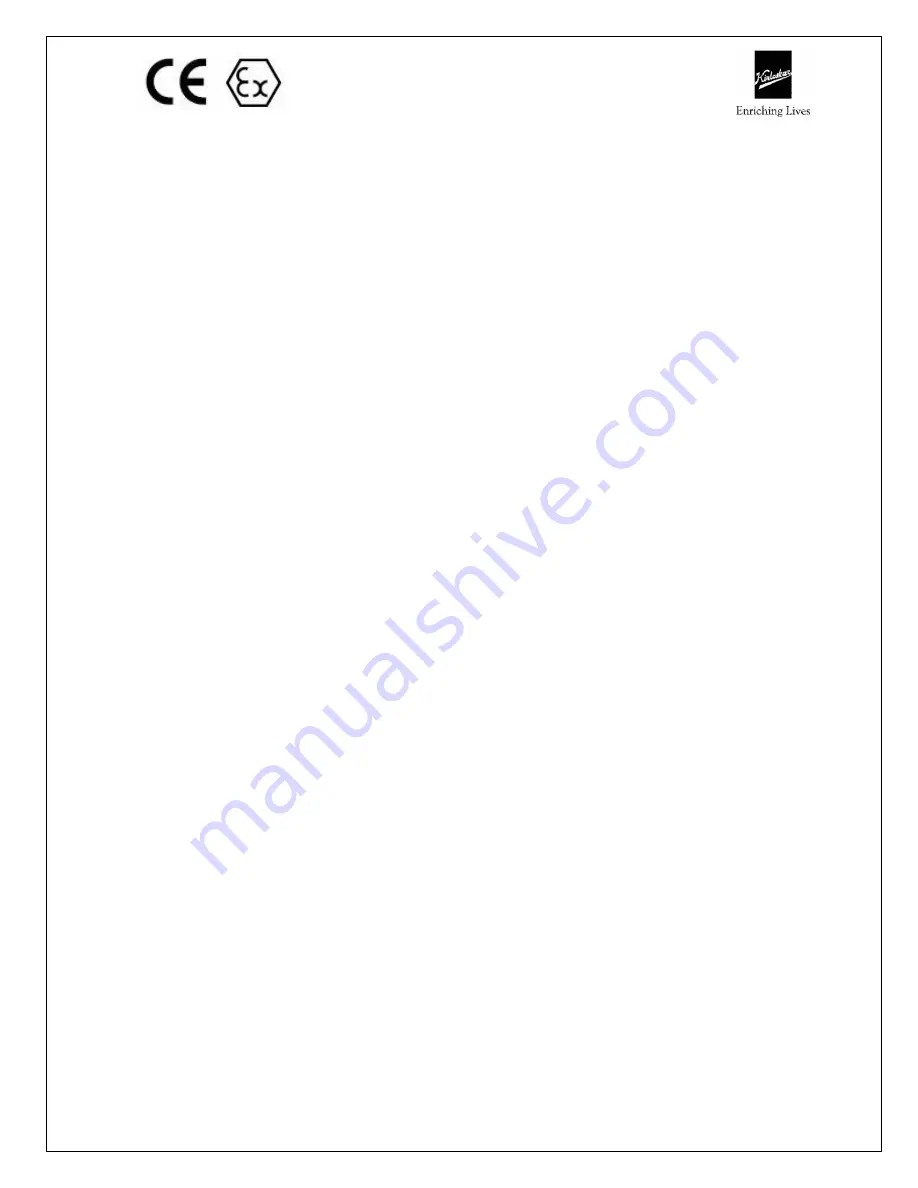
IOM/GK(P)/CONICAL ISSUE DATE: 10.11.2015
Page 24 LAST REV. DATE: 01.08.2019
4)
The direction of rotation of driver should correspond to the direction of
rotation of pump.
5)
The pump casing and the suction pipeline is fully primed with the liquid.
6)
Valve on delivery side is closed.
7)
The cock for pressure gauge connection is closed.
8)
For GK(P)J pumps before each start up of pump, circulate steam/hot
water to pump casing and/or casing cover jacket for a period of about ½
hour to ensure that all solidified liquid is melted.
4.2.2
Starting the pump
1)
In case of external liquid for sealing / quenching, start the liquid supply
before starting the pump.
2)
Start the pump. Let the prime mover pickup its full speed.
3)
Open the valve on delivery line gradually.
4)
Regulate the required flow by adjusting the delivery valve.
5)
Open the cock for pressure gauge connection.
4.2.3
During running the pump check the following things and regulate if needed -
1)
The pump is running smooth.
2)
The flow of sealing liquid in case of external sealing and cooling /
heating water is uninterrupted. If necessary, provide sight glass in the
piping.
3)
The bearings are not getting abnormally hot.
4)
There is no leakage through mechanical seal.
5)
Head and capacity developed by the pump is as specified.
6)
Power consumption is within limit.
7)
Ensure that there is no mechanical friction or noise in the pump.
8)
Stop the pump immediately, if any defects are detected. Do not start the
pump unless the defects are rectified. If it is not possible to rectify the
defects, then report immediately to the supplier or authorized dealer or
nearest KBL office.
4.2.4
During stopping the pump -
1)
Close the valve on the delivery line. Ensure that pump will not run for
more than few seconds in this condition.
2)
Stop the motor.
3)
Close the cooling water and sealing liquid connections.
4)
If the pump is not required to be operated for a long time, drain the pump
casing completely. If the pump is required to be stored for a long time,
the bearing housing should be dried internally with hot air and should be
flushed with moisture free protective such as light oil or kerosene.
5)
If any cooling and flushing arrangements are provided, then it must be
drained and dried.
Failing to follow right shop practices during equipment operation will result into
failure of product & in turn product warranty gets void.