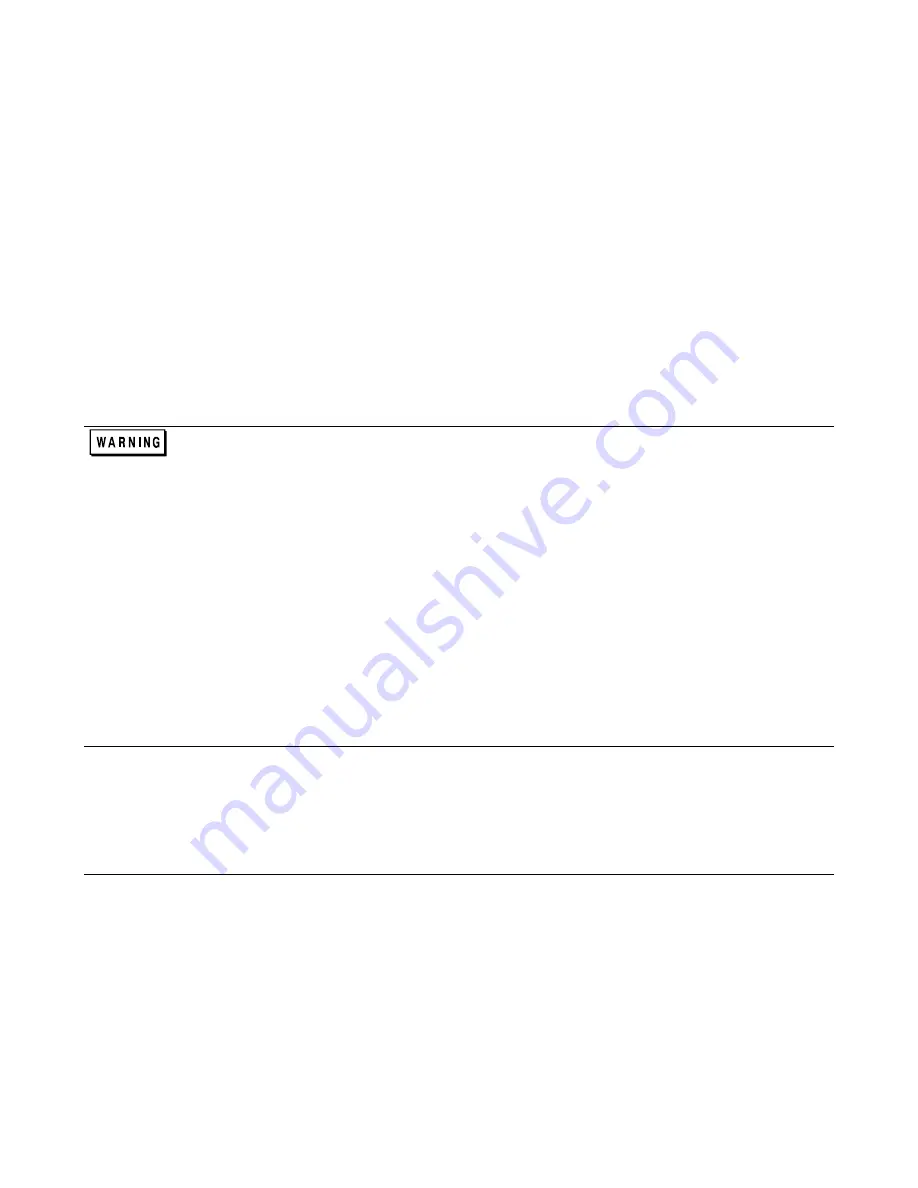
Troubleshooting 49
Tools Required
TORX screwdriver size T-15 (for most all retaining screws).
TORX screwdriver size T-20 (for power supply carry straps).
Seven (7) mm metric hex driver (to remove GPIB read connector).
Pencil, paper, and labels to make notes to aid in the reinstallation of components.
Work at a static-free station such as a table covered with static-dissipative laminate or with a conductive table mat
(Keysight P/N 9300-0797, or equivalent) using a conductive wrist strap where necessary, such as, Keysight P/N
9300-0969 or 9300-0970.
