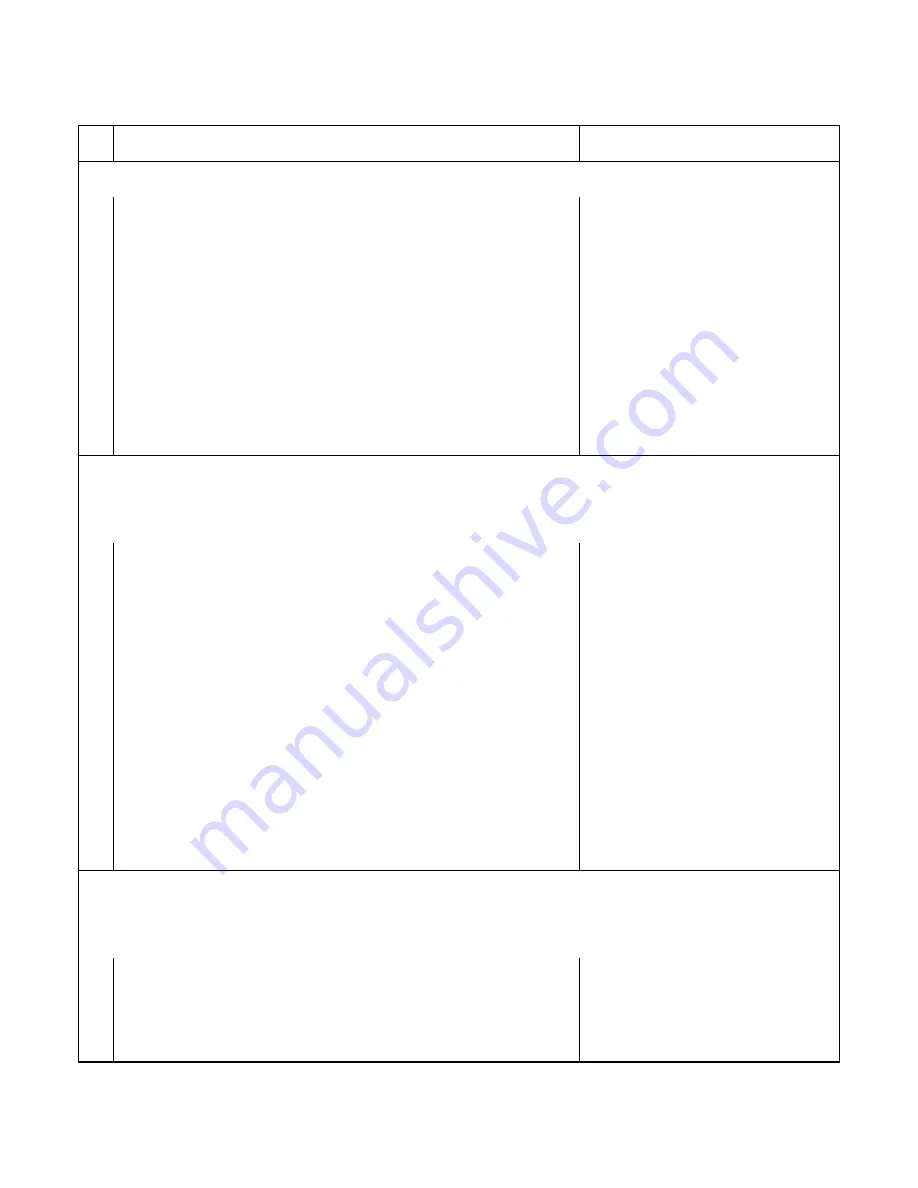
14 Verification
Table 2-4. Constant Voltage (CV) Tests (continued)
Action
Normal Result
CV Source Effect (cont)
4
Adjust the load to produce full-scale current (see Table 2-2) as shown on
the front panel display.
CV
annunciator is on. If it is not, adjust
the load to slightly reduce the output
current until the annunciator comes on.
5
Adjust the transformer to decrease the ac input voltage to the low- line
condition (174Vac or 191Vac). Record the output voltage reading of the
DVM.
6
Adjust the transformer to increase the ac input voltage to the high-line
condition (220Vac or 250Vac). Record the output voltage reading on the
DVM.
7
Check test result.
The difference between the DVM
readings in steps 5 and 6 are within the
specified Source Effect limits.
CV Noise (PARD)
Periodic and random deviations (PARD) in the output (ripple and noise) combine to produce a residual ac voltage
superimposed on the dc output voltage. This test measures CV PARD, specified as the rms and peak-to-peak output
voltages over the frequency range of 20Hz to 20MHz.
1
Turn off the power supply and connect an a-c coupled oscilloscope across
the
+
and
-
output terminals (see Fig. 2-1). Set the oscilloscope bandwidth
limit to 20MHz (30MHz for the Keysight 54504A) and use an RF tip on
the oscilloscope probe.
2
Turn on the power supply and program the current to its maximum
programmable value and the voltage to its full-scale value (see Table 2-2).
3
Adjust the load to produce full-scale current (see Table 2-2) as shown on
the front panel display.
CV
annunciator is on. If it is not, adjust
the load to slightly reduce the output
current until the annunciator comes on.
4
Record the amplitude of the waveform.
Amplitude is within the specified PARD
Peak-to-Peak limits.
5
Replace the oscilloscope connection with an ac rms voltmeter.
6
Record the reading obtained in Step 5.
Amplitude is within the specified PARD
rms limits.
Transient Recovery Time
This test measures the time required for the output voltage to return to within 100mV of its final value following a 50%
change in output load current. Measurements are made on both the unloading transient (from full load to 1/2 load) and the
loading transient (from 1/2 load to full load).
1
Turn off the power supply and connect an oscilloscope across
+S
and
-S
(see Fig. 2-1).
2
Turn on the power supply and program the current to its maximum
programmable value and the voltage to its full-scale value (see Table 2-2).
Summary of Contents for 669 A Series
Page 2: ...Service Manual Keysight Series 669xA GPIB DC Power Supplies ...
Page 3: ......
Page 27: ......
Page 56: ...Troubleshooting 53 Figure 3 15 3 Inch Front Panel Frame Assembly ...
Page 57: ...54 Troubleshooting Figure 3 16 Assembly A10 Exploded View ...
Page 58: ...Troubleshooting 55 Figure 3 17 Assembly A10 Exploded View 6690A ...
Page 59: ...56 Troubleshooting Figure 3 18 Assembly A10 Exploded View 6691A 6692A ...
Page 60: ...Troubleshooting 57 Figure 3 19 Three Phase Line Choke Subchassis Wiring ...
Page 61: ...58 Troubleshooting Figure 3 20 24 Volt Fan Transformer ...
Page 77: ...74 Diagrams Figure 6 1 Test Point Waveforms for Table 6 3 sheet 2 of 2 ...
Page 79: ...Figure 6 3 A1 Front Panel Board Assembly Diagram ...
Page 81: ...Figure 6 5 A2 GPIB Board Component Location ...
Page 83: ...Figure 6 7 A3 FET Board Component and Test Point Location ...
Page 87: ...Figure 6 11 A4 AC Input Board Component and Test Point Location 12 9 10 11 ...
Page 89: ...Figure 6 13 A5 DC Rail Board Component and Test Point Location 13 14 ...
Page 91: ...Figure 6 15 A6 Bias Board Component and Test Point Location 15 16 17 18 19 19 20 22 ...
Page 94: ...Figure 6 17 Power Mesh Schematic Diagram All Models ...
Page 103: ......