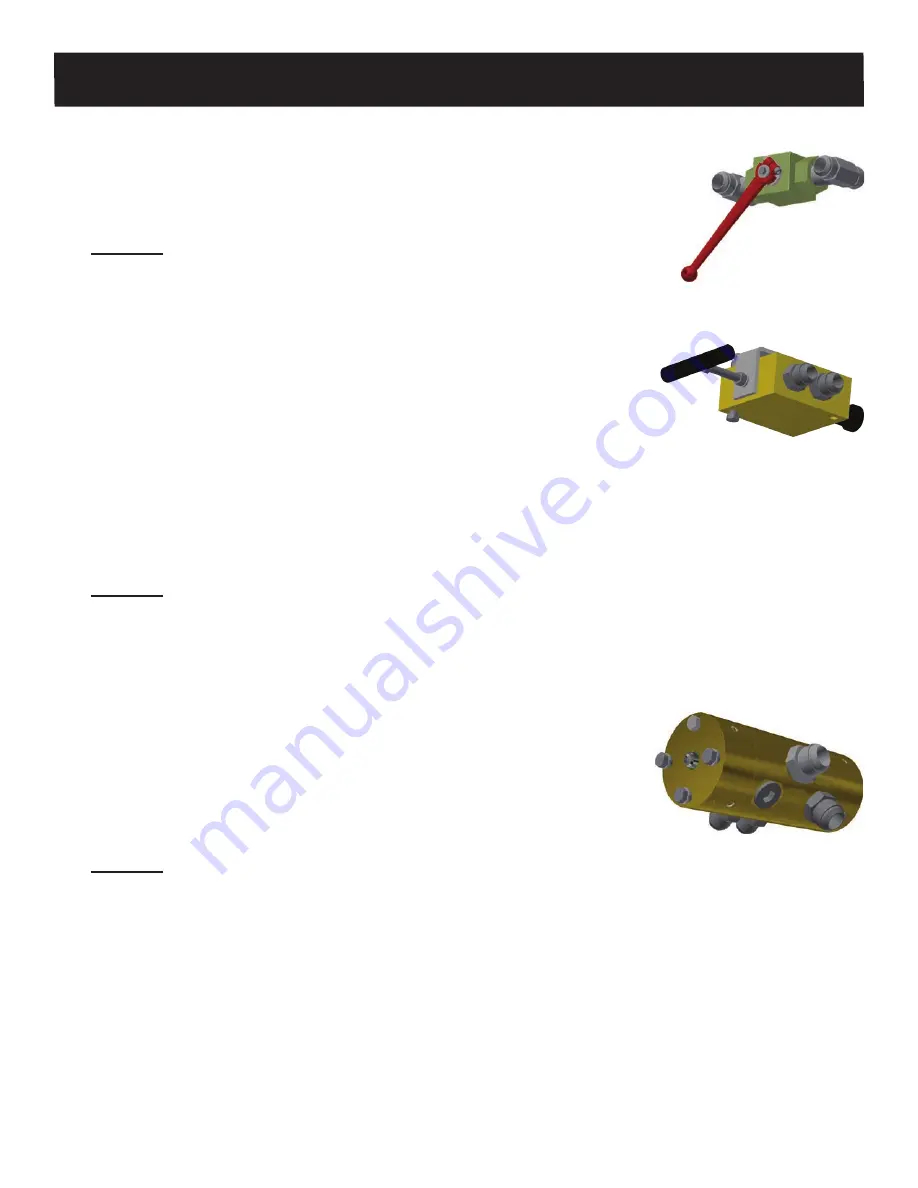
22
DOC06820 Rev. A
SERVICE / REPAIR MANUAL
RUNNING FLOOR II
®
DX
5.3
Component Identification / Function / Problems / Solutions
5.3.1
Ball Valve (On /Off)
•
A closed ball valve routes hydraulic oil flow to the drive system (floor On).
•
An open ball valve redirects hydraulic oil flow back to tank (floor Off).
• Emergency Stop
Problem:
System will not operate or operates slowly.
9
Check to make sure the ball valve is fully closed (pulled out).
9
Check for sound of high-pressure oil bypass and/or excessive heat being generated.
Teflon ball seats could be damaged by heat (replace ball valve)
5.3.2 Control Valve (Load/Unload)
• Controls which check valves are active, determining the direction of
material movement (Load or Unload).
•
Valve pulled out is in unload mode (material offloads).
•
Valve pushed in is in the load mode (material loads).
Note:
Control valves rarely fail under normal use, but may develop seal leaks over time. These leaks
can be eliminated by installing new seals in the valve body. If damage or excessive wear is visible to the
valve body or the valve spool, the valve must be replaced. If the valve has not been used for an extended
period, it may become frozen in place due to contaminants on the valve spool. Do not operate the valve
until it has been thoroughly cleaned of all contaminants and lubricated. Do not force the valve to operate.
Doing so may cause internal damage to the valve body and spool.
Problem:
All cylinders move together to the front of the trailer and then all cylinders move together to the rear of
the trailer. If this continues in both the unload and load cycles, the valve may be in the beginning stage of
failure. Replace the valve. If the control valve is mounted on the outboard side of the trailer with hoses,
check for the proper routing of the hoses. (Consult the Floor To Wet Kit Diagram for proper routing).
5.3.3 Switching Valve
• Switches the hydraulic pressure from one end of the cylinders to the
opposite end of the cylinders, which causes the cylinders to change from
the restage sequence to moving the material then back again.
NOTE:
Many switching valves are unnecessarily replaced when they are
only in need of adjustment. Switching valves almost always fail when they
switch (all cylinders to the front or to the rear of the trailer),
NOT
during the
restage cycle or unload cycle.
Problem:
•
(Unloading) All cylinders restage 1, 2, 3 to the front of the trailer and then the system stops.
•
(Unloading) All cylinders move to the rear of the trailer and then the system stops.
9
Does the system show evidence of high-pressure bypass?
If so, the switching valve may not have switched. Check the threaded rods to see if they have fully
actuated the switching valve. If not, readjust the switching valve. Be mindful that the front rod adjustment
controls the timing of the restage cycle of the cylinders to the front of the trailer. The rear rod controls the
timing of the cylinders for the unloading cycle. The same operating sequence happens, but in reverse
during the loading cycle.
NOTE:
If all the cylinders have stopped to the front or the rear of the trailer and the switching valve has
been switched, try readjusting the switching valve first. If the system still does not work properly after
adjustment, there is a high probability of switching valve failure and it needs to be replaced.