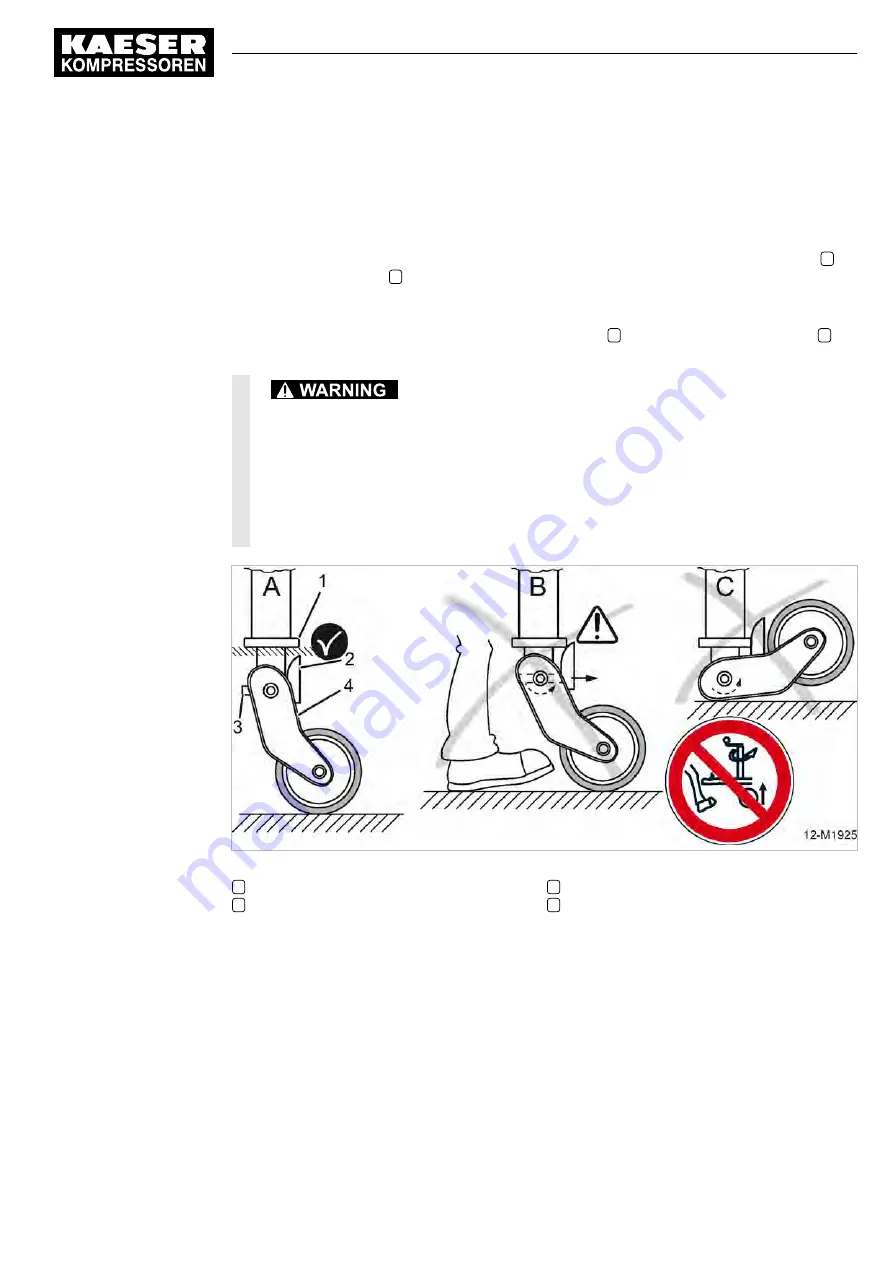
12.2.3.2 Option rb/rm/rs
Parking a machine with a height-adjustable chassis and automatic jockey wheel
In a parked machine which is separated from the towing vehicle, the machine's bearing load affects
the automatic jockey wheel.
For this reason, the jockey wheel of a separated machine must be wound down until the cam
2
no
longer touches the bead
1
. The automatic folding of the wheel suspension is thus blocked (see
figure 82/A).
When the jockey wheel of a separated machine is wound up further, the bead pushes against the
cam of the retaining pin (see figure 82/B). The retaining pin
3
unlocks the wheel suspension
4
which will abruptly fold (see figure 82/C).
A folding wheel suspension during winding up causes the towing device to suddenly crash
onto the ground,
potentially causing severe injuries to legs and/or feet.
➤ Wind the automatic jockey wheel only up when the machine is coupled to a towing vehi‐
cle.
