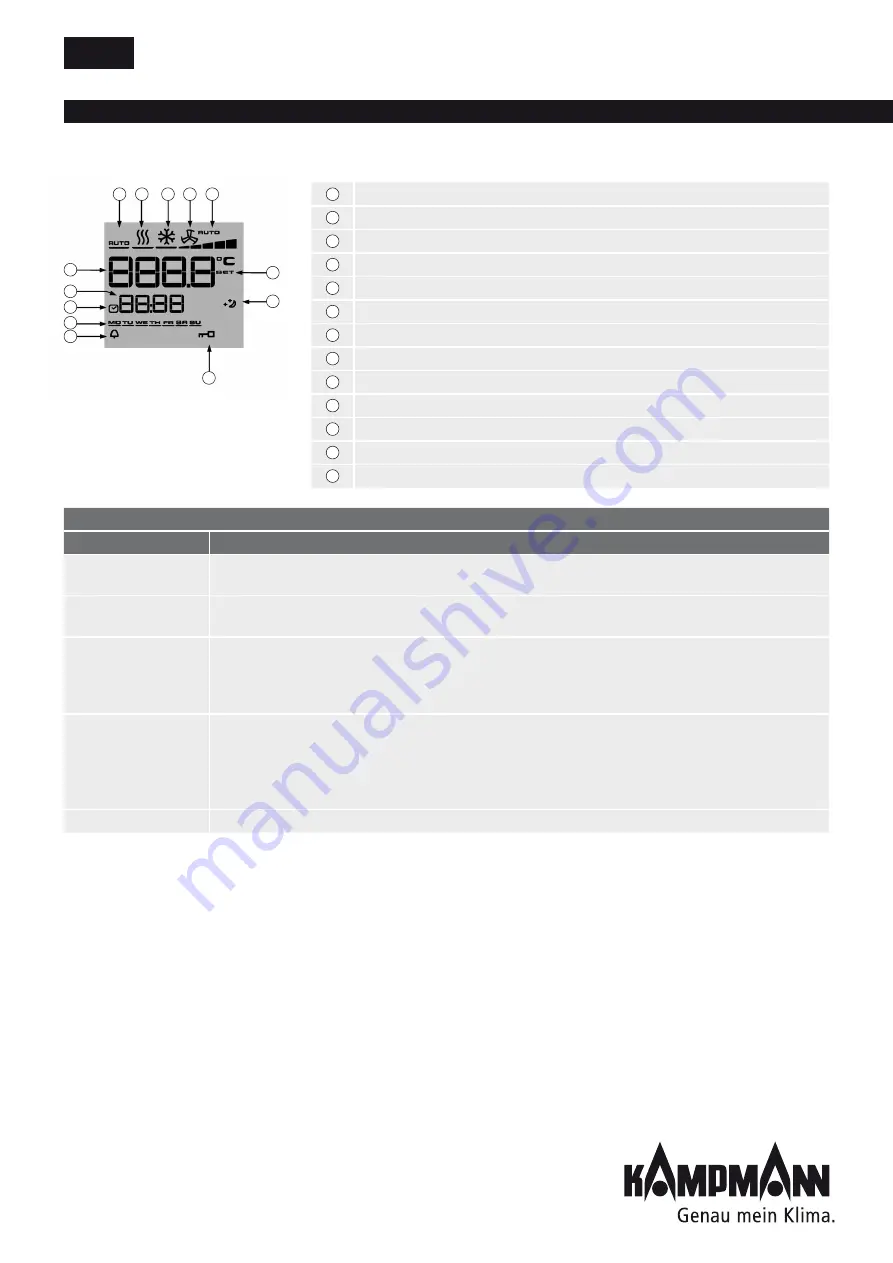
32
.
1.42
Katherm QK –
Trench convector with energy-efficient EC tangential fan
Ready-to-install convector-based trench convectors
Assembly and installation instructions
LCD display symbols
1
Display of setpoint room temperature
2
Current time
3
Timer program enabled
4
Weekday
5
Alarm
6
Selected function is locked
7
Eco mode
8
Setpoint setting enabled
9
Fan control setting Auto-0-1-2-3-4-5
10
Ventilation mode
11
Cooling mode
12
Heating mode
13
Automatic Heating/Cooling changeover mode
Operation of the basic functions
Function
Description
Switch On/Off
Switch on by pressing key 2 or the navigator dial. When switched on, the display shows a temperature. Switch off
by pressing button 2 or the navigator dial. OFF is shown.
Change temperature
Turn the navigator dial to the left to lower, and to the right to increase, the required temperature. Confirm the
entry by pressing the navigator dial.
Fan speed
Change by pressing the side fan button or using the navigator dial. Briefly press the navigator dial once. Turn the
navigator dial to the left to lower, and to the right to increase, the required fan speed. Press the navigator dial
once more to confirm the display.
In Automatic mode, the speed is adjusted when the room temperature deviates from the setpoint temperature.
Heating/Cooling/
Recirculation
Change by pressing the side fan button or using the navigator dial.
To change using the navigator dial, first press the navigator dial for approx. 1 second to move to the Fan stage
selection. Then press the navigator dial once again for 3 seconds to go to the Time setting. Press again for approx.
3 seconds to move to the Timer menu. Press again for approx. 3 seconds to move to the Mode menu. Press briefly
to confirm the entry.
Timer program
The KaControl provides the option of setting a weekly timer. Refer to the separate KaControl instructions for this.
9
10
11
12
13
1
2
3
4
5
6
7
8