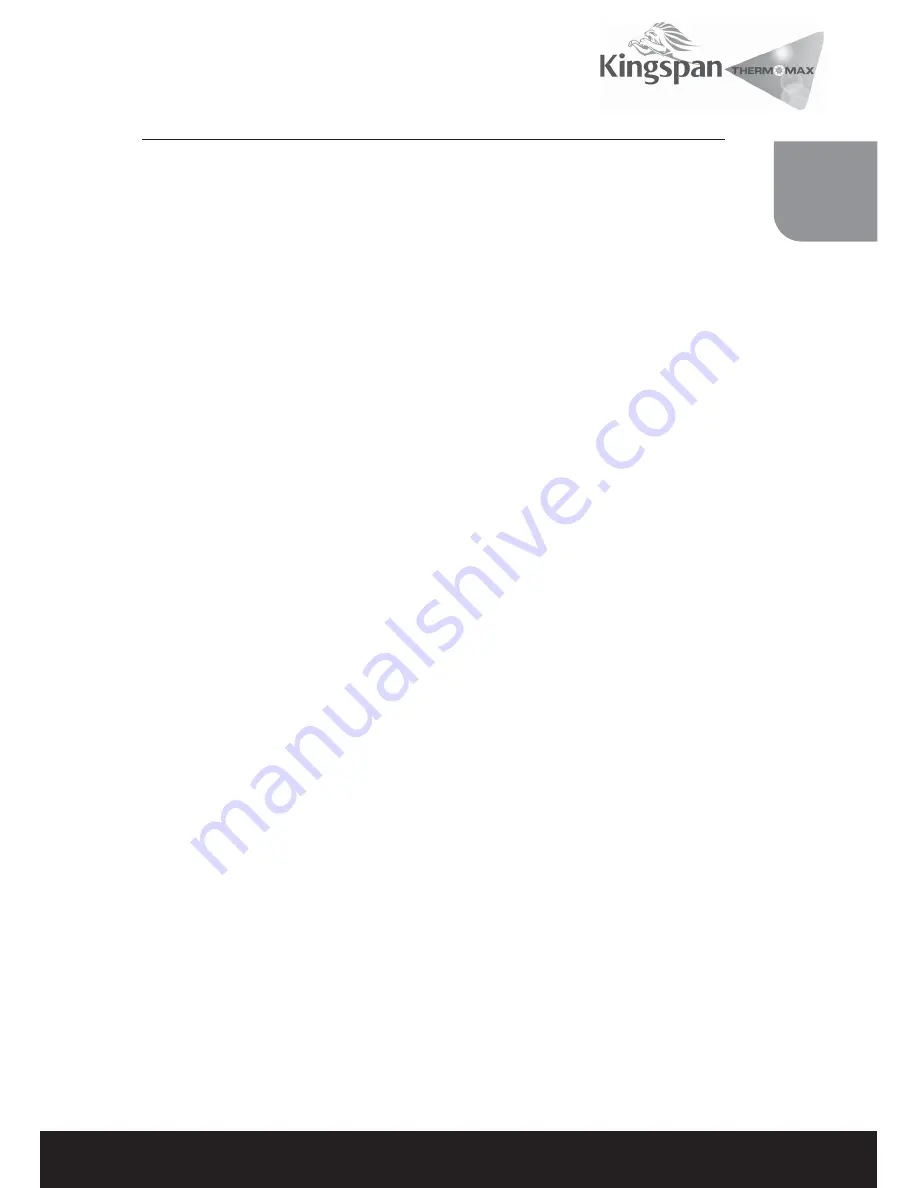
31
Kingspan Environmental Warranty Statement for Solar Goods
(in brief)
Subject to the following provisions, Kingspan Environmental warrants that the Goods will be free from defects in material
and workmanship for a period of 5 or 20 years in relation to VACUUM TUBES and a period of 5 years for VARISOL
FLOW CONDUITS & COVERS, MANIFOLDS and KITS from their date of manufacture. The warranty is given by Kingspan
Environmental subject to the following conditions:
A. A 5 year warranty period on Vacuum Tubes when such tubes are installed by a Certified Solar Installer. If the Vacuum
Tubes are installed by a Kingspan Environmental Accredited Installer and subject to the collector(s) being properly
designed, installed and maintained according to the manufacturer’s recommendations, then such products will carry a
20 year warranty period. All the systems must be designed in accordance with the Kingspan Design Guide, and installed
and maintained in accordance with the Thermomax Installation Manual.
