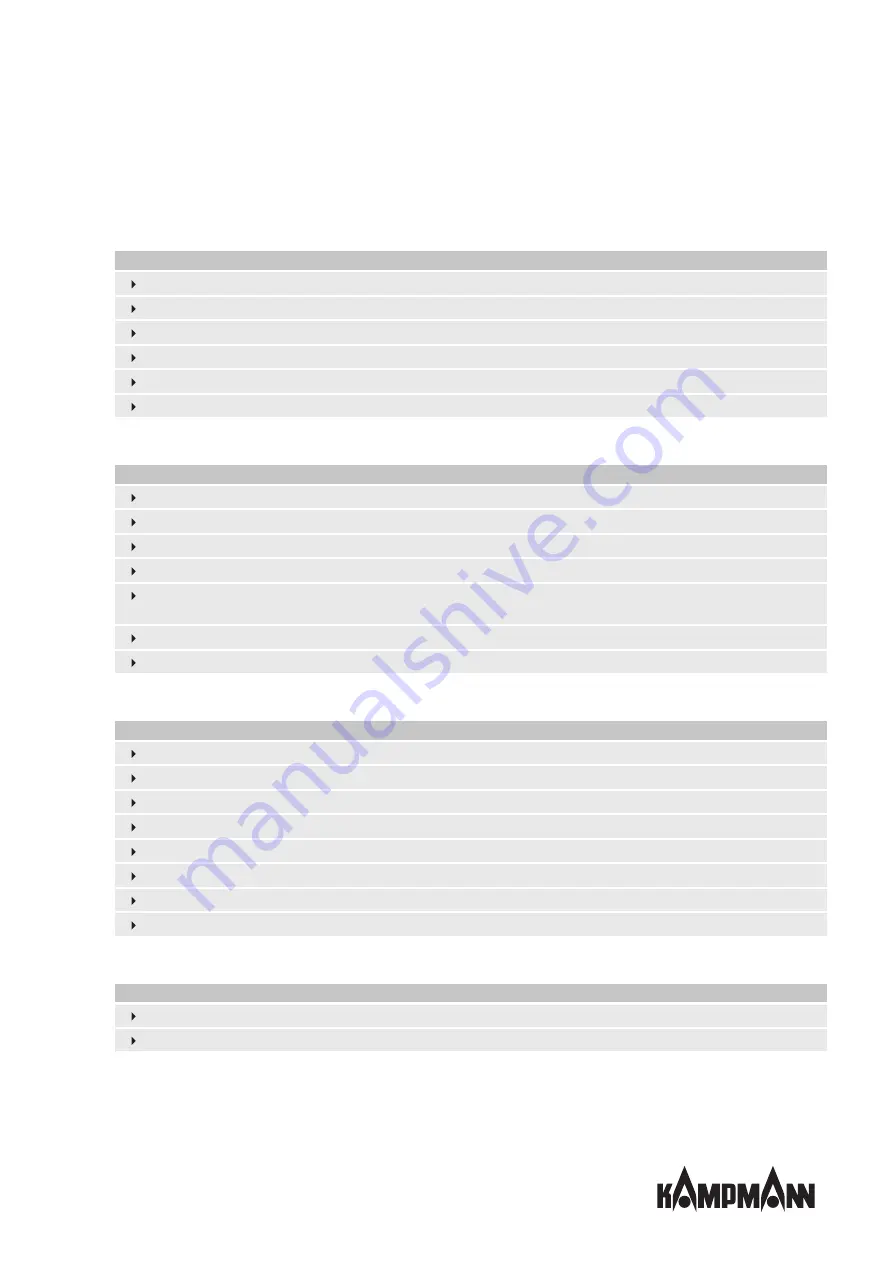
Ultra
Assembly, installation and operating instructions
49
8
Pre-commissioning checks
Before initial commissioning, check whether all the necessary conditions have been met so that the unit can function safely
and properly.
Structural tests
Check that the unit is securely standing and fixed.
Check the horizontal installation/suspension of the unit.
Check the completeness and correct seating of all filters (dirt side).
Check whether all components are properly fitted.
Check whether all air ducts are mechanically fixed in place.
Check whether all dirt, such as packaging or site dirt, has been removed.
Electrical tests
Check whether all lines have been properly laid.
Check whether all lines have the necessary cross-section.
Are all wires connected in accordance with the electric wiring diagrams?
Is the earth wire connected and wired throughout?
Check whether the fault signal contacts of the EC fans have been correctly connected (break contacts in series with
multiple units).
Check all external electrical connections and terminal connections are fixed in place and tighten if necessary.
Check whether DIP switches have been correctly set in accordance with the wiring diagram.
Water-side checks
Check whether all supply and drainage lines have been properly connected.
Fill pipes and unit with water and bleed.
Check whether all bleed screws are closed.
Check leak tightness (pressure test and visual inspection).
Check whether the parts carrying water have been flushed through.
Check whether any shut-off valves fitted on site are open.
Check whether any electrically actuated shut-off valves have been properly connected.
Check whether all valves and actuators are working properly (note permitted mounting position).
Air-side checks
Check whether there is unimpeded flow at the air inlet and outlet.
Check whether the air inlet filter is fitted and dirt-free.