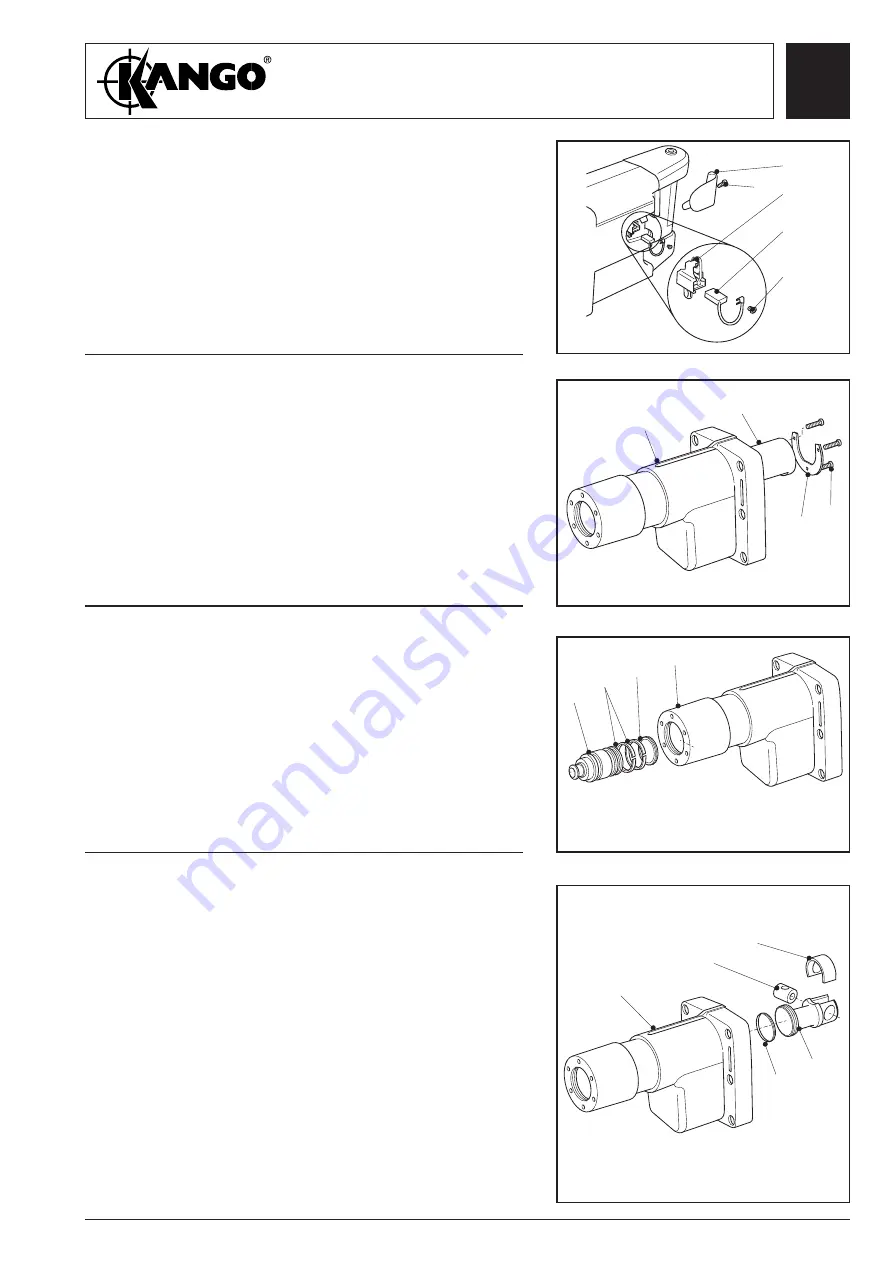
17
Service and Repair Manual
Model 1400KV/1400BV
Fig. 25
Fig. 26
Fig. 27
Refitting/
Replacing the
Brushes
1.
Lever the retaining spring (68) upwards and
insert the brush(s) (71). Ensure the correct fitting.
2.
Secure the brush lead with retaining screw (94).
3.
Fit and secure brush covers (75), with screws
(76).
Refitting the
Barrel
Assembly
1.
Locate and fit the barrel assembly (37) with the
'cut-out' toward the inclined shaft bearing mount.
2.
Temporarily fit the location ring (21) to give
correct depth of barrel assembly (37). Press home
the barrel assembly (37), ensure the correct
alignment of ISB slot.
3.
Insert the barrel retaining bracket (38) ensuring
correct location of lug. Fit retaining screws (31).
4.
Remove location ring (21).
1.
Fit bearing clips (24) to striker (23).
Note:
Fit striker to barrel and check for free
movement. If restricted discard the clips for
better fit.
2.
Fit the Nu-lip Seal (25) to striker (23).
3.
Lightly lubricate the assembly (23) and fit into the
barrel.
Refitting the
Striker
Assembly
Assembly and
Refitting the
Piston
Assembly
1.
Fit the gudgeon pin (43) and retainer clip (44) to
the piston (45).
2.
Fit the Nu-lip Seal (42).
3.
Fit piston assembly (45), into the barrel (34).
Note:
Refer to lubrication diagram for piston area
lubrication.
31
38
34
37
23
24
25
34
45
44
42
34
43
Fig. 28
75
68
71
94
76
Summary of Contents for 1400 Series
Page 1: ......