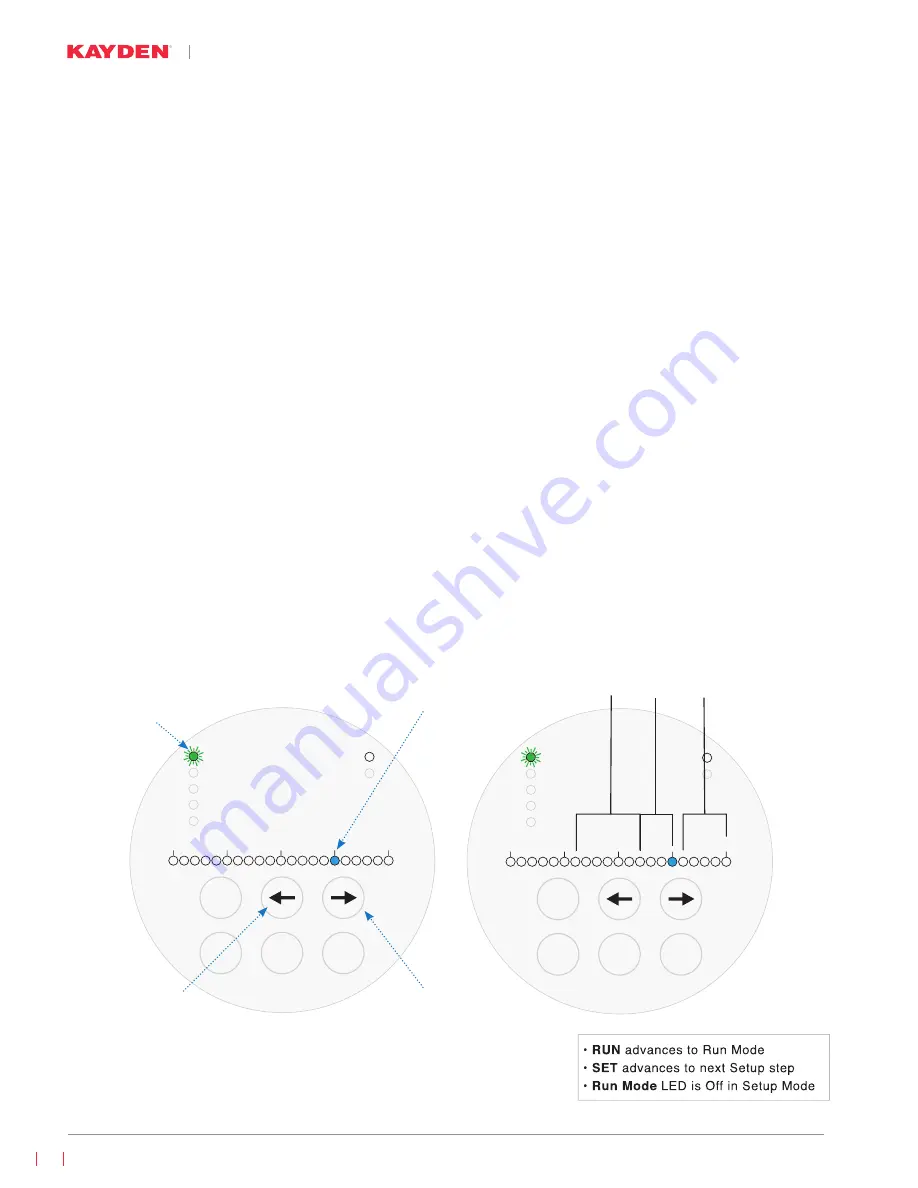
36
kayden.com Online Store
CLASSIC
®
800 Product Manual
Setup & Operation
5. View or Adjust the Heater Power
•
The correct heater setting is determined primarily by the process media and secondarily by the velocity
of the process. The heater setting is a key factor in determining the sensitivity and reaction time of the
switch/transmitter.
•
The CLASSIC 800’s sensor heater produces 2 Watts at full power.
•
The “Smart Heater” function in the CLASSIC 800 Series continously monitors the Thermal Signal.
If the Thermal Signal falls to zero, the heater power is automatically reduced from the user
setting to prevent the creation of a “Thermal Offset”. The heater power will be restored to the
user setting when the Thermal Signal increases.
•
The Factory Default setting of 75% is optimal (70 - 80% depending on velocity) for Hydrocarbon-
based liquids and suitable for many applications. The CLASSIC 800 allows the Heater Power to
be set between 0% and 100% in 5% steps.
•
RECOMMENDED HEATER POWER SETTINGS:
•
30 - 60% heater power
(
7-13 LEDs
) - Air or Gas (Flow) (depending on velocity)
•
60 - 75% heater power
(
13-16 LEDs
) - Oil or Hydrocarbon based liquids
(Flow, Level & Interface)
•
80 - 100% heater power
(
17-21 LEDs
) - Water or non-viscous liquids
(Flow, Level & Interface)
The faster the flow rate (velocity) the more heat is required. In level applications the amount of heat,
in part, determines the reaction time.
Note:
The heater power is shown when using Kayden RCM software in the Graph view.
Figure 27 - Setting the Heater Power
Thermal Signal
100%
0
Relay 1
Relay 2
Fault
Set Point 1
Set Point 2
Run Mode
Bypass
RUN
SET
1
2
CLASSIC
™
Thermal Signal
100%
0
Relay 1
Relay 2
Fault
Set Point 1
Set Point 2
Run Mode
Bypass
RUN
SET
1
2
CLASSIC
™
Air/Gas
Water
Oil
Relay 1 is
flashing
Decrease
Heater Power
Increase
Heater Power
Single LED displays
Heater Power setting
Recommended Heater
Power Settings