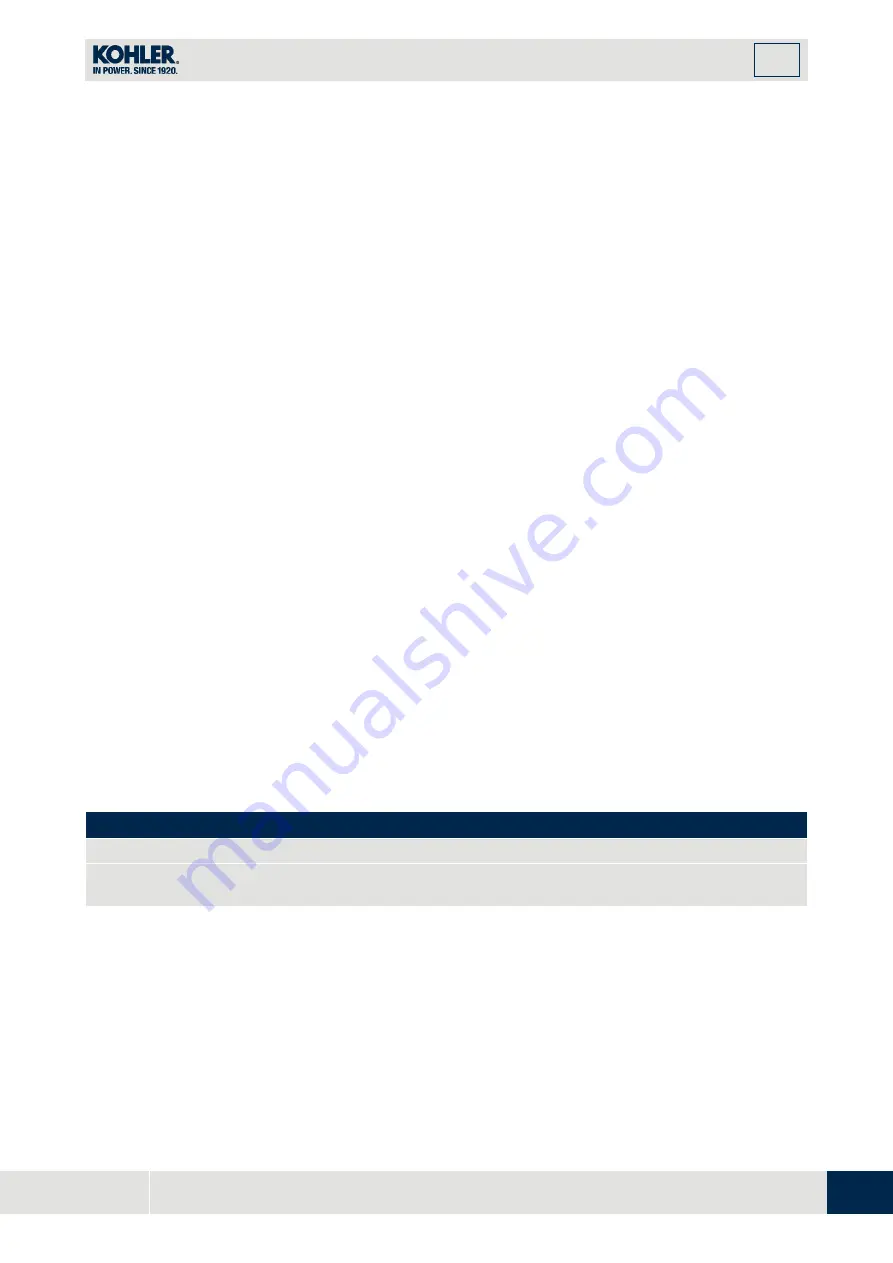
TECHNICAL
INFORMATION
2
15
EN
Insufficient lubricating capacity can lead to serious wear problems above all in common rail
injection systems. Too low a lubricating capacity is particularly a problem in fuels with a low sulfur
content (and in this respect sulfur contents ‹500 mg/kg can already be considered low). An
adequate lubricating capacity is guaranteed by the appropriate additives in low-sulfur (‹50 mg/kg) or
sulfur-free (‹10 mg/kg or ‹15 mg/kg) diesel fuels according to EN 590 and ASTM D 975. In low-
sulpur and sulfur-free diesel fuels which do not comply with this standard, the lubricating capacity
may have to be guaranteed by additives. The parameter for sufficient lubricating capacity is a
maximum wear spot of 460 micrometers in the HFRR test (EN ISO 12156-1).
KDI Electronic Injection Tier 3 – Stage IIIA emission equivalent certified Engines (EGR engines)
•
Those engines are designed for fuels in accordance with EN 590 and ASTM D975 for a cetane
number of at least 45. Since those engines are not equipped with exhaust gas after-treatment, they
can be operated with diesel fuels with sulfur content up to 500 mg/kg (ppm). Compliance with the
emission requirements is guaranteed only with sulfur content up to 350 mg/kg (ppm).
Fuels with a sulfur content > 50 mg/kg demand a shorter lubricating oil change interval. This is set
at 250hrs. However, the engine oil must be changed when the Total Base Number TBN is reduced
to 6.0 mgKOH/g test method ASTM D4739. Do not use low SAPS engine oils.
KDI Electronic Injection uncertified Engines (no EGR engines)
•
Those engines are designed for fuels in accordance with EN 590 and ASTM D975 for a cetane
number of at least 45. Since those engines are not equipped with exhaust gas after-treatment, they
can be operated with diesel fuels with sulfur content up to 2000 mg/kg (ppm). Fuels with a sulfur
content > 15 mg/kg demand a shorter lubricating oil change interval. This is set at 250hrs. However,
the engine oil must be changed when the Total Base Number TBN is reduced to 6.0 mgKOH/g test
method ASTM D4739.
2.5.1
Fuel for low temperatures
•
When operating the engine in ambient temperatures lower than 0 degrees C, use suitable low
temperature fuel normally available from fuel distributors and corresponding to the specifications of
Tab. 2.3
.
•
These fuels reduce the formation of paraffin in diesel at low temperatures.
•
When paraffin forms in the diesel, the fuel filter becomes blocked interrupting the flow of fuel.
2.5.2 Biodiesel fuel
•
Fuels containing 10% methyl ester or B10, are suitable for use in this engine provided that they
meet the specifications listed in the Tab. 2.3.
•
DO NOT USE
vegetable oil as a biofuel for this engine.
2.4
BIODIESEL COMPATIBILITY
Biodiesel according to EN 14214 (only permissible for mixture with diesel fuel at max. 10% (V/V))
US biodiesel according to ASTM D6751 – 09a (B100) (only permissible for mixtures with diesel fuel at
10% (V/V))
2.5.3 Synthetic fuels: GTL, CTL, BTL, HV
It is a well-known fact that engines which are operated for longer periods with conventional diesel fuel and
then converted to synthetic fuels suffer shrinkage of polymer seals in the injection system and thus fuel
leaks. The reason for this behavior is that the aromatic-free synthetic fuels can lead to a change in the
sealing behavior of polymer seals.
Therefore, conversion from diesel fuel to synthetic fuel may only be done after changing the critical seals.
The problem of shrinkage does not occur when an engine was operated with synthetic fuel from the start.