Top Cover
1.
Remove the four screws that secure the carrying straps (two TORX 20 screws on each side). These same screws secure
the cover to the chassis.
2.
Spread the bottom rear of the cover, and then pull the cover backwards towards the rear of the power supply to
disengage it from the front panel.
Shock Hazard:
Hazardous voltage can exist inside the power supply even after it has been turned off.
Check the INPUT RAIL LED (A4CR402) under the RFI shield (see Figure 3-18 end of this section for
LED location). If the LED is on, there is still hazardous voltage inside the supply. Wait until the LED goes
off (
approximately 7 minutes after power is removed
) before proceeding.
Removing Protective RFI Shield (Galvanized Sheet Metal)
Once you remove the top cover of the power supply, you will see the RFI galvanized sheet metal cover preventing the
power supply from emanating RFI fields. The RFI shield covers most components and circuit boards, as well as, many of
the chassis-mounted components. You must remove this shield in order to gain access to the inside of the power supply.
Remove the shield as follows:
1.
There are approximately 21 screws holding the cover to the frame.
2.
There are two screws at the top of the shield that secure a retaining clip for the GPIB board. You do not need to remove
these screws, simply loosen the screws and slide the GPIB retaining clip backwards free of the GPIB board.
3.
Remove all shield securing screws using a TORX T-15 screwdriver and save for later reinstallation .
4.
Lift the RF shield out of the chassis.
5.
When DC RAIL LEDs are extinguished, it is safe to work inside the power supply. (See Warning note above.)
Note
The following procedures describe the removal of most of the circuit boards within the power supply.
Once the GPIB board is removed, you will have access to the A4 AC Input Assembly and the A5 DC Rail
Assembly. Similarly, once the A10 control board is removed along with the Rectifier HS you will have
access to other components and boards within the supply.
It is recommended that when you disconnect any wires and/or cable connectors you should immediately
label them to simplify their reinstallation later.
GPIB Board
To remove the GPIB board, disconnect the cables from the following connectors at the GPIB board:
1.
Disconnect the cable going to connector P101.
2.
Disconnect phone cable going to J107.
3.
Disconnect phone cable going to J107.
4.
Disconnect phone cable going to J108.
5.
Remove two (2) holding screws at read of chassis holding GPIB board in place.
6.
Using a 7 mm driver, remove the two (2) screws holding the GPIB connector at rear of chassis.
7.
The GPIB board can now be lifted out from the chassis.
Summary of Contents for 669 A Series
Page 2: ...Service Manual Keysight Series 669xA GPIB DC Power Supplies ...
Page 3: ......
Page 27: ......
Page 56: ...Troubleshooting 53 Figure 3 15 3 Inch Front Panel Frame Assembly ...
Page 57: ...54 Troubleshooting Figure 3 16 Assembly A10 Exploded View ...
Page 58: ...Troubleshooting 55 Figure 3 17 Assembly A10 Exploded View 6690A ...
Page 59: ...56 Troubleshooting Figure 3 18 Assembly A10 Exploded View 6691A 6692A ...
Page 60: ...Troubleshooting 57 Figure 3 19 Three Phase Line Choke Subchassis Wiring ...
Page 61: ...58 Troubleshooting Figure 3 20 24 Volt Fan Transformer ...
Page 77: ...74 Diagrams Figure 6 1 Test Point Waveforms for Table 6 3 sheet 2 of 2 ...
Page 79: ...Figure 6 3 A1 Front Panel Board Assembly Diagram ...
Page 81: ...Figure 6 5 A2 GPIB Board Component Location ...
Page 83: ...Figure 6 7 A3 FET Board Component and Test Point Location ...
Page 87: ...Figure 6 11 A4 AC Input Board Component and Test Point Location 12 9 10 11 ...
Page 89: ...Figure 6 13 A5 DC Rail Board Component and Test Point Location 13 14 ...
Page 91: ...Figure 6 15 A6 Bias Board Component and Test Point Location 15 16 17 18 19 19 20 22 ...
Page 94: ...Figure 6 17 Power Mesh Schematic Diagram All Models ...
Page 103: ......