➤ Wind the automatic jockey wheel up only as far as the bead does not touch the cam.
➤ Do not place your feet beneath the towing device.
Fig. 82 Warning: Risk of injury due to falling towing device!
1
Bead
2
Cam
3
Retaining pin
4
Wheel suspension
1. Use a coupled towing vehicle to move the machine into position.
2. Place chocks under the wheels.
3. Loosen the lighting and signalling system.
4. Pull on the parking brake past the dead point zone (see figure 81).
The gas spring holds the brake under tension.
5. Detach the breakaway cable.
6. Lower the jockey wheel.
7. Pull the coupling handle up and lower the jockey wheel further.
The ball coupling must be released from the towing device of the towing vehicle.
12 Decommissioning, Storage and Transport
12.2 Transport
No.: 9_9548 05 USE
Operator Manual Screw Compressor
M27
227
Summary of Contents for M27
Page 260: ...13 Annex 13 4 Wiring diagrams 250 Operator Manual Screw Compressor M27 No 9_9548 05 USE...
Page 261: ...13 Annex 13 4 Wiring diagrams No 9_9548 05 USE Operator Manual Screw Compressor M27 251...
Page 262: ...13 Annex 13 4 Wiring diagrams 252 Operator Manual Screw Compressor M27 No 9_9548 05 USE...
Page 263: ...13 Annex 13 4 Wiring diagrams No 9_9548 05 USE Operator Manual Screw Compressor M27 253...
Page 264: ...13 Annex 13 4 Wiring diagrams 254 Operator Manual Screw Compressor M27 No 9_9548 05 USE...
Page 265: ...13 Annex 13 4 Wiring diagrams No 9_9548 05 USE Operator Manual Screw Compressor M27 255...
Page 266: ...13 Annex 13 4 Wiring diagrams 256 Operator Manual Screw Compressor M27 No 9_9548 05 USE...
Page 267: ...13 Annex 13 4 Wiring diagrams No 9_9548 05 USE Operator Manual Screw Compressor M27 257...
Page 268: ...13 Annex 13 4 Wiring diagrams 258 Operator Manual Screw Compressor M27 No 9_9548 05 USE...
Page 270: ...13 Annex 13 4 Wiring diagrams 260 Operator Manual Screw Compressor M27 No 9_9548 05 USE...
Page 271: ...13 Annex 13 4 Wiring diagrams No 9_9548 05 USE Operator Manual Screw Compressor M27 261...
Page 272: ...13 Annex 13 4 Wiring diagrams 262 Operator Manual Screw Compressor M27 No 9_9548 05 USE...
Page 273: ...13 Annex 13 4 Wiring diagrams No 9_9548 05 USE Operator Manual Screw Compressor M27 263...
Page 274: ...13 Annex 13 4 Wiring diagrams 264 Operator Manual Screw Compressor M27 No 9_9548 05 USE...
Page 276: ...13 Annex 13 4 Wiring diagrams 266 Operator Manual Screw Compressor M27 No 9_9548 05 USE...
Page 277: ...13 Annex 13 4 Wiring diagrams No 9_9548 05 USE Operator Manual Screw Compressor M27 267...
Page 278: ...13 Annex 13 4 Wiring diagrams 268 Operator Manual Screw Compressor M27 No 9_9548 05 USE...
Page 279: ...13 Annex 13 4 Wiring diagrams No 9_9548 05 USE Operator Manual Screw Compressor M27 269...
Page 281: ...13 Annex 13 4 Wiring diagrams No 9_9548 05 USE Operator Manual Screw Compressor M27 271...
Page 282: ...13 Annex 13 4 Wiring diagrams 272 Operator Manual Screw Compressor M27 No 9_9548 05 USE...
Page 283: ...13 Annex 13 4 Wiring diagrams No 9_9548 05 USE Operator Manual Screw Compressor M27 273...
Page 284: ...13 Annex 13 4 Wiring diagrams 274 Operator Manual Screw Compressor M27 No 9_9548 05 USE...
Page 286: ...13 Annex 13 4 Wiring diagrams 276 Operator Manual Screw Compressor M27 No 9_9548 05 USE...
Page 287: ...13 Annex 13 4 Wiring diagrams No 9_9548 05 USE Operator Manual Screw Compressor M27 277...
Page 288: ...13 Annex 13 4 Wiring diagrams 278 Operator Manual Screw Compressor M27 No 9_9548 05 USE...
Page 289: ...13 Annex 13 4 Wiring diagrams No 9_9548 05 USE Operator Manual Screw Compressor M27 279...