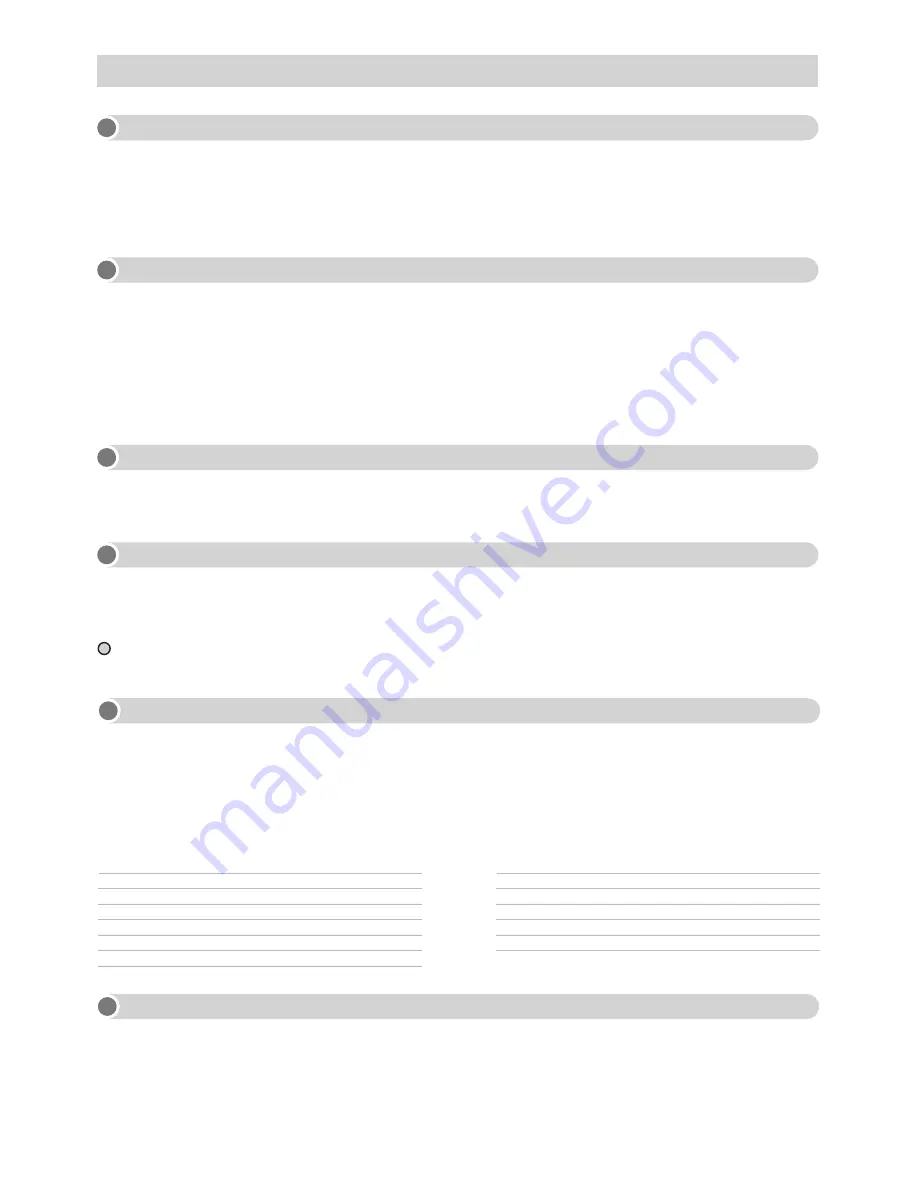
To assemble
“belt unit”, proceed as follows:
- Slide one end of the belt into the transfer pulley (
A
) and the other end into the motor support (
B
) following the orientation shown
in
figures 1
and
2
- Then join the two ends with the plastic joint (
C
). Fix to the top drive carriage (
D
) as in
fig.03
.
- Extend the belt and check that the unit is in line, with the teeth facing inwards (
fig.04
).
ASSEMBLING THE “BELT UNIT”
ASSEMBLING THE GUIDE “GRB3” (3mt)
ASSEMBLING THE GUIDE “GRB23” (1.5mt X 2) OR “GRB4” (3mt + 1)
FIXING THE GEAR MOTOR TO THE GUIDE
- Mate the motor casing (
L
) to the support (
B
)
(
fig.09
).
- Definitively fix the gear motor to the guide using the four 6.3 mm x 50 self-threading screws
(
M
)
and the two M6 x 50 metric
screws
(
N
)
as in
figures 9
and
10
.