B. Kingspan Environmental shall be under no liability in respect of any defect in the Goods arising from any information
drawing design or specification supplied by the Buyer
C. Kingspan Environmental shall be under no liability in respect of any defect arising from fair wear and tear, willful
or accidental damage, negligence, abnormal working conditions, failure to follow the Kingspan Environmental'
instructions, misuse or alteration or repair of the Goods without approval
D. The above warranty does not extend to parts materials equipment not manufactured by Kingspan Environmental in
respect of which the Buyer shall only be entitled to the benefit of any such warranty or guarantee as is given by the
manufacturer to the Company.
E. The defect has been reported by the Buyer to Kingspan Environmental within the warranty period.
F. The installation of the Goods having been carried out by fully trained and competent person(s).
G. The Goods having been subjected to neither “prolonged stagnation conditions” nor exhibiting signs of “extreme
temperature exposure”
1.
The Buyer shall not make any statement or representation or give any warranty to any third party in respect of any
Goods other than in the terms made or given by Kingspan Environmental to the Buyer nor shall the Buyer have any
authority to commit Kingspan Environmental to provide any service in relation to the Goods.
2. The Company's liability to the Buyer for death or injury resulting from its own or that of its employees' agents' or
subcontractors' negligence and damage suffered by the Buyer as a result of any breach of the obligations implied by
Section 12 of The Sale of Goods Act 1979 shall not be limited.
3. If Kingspan Environmental fails to deliver the Goods for any reason other than any cause beyond the Company's
reasonable control or the Buyer's fault then Kingspan Environmental shall only be liable to the Buyer for and the
Company's liability shall be limited to the excess (if any) of the cost to the Buyer (in the cheapest available market) of
similar goods to replace those not delivered over the Price of the Goods.
4. The Buyer shall examine all delivered Goods forthwith. Any claim based on any defect in the quality or condition of
the Goods or their failure to correspond with specification shall be notified to Kingspan Environmental within 7 days
from the delivery date or where the defect was not apparent on reasonable inspection within a reasonable time after
discovery of the failure. If delivery is not refused and the Buyer does not notify Kingspan Environmental the Buyer shall
not be entitled to reject the Goods.
5. Kingspan Environmental shall be entitled to examine any Goods, which are the subject of any claim by the Buyer, and
to remove such Goods or any part thereof for testing. No tests carried out by the Buyer will be recognised by Kingspan
Environmental unless carried out strictly in accordance with a method previously agreed by Kingspan Environmental as
being suitable for the purpose.
6. Any valid claim in respect of the Goods which is based on any defect in the quality or condition of the Goods or
their failure to meet specification is notified to Kingspan Environmental in accordance with these Conditions
Kingspan Environmental shall be entitled to repair or replace the Goods (or the part in question) free of charge or
at the Company's sole discretion refund to the Buyer the Price (or a proportionate part of the Price) but Kingspan
Environmental shall have no further liability to the Buyer.
7. Kingspan Environmental shall not be liable to the Buyer by reason of any representation (unless fraudulent) or any
implied warranty condition or other term or any duty at common law (including but without limitation the negligence of
Kingspan Environmental its employees agents or otherwise) or under the express terms of the Contract for any loss of
production loss of profits or anticipated profits loss of contracts operation time or anticipated savings loss of business
or of expected further business loss of or corruption to data damage to the Buyer’s reputation or goodwill damages
costs or expenses payable by the Buyer to any third party or any other indirect special or consequential loss or damage
or claim (whether caused by the negligence of Kingspan Environmental its employees agents or otherwise) which arise
out of or in connection with the supply of the Goods or their use or resale by the Buyer.
8. Without prejudice to the provisions of clauses 3, 4, 5, 6 and 7 the entire liability of the Buyer under or in connection with
the Contract shall not exceed the Price of the Goods.
9. Kingspan Environmental shall not be liable to the Buyer or be deemed to be in breach of the contract by reason of any
delay in performing or any failure to perform any of the Company's obligations in relation to the Goods if the delay or
failure was due to any cause beyond the Company's reasonable control. Without limiting the foregoing, due to causes
beyond the Company's reasonable control.
10. For comprehensive details regarding “Warranties and Liability” please refer to the “CONDITIONS OF SALES” section 7.
Warranty Statement