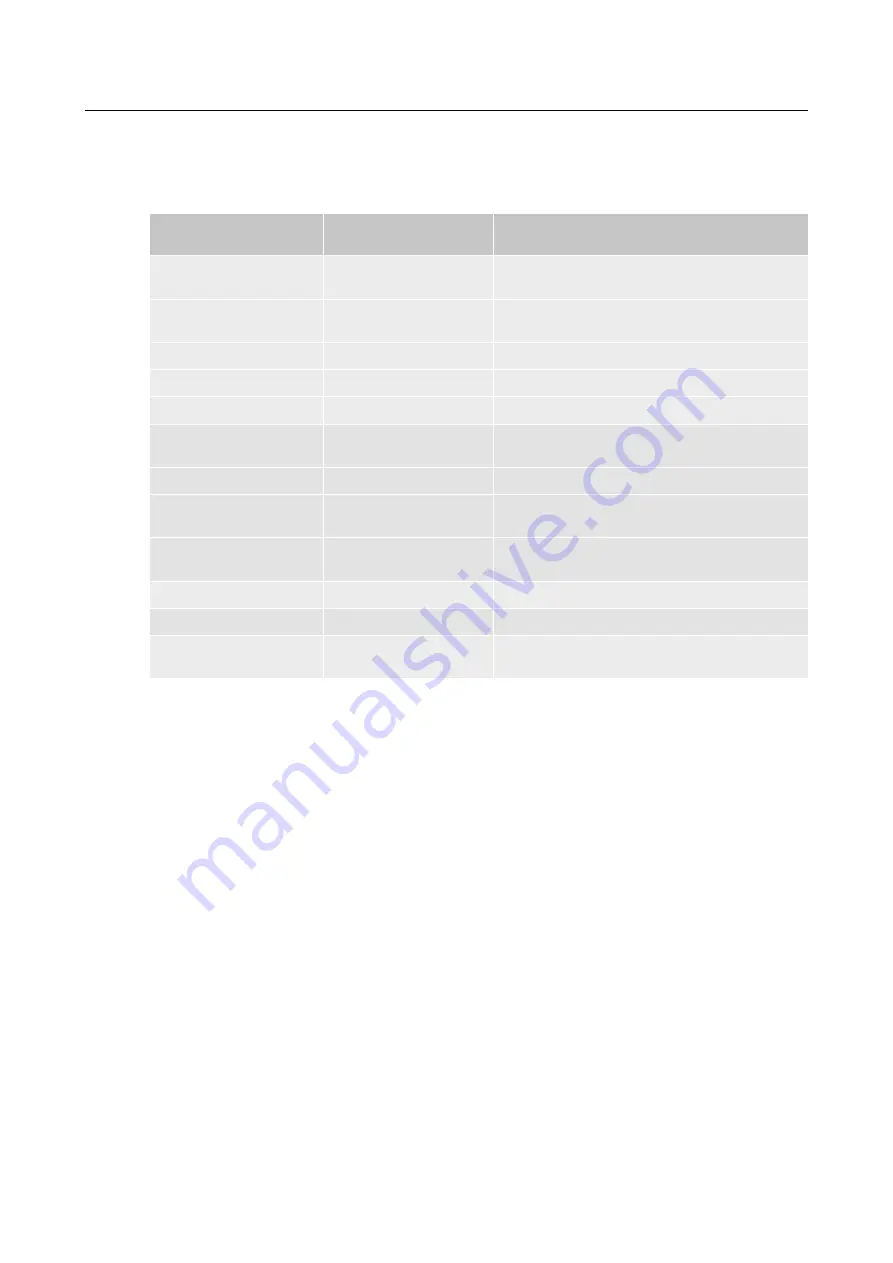
52
9. Care and maintenance
9.3 Maintenance plan (one-shift operation)
Cycle
Assembly
Maintenance task
Daily
Polishing pastes
Check paste length. Replace if below 80 mm or if
the corresponding message has appeared.
Polishing / deburring unit
Set ring distance. Replace if the diameter is less
than 165 mm.
Knife magazine
Dismantle and clean knife magazine.
Machine interior
Clean thoroughly using a brush or cloth.
Coolant unit
Drain water out, clean trough.
Weekly
Grinding belt drive
Open belt protection hood and clean the area of
the grinding belt.
Suction unit
Empty suction unit tray.
Check filter cartridge, remove and clean or replace
as needed.
Clean interior and exterior of machine. Attention!
The polishing / deburring rings cannot be wet.
Monthly
Gripper
Unscrew gripper and clean seal surface.
Semi-annually
Grinding belt drive
Remove and clean flow gauge.
Annually
Contact service department of KNECHT Maschinen-
bau GmbH.