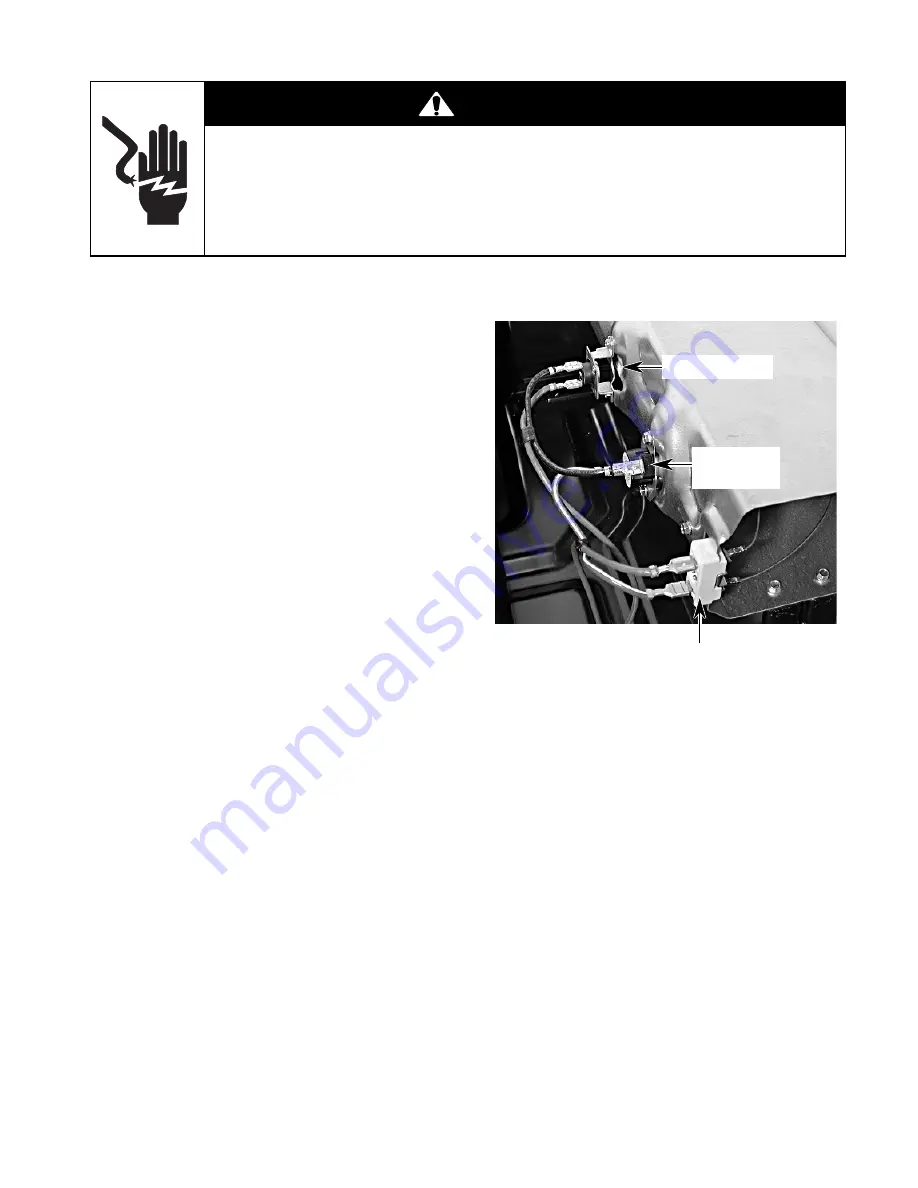
5-5
THERMAL CUTOFF
(ELECTRIC DRYERS ONLY)
Refer to page 4-10 for the procedure for ser-
vicing the thermal cutoff.
The thermal cutoff is a non-resettable device.
The cutoff temperature is 178
°
C (352
°
F).
If the dryer does not heat and there is 240 VAC
to the dryer, perform the following test.
1.Unplug dryer or disconnect power.
2.Disconnect the wires from the thermal cut-
off.
3.Set the ohmmeter to the R X 1 scale.
4.Touch the ohmmeter test leads to the ther-
mal cutoff terminals. The meter should in-
dicate continuity (0
Ω
). If the meter indi-
cates an open circuit (infinite), replace both
the thermal cutoff and the high-limit ther-
mostat. In addition, check for a failed
heater element, or a blocked, or improper
exhaust system.
Thermal Cutoff
High-Limit
Thermostat
Heater Terminals
WARNING
Electrical Shock Hazard
Disconnect power before servicing.
Replace all parts and panels before operating.
Failure to do so can result in death or electrical shock.
Summary of Contents for Ensemble KEHS01PMT/WH
Page 4: ... iv NOTES ...
Page 36: ...2 26 NOTES ...
Page 58: ...4 16 Squeeze Arms 8 Squeeze the locking arms and remove the socket from the drum light holder ...
Page 84: ...6 14 NOTES ...
Page 86: ...7 2 NOTES ...
Page 88: ......