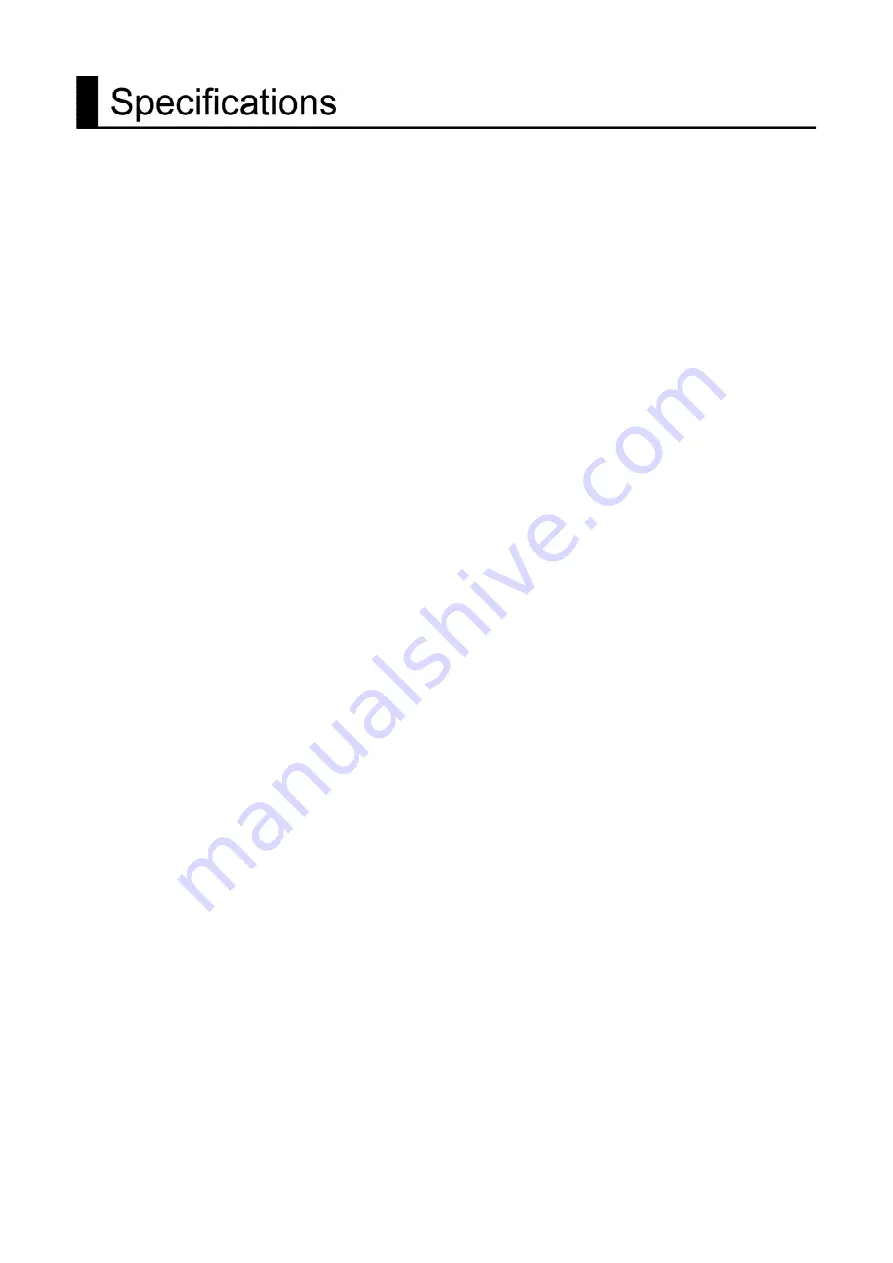
27
External
dimensions
/
weight
300Plus
:
314 (W)
×
396 (H)
×
468 (D) mm 22kg
500Plus
:
415 (W)
×
441 (H)
×
503 (D) mm 33kg
1500Plus
:
510 (W)
×
520 (H)
×
608 (D) mm 49kg
3000Plus
:
600 (W)
×
604 (H)
×
748 (D) mm 82kg
5000Plus
:
670 (W)
×
734 (H)
×
883 (D) mm 118kg
Effective size in furnace
/
300Plus
:
120 (W)
×
110 (H)
×
222 (D) mm 2.9L
Furnace
internal
volume
500
Plus
:
160 (W)
×
130 (H)
×
240 (D) mm 5.0L
1500Plus
:
230 (W)
×
200 (H)
×
300 (D) mm 13.8L
3000Plus
:
300 (W)
×
244 (H)
×
400 (D) mm 29.2L
5000Plus
:
350 (W)
×
300 (H)
×
500 (D) mm 52.5L
Power supply voltage
/
300Plus
:
AC100V
50/60Hz
1.2kVA
Power
consumption
500Plus
:
AC200V Single phase 50/60Hz 1.8kVA
1500Plus
:
AC200V Single phase 50/60Hz 3.6kVA
3000Plus
:
AC200V Single phase 50/60Hz 5.5kVA
5000Plus
:
AC200V Single phase 50/60Hz 8.0kVA
Maximum operating temperature 1150
℃
※
5000 Plus only 1100
℃
Regular
use
temperature 1000
℃
Operating
temperature
range
100
℃~
Maximum operating temperature
Note
)
Temperature distribution and control performance deteriorate
as
the
temperature
decreases
from
around
300
℃
.
Temperature
control
unit
0.5
℃
Temperature control method PID control (20 sets of PID constants, 10 of which are automatic)
with auto tuning
Furnace
material ceramic
fiber-vacuum
molding
Temperature
sensor
JIS
K
thermocouple
※
Optional high temperature compatible platinum pin thermocouple
Heating
element Iron
chrome
wire
Exhaust
hole
diameter
φ
23.5
Maximum
heating
rate
From
normal
temperature to maximum operating temperature
300Plus
:
About 40 minutes
500Plus
:
About 28 minutes
1500Plus
:
About 25 minutes
3000Plus
:
About 28 minutes
5000Plus
:
About 49 minutes
Number
of
programs 50
patterns
/
100 segments
Summary of Contents for 1500-Plus
Page 2: ......