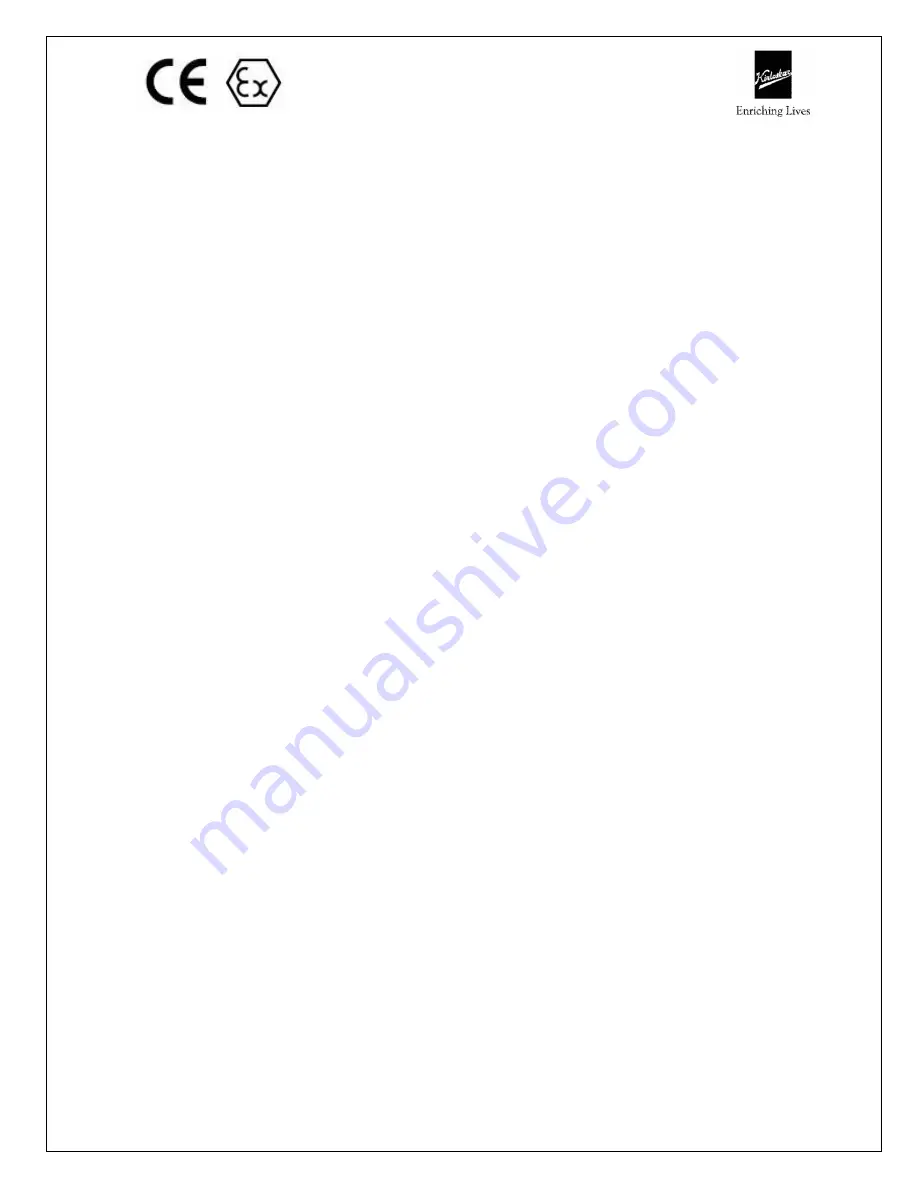
IOM/GK(P)/CONICAL ISSUE DATE: 10.11.2015
Page 23 LAST REV. DATE: 01.08.2019
in the container shall remain steady at a position. Visible level of the oil
in the container indicates that bearing housing is filled up to mark.
Caution
1)
In no case oil should be filled directly in to the bearing housing
reservoir, through breather cap.
2)
Replenish the visible reserve supply of oil in the container as oil is
used up.
3)
Please ensure that air ‘GROOVE’ provided on Aluminium body on
which plastic container rests is not clogged with dust / fibre, oil film,
etc. This groove allows atmospheric air to enter inside the body, to
maintain oil level in bearing housing.
4.
Operation:
4.1 EQUIPMENT DESCRIPTION:
End suction centrifugal pump type GK(P) is from KBL manufactured process
pump series which dimensionally conforms to DIN 24256 / ISO 2858 &
technically meeting requirements of ISO 5199.
The mechanical assembly comprises a rigid shaft, supported by a pair of
bearings with a double / single shrouded impeller mounted in a removable
bearing housing assembly. This is attached to an end suction volute casing
fitted with wear rings. The bearing housing, shaft and impeller assembly can
be withdrawn from the volute for maintenance without disconnection of pipe
work.
The discharge branch is positioned vertically upwards while suction branch
is horizontal and is at 90° to discharge nozzle. An additional mounting foot
is fitted at the outer bearing position for stability.
The complete assembly is of rigid construction, being intended for mounting
on suitable base plate with electric motor / internal combustion engine. A
suitable coupling is provided to transmit the rotational drive between pump
and motor. A spacer coupling is most suitable to use, because it allows the
removal of the pump rotating assembly without disconnecting suction pipe,
discharge pipe and motor.
Mechanical seal is used to seal the leakage of pumped liquid across the shaft
as a Standard scope of supply.
4.2 EQUIPMENT OPERATION:
4.2.1
Before starting the pump check the following:
1)
The pump rotates freely by hand. (Ensure seal locking plates are removed
before rotation).
2)
The level of the oil in the constant level oiler is up to the mark.
3)
The sealing liquid and cooling water connections are properly tightened
and adjusted.