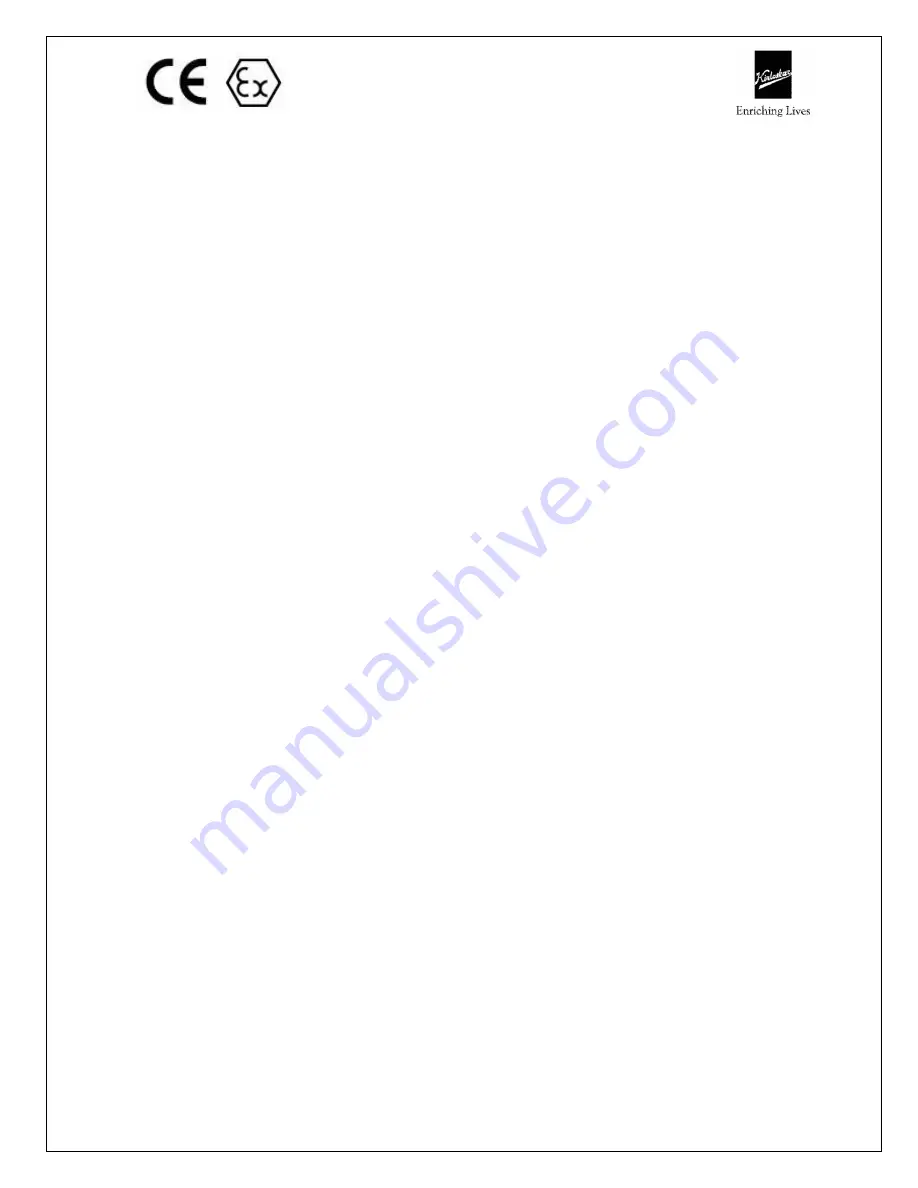
IOM/GK(P)/CONICAL ISSUE DATE: 10.11.2015
Page 8 LAST REV. DATE: 01.08.2019
Where there is any risk of the pump being run for prolonged periods against a
closed or partially closed valve generating high liquid and casing external surface
temperatures,
it is recommended that users fit an external surface temperature
protection device
.
A.5.2 Additional requirements for self-priming conditions
Where the system operation does not ensure control of priming, and the maximum
permitted surface temperature of the T3 Class could be exceeded, it is
recommended for users to fit an external surface temperature protection device.
A.6 Preventing the build up of explosive mixtures
ENSURE PUMP IS PROPERLY FILLED WHENEVER POSSIBLE AND DOES NOT RUN
DRY FOR LONGER THAN 5 MINUTES CONTINUOUSLY
Ensure the pump and relevant suction and discharge pipeline system is totally filled
with liquid during the pumping operation, so that an explosive atmosphere is
prevented. If the operation of the system cannot avoid this condition, ensure that
the pump does not run dry for more than 5 minutes continuously.
To avoid potential hazards from fugitive emissions of vapour or gas to atmosphere
the surrounding area must be well ventilated.
A.7 Preventing sparks
To avoid the potential hazard from random induced current generating a spark, the
earth stud on the pump casing or foot must be connected. Avoid electrostatic
charge: Do not rub non-metallic surfaces with a dry cloth for cleaning, etc; ensure
the cloth is damp.
A.8 Preventing leakage
The pump must only be used to handle liquids for which it has been approved to
have the correct corrosion resistance. Avoid entrapment of liquid in the pump and
associated piping due to closing of suction and discharge valves, which could cause
dangerous excessive pressures to occur if there is heat input to the liquid. This can
occur particularly if the pump is stationary. Bursting of liquid containing parts due
to freezing, must be avoided by draining or protecting the pump and ancillary
systems. If leakage of liquid to atmosphere can result in a hazard, the installation of
a liquid detection device is recommended.
A.9 Maintenance of the GK(P) pump to avoid the hazard
CORRECT MAINTENANCE IS REQUIRED TO AVOID POTENTIAL HAZARDS WHICH
GIVE A RISK OF EXPLOSION
The responsibility for compliance with maintenance instructions is with the plant
operator. To avoid potential explosive hazards during maintenance, the tools,
cleaning and painting materials used must not give rise to sparking or adversely
affect the ambient conditions. Where there is a risk from such tools or materials,
maintenance must be conducted in a safe area.
It is recommended that a maintenance plan and schedule is adopted, in line with
the user instructions provided, to include the following: