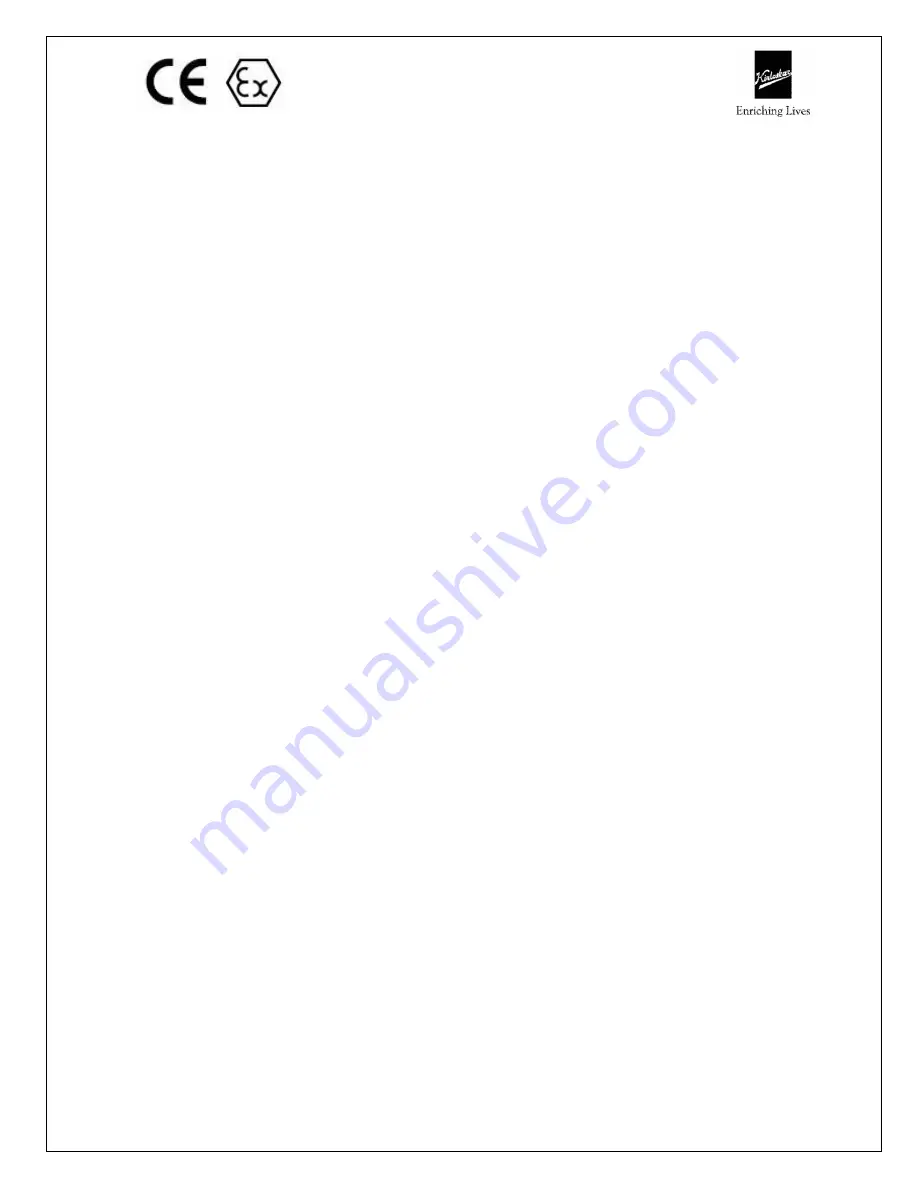
IOM/GK(P)/CONICAL ISSUE DATE: 10.11.2015
Page 64 LAST REV. DATE: 01.08.2019
PIPING
Both suction and delivery pipes and accessories should be independently supported
near the pump, so that when the flanges, bolts are tightened no strains will be
transmitted to the pump casing. It is usually advisable to increase the size of both
the suction and delivery pipe at the pump nozzles in order to decrease the loss of
head due to friction and for the same reason piping should be arranged with
minimum possible bends as possible, or it should be made with long radius
wherever possible. The pipe lines should be free from scales, welding residuals etc.,
and have to be mounted in such a way that they can be connected to suction and
delivery flanges without any stress on the pump. It can be achieved by supporting
the pipelines at appropriate locations.
SUCTION PIPE
The suction pipe should be as short as possible. This can be achieved by placing
the pump near the liquid to be pumped. The suction pipe must be kept free from air
leakages. This is particularly important when the suction lift is high. A horizontal
suction line must have a gradual rise to the pump. Any high point in the pipe will be
filled with air and thus prevent proper operation of the pocket in the top of the
reducer and the pipe. Use an eccentric piece instead.
The end of the suction pipe must be well submerged to avoid whirlpools and
ingress of air but must be kept clear of any deposits of mud, silt, grit, etc. The pipe
must be away from any side of the wall by 450 mm. The end of the strainer must
be provided with a strainer of sufficient open area.
DELIVERY PIPE
A check (non-return) valve and a gate or sluice valve (regulating valve) should be
installed in the discharge line. The check valve placed between the pump and the
gate valve is to protect the pump from excessive pressure and to prevent water
running back through the pump in case of failure of the driving machine.
Discharge piping should be provided with a sluice valve adjacent to the delivery
flange to control the discharge if required.
VACUUM EQUALIZING LINE (AND LIQUID LINE)
If the pump draws from a system under vacuum an equalizing pipe must be carried
from the highest point of the suction line, however as close to the suction flange of
the pump as possible, to the top of the feed tank to keep gas bubbles that might
have been entrapped in the flow from entering the pump. The line should be fitted
with an isolating valve which should be closed only for maintenance work on the
pump set.
Apply sealing liquid (external sealing) to the shaft seal cage to prevent entry of air
in the case of pumps with packed stuffing box. It is convenient to tap the sealing
liquid from the delivery line above the non-return valve.
FOOT-VALVE
It is advisable to install a foot-valve to facilitate priming. The foot-valve should have
sufficient clear passage for water. Care must be taken to prevent foreign matter