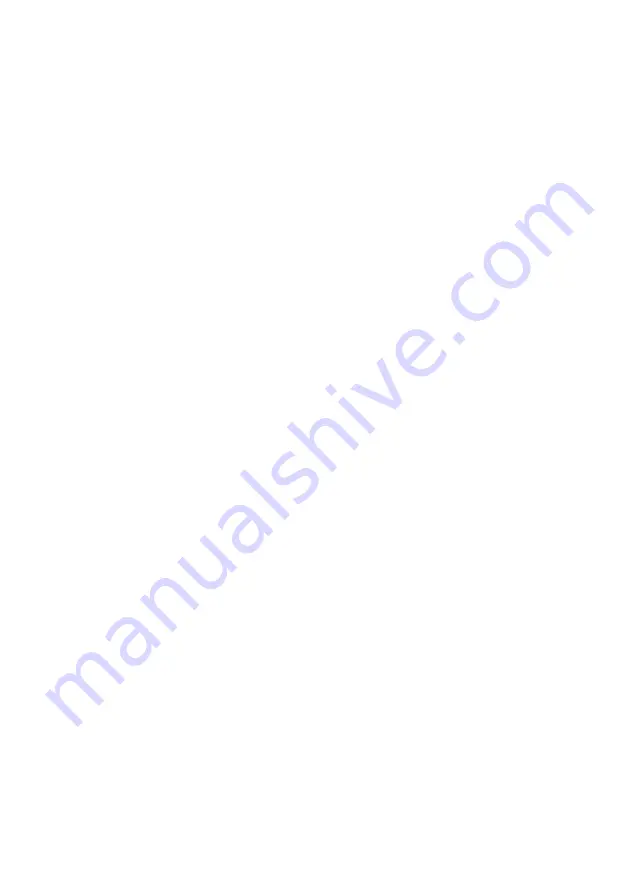
40
3. Assembly & commissioning
3.1. Supplied package
The machine is delivered on a pallet, max. 6 pieces per pallet.
• fully assembled – with a 230 V protective contact plug (sensor is set at the factory)
Optional: • bounce frame
3.2. Checking before commissioning
Before commissioning the “Uno” cow cleaning machine, it must always be checked for completeness,
visible defects or sources of danger.
The following checking measures should be carried out:
• check the machine for loose or hanging parts or damage sustained during transport.
• check the cable insulation.
• check that all safety devices are present and are in perfect working order.
• check whether there are any sources of danger near the machine that could impair the problem-free and safe
operation of the machine (water hoses, influence of weather, hanging cables or ropes, etc.).
3.3. Installation
The best possible positioning and stable securing is particularly important for ensuring the problem-free operation of
this heavy-duty machine.
The following must be noted:
• do not set up the machine in a confined space in the pen.
• to avoid backlogs, do not set up the machine directly before or after the milking station.
• do not set up the machine in proximity to equipment that is sensitive to dust.
• protect the electrical control box from rain and excessive sunlight.
• mount the electrical control box on a stable, vibration-free base to avoid damage to electronic parts caused by
shaking
• mount the machine on a stable concrete wall or pillar
• the surface on which the support arm rests must be level, otherwise the frame can become twisted –> consequen-
tial damage
• use at least 4 heavy duty M12 screws. The fastening material must be chosen appropriate to the base. (masonry,
concrete wall). Where concrete walls are used, heavy-duty anchors are usually sufficient. Where other bases are
used, always use through-bolts.
• when mounting the machine and control box outdoors, protect it with a roof against rain and snow
• only mount the machine using suitable lifting equipment (pulley, front-loader, etc.), noting the relevant accident
prevention regulations!
• secure screws to stop them working themselves loose –> use self-tapping nuts and/or thread lockers
• check securing bolts regularly and re-tighten if necessary.
• the fastening surface (masonry, concrete wall) must be free from vibration and oscillation.
Tip: secure the machine to an even, solid concrete wall. Drill through the concrete wall and screw suitable
steel counter plates or large washers onto the other side of the wall using threaded rods onto the sup-
port arm!
Tip: Attach the base plate first so that you don’t have to hold the entire machine in position. The outside
holes can be used for wall mounting and the inside holes can also be used for pillar mounting.
Mounting height: see Fig. 3 + 4
Average withers height - 680 mm = mounting height
Example: based on an average withers height of 1,350 mm, the mounting height would be 670 mm (1,350 mm
- 680 mm = 670 mm).