Please take care to insert the self-threading screws “M” and the metric screws “N” in the appropriate holes as
shown in figure 10.
Guide "
GRB3
" is supplied already assembled, the only operation still required is to tension the belt until the distances between
the pulley support (
A
) and bracket (
I
) is 18 -20 mm (
fig.08
).
To assemble the guide “
GRB23
” or the guide “
GRB4
”, proceed as follows:
- Extend the belt and check that the unit is in line, with the teeth facing inwards (
fig.04
).
- Insert the “belt unit” into the guide without the brackets from the screw (
E
) end until the motor support is restrained (
fig.05
).
- Prepare the two profiles (
F
) and the joint (
G
) supplied (
fig.06
).
- Join the two guides and the joint firmly together with the fastenings supplied (
H
) (
fig. 06
).
- Insert the screw M8x70 (
E
) into the bracket (
I
). Insert, in order, the washer, the spring, the washer and the self-locking M8 nut
(
fig.07
).
- Tension the belt until the distances between the pulley support (
A
) and bracket (
I
) is 18 - 20 mm (
fig.08
).
!
Considering the installation limits pointed out on the previous page, fix it above the door, centrally to the door and with the
bracket “
O”
perfectly level (
fig.11
).
Where the installation site allows, the possibility exists to fix the guide directly onto the ceiling, turning the bracket (
O
)
90°
(
fig.12
).
To facilitate and optimise the installation, some "guideline" dimensions are given that allow the profile to be fixed perfectly level
(
fig.13 - fig.14
).
0mm
Ceiling height (H)
(fig.13)
40mm
Ceiling height (H)
(fig.13)
80mm
120mm
160mm
01
02
03
04
05
200mm
06
Bracket hole
(fig.14)
240mm
280mm
320mm
360mm
400mm
07
08
09
10
11
Bracket hole
(fig.14)
WALL MOUNTING THE GUIDE
Set the automation to manual operation (
fig.20
), and then drag the carriage to the door.
Fix the bracket (
Q
) to the door making
sure the two surfaces mate perfectly (
fig.17
).
Please verify it is firmly fastened, opening and closing the door manually.
!
!
With the automation set on manual operation, fully close the door, loosen the catch screw (
R
)
and join the catch itself to the drive
carriage. Then tighten the screw (
R
) firmly (
fig.18
).
Repeat the operation with the door fully open (
fig.19
).
The release manoeuvre has been provided for manual opening of the door in case of a power cut or motor breakdown.
In order to enable all types of use (for example the presence of an electric or outside lock) the handle has been designed to lock
itself perpendicularly to the carriage, allowing the user to completely do away with door automation.
The gear motor can also be released from the outside installing the optional accessory “
SBLO01
".
The two manual operating modes are:
MODE 01:
If you would like to release the
automation and keep it released
even after closing the gate.
OPERATION:
The user that exits from the garage
can close the gate and re-enter
without having to repeat the release
operation. The automation release
must be guaranteed by an external
blocking system (a lock, for
example)
INSTRUCTIONS:
- Pull the release cord downwards
as illustrated in
figure 20
until the
handle perpendicular to the guide
is blocked, unhooking the lower
driving carriage.
- Move the gate manually
MODE 02:
If you would like to release the
automation and then re-activate it
during the manual closing, thus
blocking the gate.
OPERATION:
The user that exits the garage,
making use of the reconnection of
the automation during the manual
closing operation, obtains the
recoupling of the carriages and thus
the blocking of the gate
INSTRUCTIONS:
- Pull the release cord downwards
as illustrated in
figure 20
until the
handle perpendicular to the guide
is blocked
- Move the door manually
- Return the handle to the original
position (
fig. 21 - 21b
)
During manual operation use only the door for opening and closing, thus avoiding strain on the carriage by pulling
the release cord.
ADJUSTING THE END OF STROKE
FIXING THE DOOR TO THE BRACKET
MANUAL MANOEUVRE
Unscrew the M6 nut (
P
) and anchor the fastening brackets to the ceiling above the guide verifying they are perpendicular to the
profile (
fig.15
). For the choice of the holes, see the previous paragraph (
fig.13-14
).
Cut the brackets in the part extending under the profile.
Lift away the guide, mark the bracket anchoring points on the ceiling, put the guide back and drill the ceiling (
fig.16
).
Definitively fix the guide and verify it is level.
CEILING MOUNTING THE GUIDE
20
21
21b
INSTALLATION