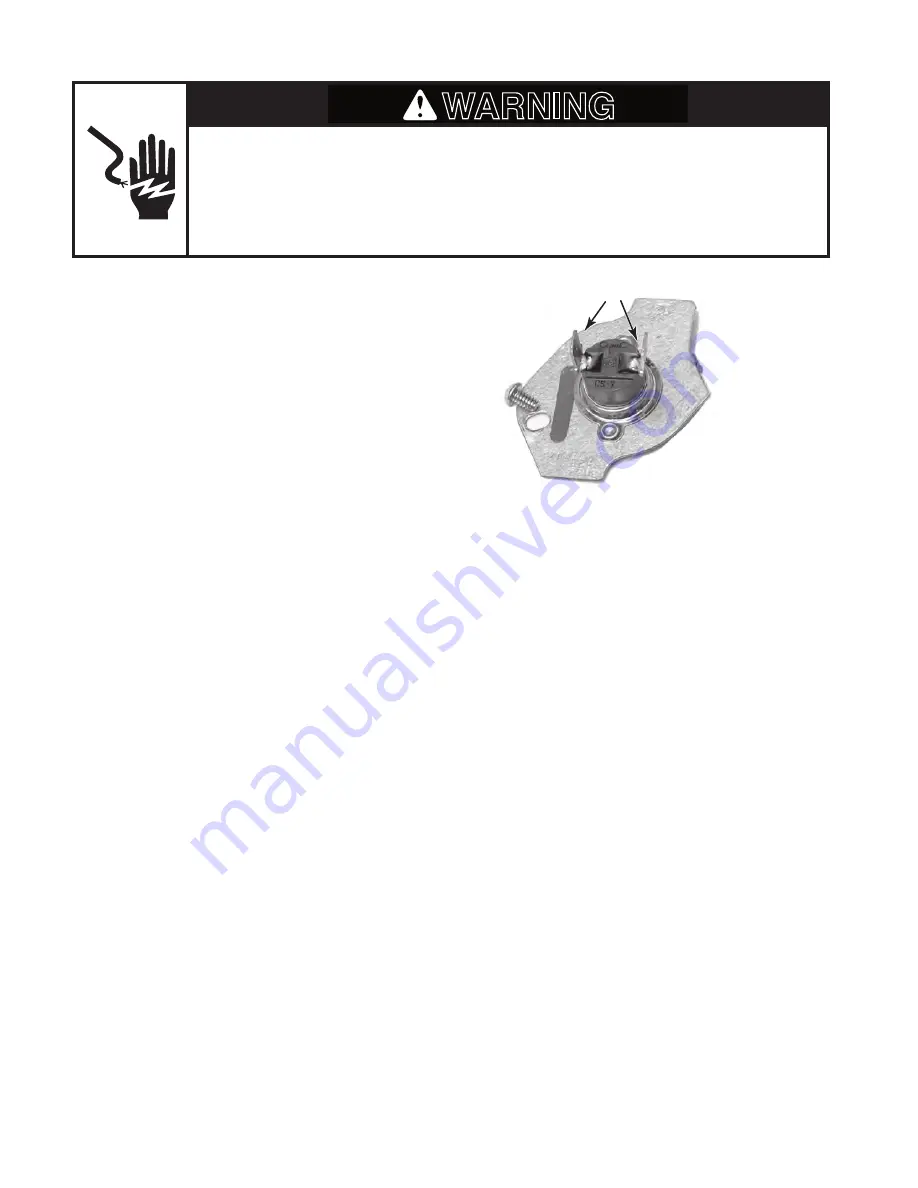
5-10
THERMAL CUTOFF (TCO)
(GAS DRYERS ONLY)
Refer to page 4-10 for the procedure for ac-
cessing the thermal cutoff (TCO).
1. Unplug dryer or disconnect power.
2. Turn off gas supply to dryer.
3. Disconnect the wire connectors from the
TCO terminals.
4. Set the ohmmeter to the R X 1 scale.
5. Touch the ohmmeter test leads to the TCO
terminals. The meter should indicate a
closed circuit (0
Ω
).
Electrical Shock Hazard
Disconnect power before servicing.
Replace all parts and panels before operating.
Failure to do so can result in death or electrical shock.
WARNING
Terminals
Thermal Cutoff (TCO)
Summary of Contents for KHEV01RSS - Pro Line Plus Electric Dryer
Page 112: ......