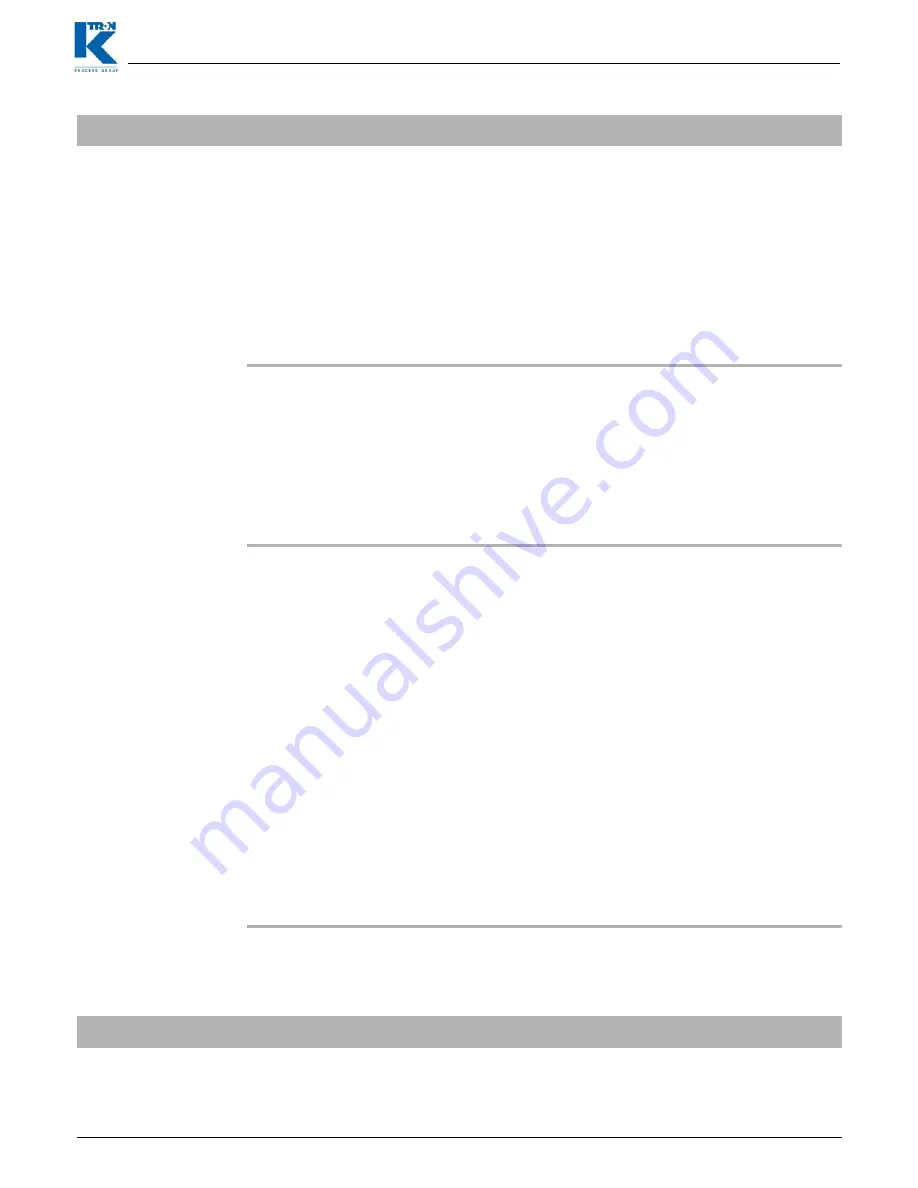
Docu-No.: 0590020601-EN Rev. 1.6.0
Page 79
Alarm Messages- Cause and Remedy
4
Massflow variances in LWF feeding 4.6
General massflow
fluctuations LWF
(continued)
During Refill:
MASSFLOW HIGH.
• Increased degree of feeder-screw
filling or even the material is flowing
through during refilling.
• Pressure increase in the hopper dur-
ing refilling. The reduction in pres-
sure when refilling is completed af-
fects the weight.
Increase lower refilling level in
program parameter <PRODUCT
CHANGE> menu, <REFILL MIN>,
reduce the refilling speed or fit
different feeder screws if
necessary.
Make sure that the air can escape
more easily. Replace the hopper's
air filter if necessary.
Increase <POST REFILL DELAY>.
• Friction on the scales
(to be ascertained with a static
weight test).
• Pressure fluctuations in the storage
container caused by pressure,
suction or insufficient ventilation.
Check all mechanical connections
to the scale, they must be flexible.
The scale may not touch anything.
Replace scale.
Improve ventilation, install a
pressure compensator on the
ventilation connection during the
suction process.
During Refill:
MASSFLOW LOW
• Fluidized material caused by the
vortices of air in the hopper during
refilling.
• Continuous trickle from the refilling
device.
• The weight can be adversely
affected if refilling is not stopped in
time (within a few seconds).
Increase lower refilling level in
program parameter <PRODUCT
CHANGE> menu, <REFILL MIN>,
reduce the refilling speed if
necessary.
If equipped with pneumatic slide
gates, make sure that the slide
gate closes sufficiently.
Where liquids are being processed,
the refilling valve must be located
directly above the hopper.
Increase mode-switch delay in
program parameter <PRODUCT
CHANGE> menu, <POST REFILL
DELAY>.
• Hopper is overfilled. The material is
contacting the inlet portion thus
causing friction in weighing.
Reduce the top refilling level in
program parameter <PRODUCT
CHANGE> menu, <REFILL MAX>,
reduce the refilling speed.
Alarms
Cause
Remedy
Table page 2 of 2