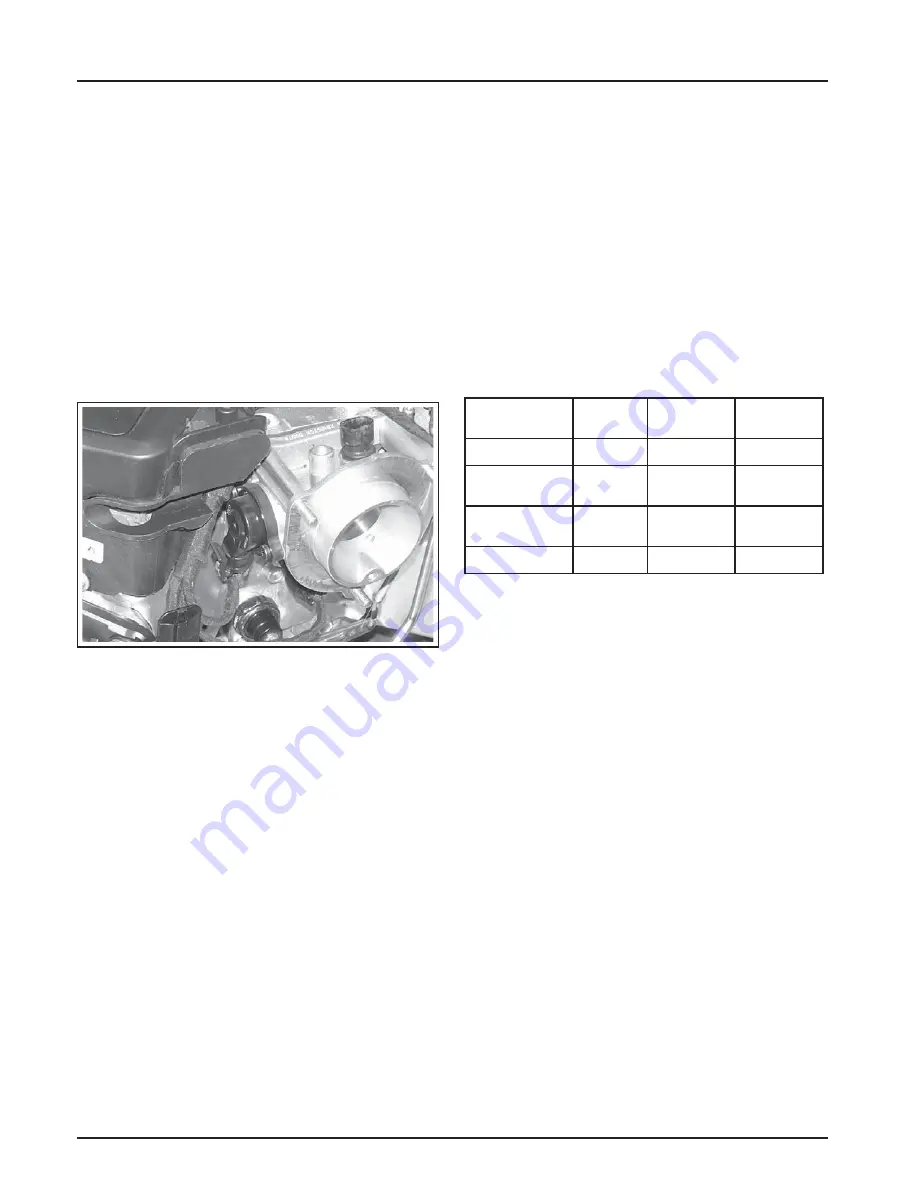
5.10
Section 5
EFI Fuel System
4. Leave the leads connected to the pin terminals as
described in step 3. Rotate the thro
tt
le sha
ft
slowly to the full thro
tt
le position. Monitor the
dial during rotation for indication of any
momentary short or open circuits. Note the
resistance at the full thro
tt
le position. It should be
4600-5200
without a stop pin, or
3200-4100
Ω
with a stop pin.
5. Disconnect the main wiring harness connector
from the TPS, leaving the TPS assembled to the
thro
tt
le body. Refer to the following chart and
perform the resistance checks indicated between
the terminals in the TPS switch, with the thro
tt
le
in the positions speci
fi
ed. Pin location shown in
Figure 5-4.
If the resistance values in steps 3, 4, and 5 are
within speci
fi
cations, go to step 6.
If the resistance values are not within
speci
fi
cations, or a momentary short or open
circuit was detected during rotation (step 4), the
TPS needs to be replaced, go to step 7.
6. Check the TPS circuits (input, ground) between
the TPS plug and the main harness connector for
continuity, damage, etc. The input pin is 12 and
the ground is pin 10.
a. Repair or replace as required.
b. Turn the idle speed screw back in to its
original se
tt
ing.
c. Reconnect connector plugs, start engine and
retest system operation.
7. Remove the two mounting screws from the TPS.
Save the screws for reuse. Remove and discard
the faulty TPS. Install the replacement TPS and
secure with the original mounting screws.
a. Reconnect the Black and TPS connector plugs.
b. Perform the TPS Learn Procedure integrating
the new sensor to the ECU.
Thro
tt
le
Position
Between
Terminal
Resistance
Value (
Ω
)
Continuity
Closed
A & C
1400-1800
Yes
Full with Stop
Pin
A & C
3200-4100
Yes
Full without
Stop Pin
A & C
4600-5200
Yes
Any
A & B
3000-7000
Yes
Mounted on the thro
tt
le body and operated directly
o
ff
the end of the thro
tt
le sha
ft
, the TPS works as a
potentiometer, varying the voltage signal to the ECU
in direct correlation to the angle of the thro
tt
le plate.
This signal, along with the other sensor signals, is
processed by the ECU and compared to the internal
preprogrammed maps to determine the required fuel
and ignition se
tt
ings for the amount of load.
The correct position of the TPS is established and
set at the factory. Do not loosen the TPS or alter the
mounting position unless absolutely required by fault
code diagnosis. If the
TPS is loosened or repositioned,
the appropriate TPS Learn Procedure
must
be
performed to re-establish the baseline relationship
between the ECU and the TPS.
Figure 5-5. TPS Location.
Service
The TPS is a sealed, non-serviceable assembly.
If diagnosis indicates a bad sensor, complete
replacement is necessary. If a blink code indicates a
problem with the TPS, it can be tested as follows:
1. Counting the number of turns, back out the idle
speed adjusting screw (counterclockwise) until
the thro
tt
le plates can be closed completely. Write
this number down for reference later.
2. Disconnect the Black connector from the ECU,
but leave the TPS mounted to the thro
tt
le body.
3. a. Use an ohmmeter and connect the red
(positive) ohmmeter lead to Black pin 12
terminal and the black (negative) ohmmeter
lead to Black pin 10 terminal to test.
b. Hold
the
thro
tt
le closed and check the
resistance. It should be
1400-1800
Ω
.
Summary of Contents for Command PRO CH749
Page 1: ...SERVICE MANUAL ECH630 ECH749 HORIZONTAL CRANKSHAFT ...
Page 2: ......
Page 4: ......
Page 76: ...6 6 Section 6 Lubrication System ...
Page 94: ...7 18 Section 7 Electrical System and Components ...
Page 112: ...8 18 Section 8 Disassembly ...
Page 126: ...9 14 Section 9 Inspection and Reconditioning ...
Page 153: ......