oils, filters, the coolant and the battery are considered special waste and must be collected and dis-
posed of according to the regulations in force.
1. Prepare a container under the prefilter (1) to gather the fuel.
2. Remove the prefilter from the clamp (2).
3.
Remove the clamp (3) and disconnect the pipe (4) from the
prefilter.
4.
Remove the clamp (5), disconnect the pipe (6) from the used
prefilter and discard it.
5. Connect the pipes (4) and (6) to a new prefilter and fasten
them with the clamps (3) and (5).
6. Install the prefilter in the clamp (2) and bleed the fuel circuit
(see "4.9.5.c CHANGING THE FUEL FILTER ELEMENT
(WITH WATER SEPARATOR)").
Summary of Contents for PC26MR-3
Page 2: ......
Page 19: ...SAFETY AND ACCIDENT PREVENTION 17 ...
Page 62: ...60 THIS PAGE WAS INTENTIONALLY LEFT EMPTY ...
Page 63: ...THE MACHINE AND ITS OPERATIONS 61 ...
Page 170: ...168 THIS PAGE WAS INTENTIONALLY LEFT EMPTY ...
Page 171: ...MAINTENANCE 169 ...
Page 226: ...224 THIS PAGE WAS INTENTIONALLY LEFT EMPTY ...
Page 227: ...TECHNICAL SPECIFICATIONS 225 ...
Page 234: ...232 THIS PAGE WAS INTENTIONALLY LEFT EMPTY ...
Page 235: ...AUTHORISED EQUIPMENT 233 ...
Page 250: ...248 THIS PAGE WAS INTENTIONALLY LEFT EMPTY ...
Page 251: ......
Page 252: ... 2008 KOMATSU UTILITY EUROPE S p A All Rights Reserved Printed in Europe 01 2008 ...