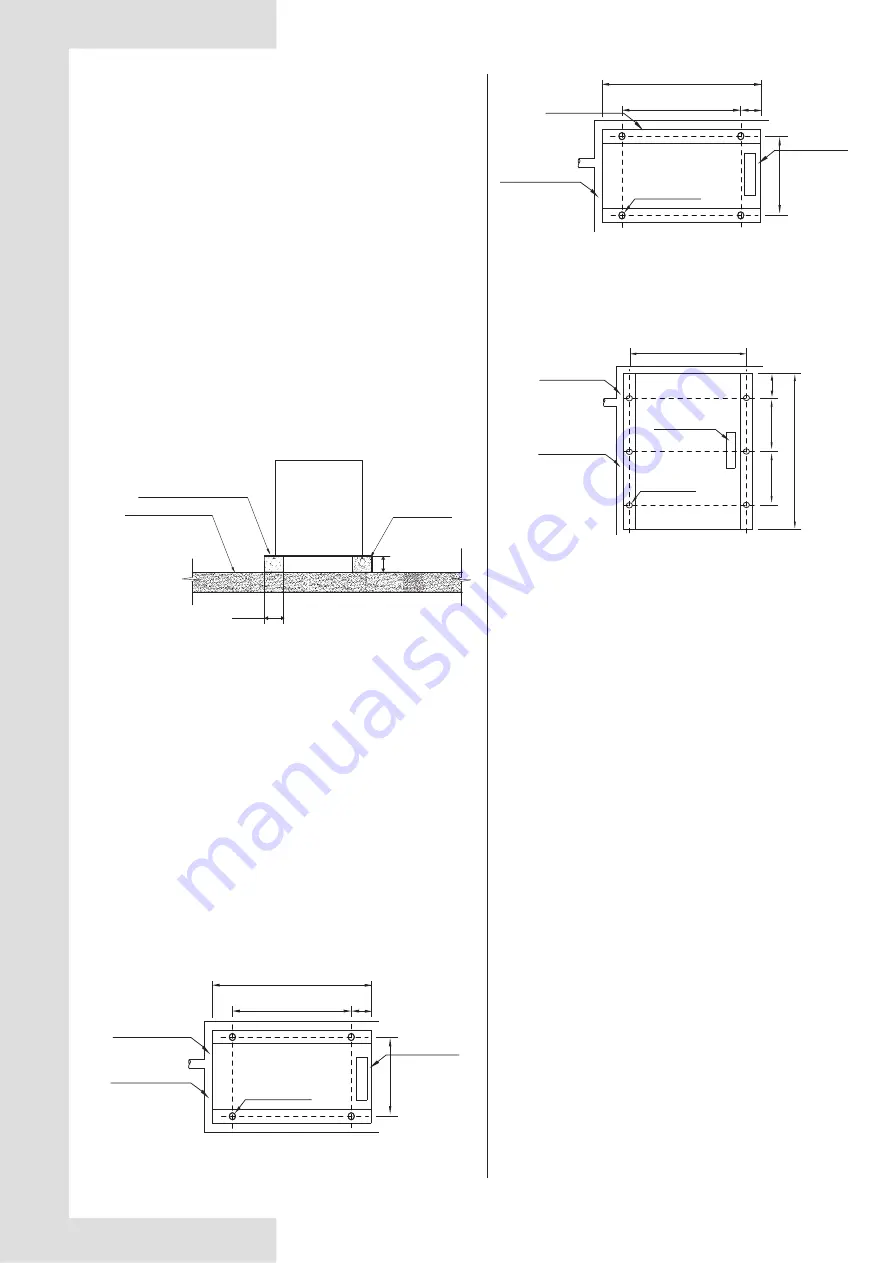
6.3 Installation foundation
6.4 Installation of damping devices
6.4.1 Damping devices must be provided
between the unit and its foundation.
6.3.2 Location drawing of installation
foundation of the unit: (unit: mm)
By means of the Φ15mm diameter installation holes on
the steel frame of the unit base, the unit can be fastened
on the foundation through the spring damper. See
Fig.6-6,6-7 (Schematic diagram of installation dimension
of the unit) for details about center distance of the
installation holes. The damper does not go with the unit,
and the user can select the damper according to the
relevant requirements. When the unit is installed on the
high roof or the area sensitive to vibration, please consult
the relevant persons before selecting the damper.
Step 1. Make sure that the flatness of the concrete
foundation is within ±3mm, and then place the unit on the
cushion block.
Step 2. Raise the unit to the height suitable for
installation of the damping device.
Step 3. Remove the clamp nuts of the damper. Place the
unit on the damper, and align the fixing bolt holes of the
damper with the fixing holes on the unit base.
Step 4. Return the clamp nuts of the damper to the fixing
holes on the unit base, and tighten them into the damper.
Step 5. Adjust the operational height of the damper base,
and screw down the leveling bolts. Tighten the bolts by
one circle to ensure equal height adjustment variance of
the damper.
Step 6. The lock bolts can be tightened after the correct
operational height is reached.
6.4.2 Installation steps of the damper
Top view of schematic diagram of installation
dimension of
KEM-90 DRS5 KH
&
KEM-140
DRS5 KH
Fig. 6-7
1991
Drainage channel
Anchor bolt
1550
862
220
Electric control
Inlet and outlet
box side
pipe side
(unit: mm)
1) A solid base prevents excess vibration and noise. Outdoor
unit bases should be constructed on solid ground or on structures
of sufficient strength to support the units’ weight.
2) Bases should be at least 200mm high to provide sufficient
access for installation of piping.Snow protection should also be
considered for the base height
.
3) Either steel or concrete bases may be suitable.
Outdoor unit base structure design should take account of the
following considerations:
6.3.1 Base structure
4) A typical concrete base design is shown in Fig. 6-5. A typical
concrete specification is 1 part cement, 2 parts sand and 4 parts
crushed stone with steel reinforcing bar. The edges of the base
should be chamfered
5) To ensure that all contact points are equally secure, bases
should be completely level. Base design should ensure that the
points on the units’ bases designed for weight-bearing support
are fully supported.
≥80mm
Fig.6-5 Front view of base structure
Concrete base
h
≥
200mm
Rubber anti-vibration pads
Solid ground / surface
≥
200mm
Outdoor unit
1) If the unit is located so high that it is inconvenient for
maintenance personnel to conduct maintenance, the suitable
scaffold can be provided around the unit.
2) The scaffold must be able to bear the weight of
maintenance personnel and maintenance facilities.
3) The bottom frame of the unit is not allowed to be embedded
into the concrete of installation foundation.
4) A drainage ditch should be provided to allow drainage of
condensate that may form on the heat exchangers when the
units are running in heating mode. The drainage should ensure
that condensate is directed away from roadways and
footpaths, especially in locations where the climate is such that
condensate may freeze.
2200
Drainage channel
Anchor bolt
1460
1017
370
(unit: mm)
Top view of schematic diagram of
installation dimension of
KEM-75 DRS5 KH
Inlet and outlet
pipe side
Electric control
box side
Fig. 6-6
Top view of schematic diagram of
installation dimension of
KEM-180 DRS5 KH
Fig. 6-8
Drainage channel
Anchor bolt
2120
403
(unit: mm)
974
Inlet and outlet
pipe side
Electric control
box side
2752
974
09