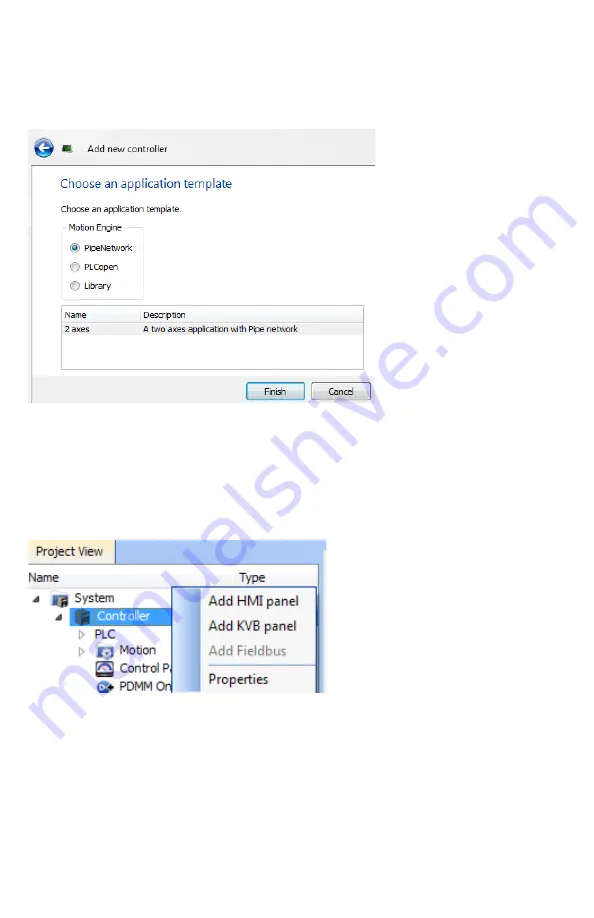
16
Select your AKD PDMM model from the list and click Next. You will then be prompted to select
an application template:
Figure 20. Select Application Template
Choose from PipeNetwork, PLCopen, or Library, and click Finish. The controller will then be
added to the project view.
To associate the project with the IP address of the PDMM controller, right click on the
Controller option in the Project View.
Figure 21. Controller Selection
AKD PDMM Quick Start | Install and Start the KAS IDE