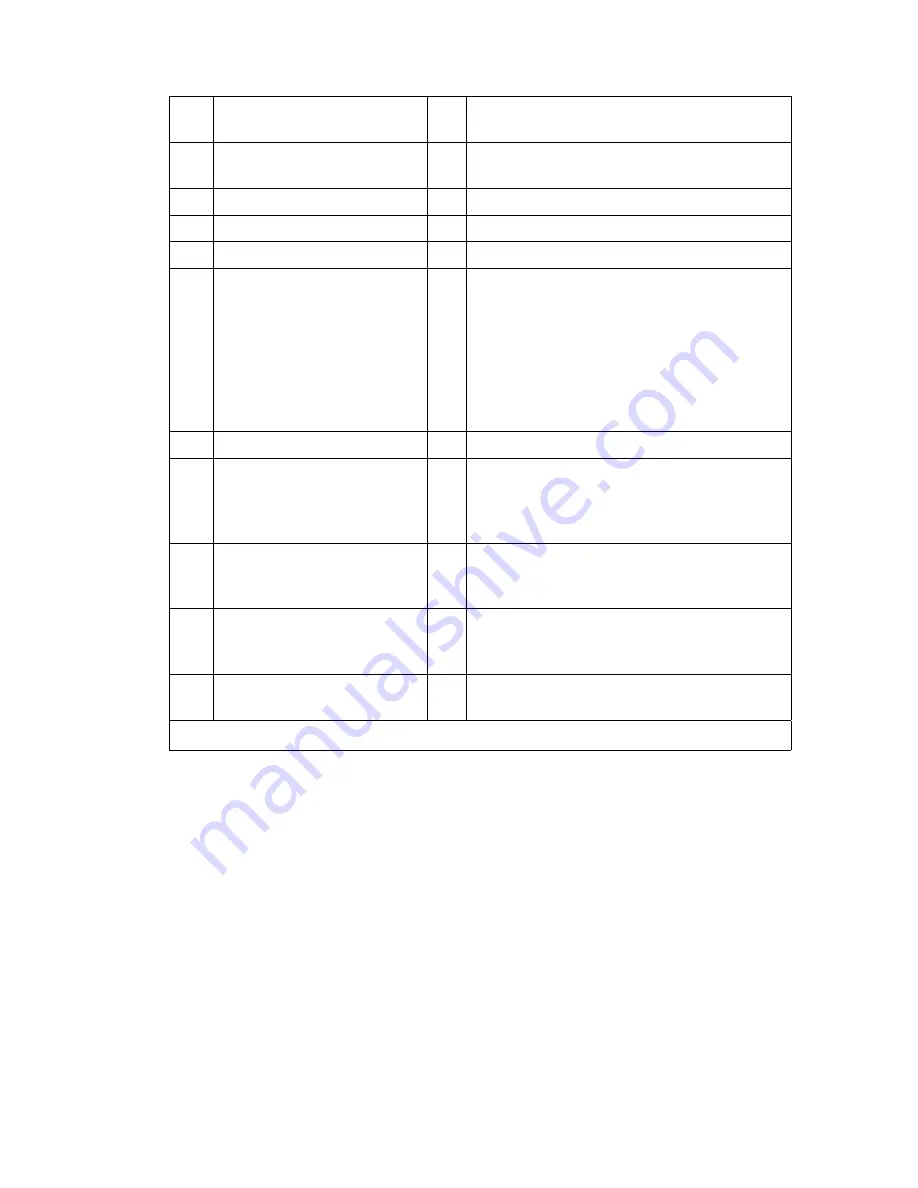
E 2
0799
.G
B
2
Description of the operating controls and indicators
Pos.
Bedien- bzw.
Anzeigeelement
Funktion
1 Controller
t
Controls the direction of travel as well as
the travelling speed.
2 Operating key “Lifting”
t
Lifts the lifting device.
3 Operating key “Lowering”
t
Lowers the lifting device.
4 Operating key “Horn”
t
Gives an audible warning signal.
5 Combined instrument
Information and service
indicator
o
o
Indicates the remaining capacity of the
battery and the hours of operation that the
truck has already performed
(see chapter D, section 6).
Indicates important driving and lifting para-
meters, warning messages, notes on
operation faults and service information
(see chapter E, section 5).
6 Steering
t
Steering the truck.
7 Key switch
t
Switches the control current on and off.
When the key is removed from the key
switch, the truck cannot be operated by
unauthorised persons.
8 Master switch
(emergency stop)
t
The circuit is interrupted, all electrical
functions are switched off and the truck is
automatically braked.
9 Dead man's switch
t
- released:
Driving function blocked or
truck is slowing down
- operated:
Driving function released
10 Sitting aid adjusting screw
t
Adjusting the inclination angle of the sitting
aid.
t
= Standard equipment
o
= Optional equipment
E 2
0799
.G
B
2
Description of the operating controls and indicators
Pos.
Bedien- bzw.
Anzeigeelement
Funktion
1 Controller
t
Controls the direction of travel as well as
the travelling speed.
2 Operating key “Lifting”
t
Lifts the lifting device.
3 Operating key “Lowering”
t
Lowers the lifting device.
4 Operating key “Horn”
t
Gives an audible warning signal.
5 Combined instrument
Information and service
indicator
o
o
Indicates the remaining capacity of the
battery and the hours of operation that the
truck has already performed
(see chapter D, section 6).
Indicates important driving and lifting para-
meters, warning messages, notes on
operation faults and service information
(see chapter E, section 5).
6 Steering
t
Steering the truck.
7 Key switch
t
Switches the control current on and off.
When the key is removed from the key
switch, the truck cannot be operated by
unauthorised persons.
8 Master switch
(emergency stop)
t
The circuit is interrupted, all electrical
functions are switched off and the truck is
automatically braked.
9 Dead man's switch
t
- released:
Driving function blocked or
truck is slowing down
- operated:
Driving function released
10 Sitting aid adjusting screw
t
Adjusting the inclination angle of the sitting
aid.
t
= Standard equipment
o
= Optional equipment
E 2
0799
.G
B
2
Description of the operating controls and indicators
Pos.
Bedien- bzw.
Anzeigeelement
Funktion
1 Controller
t
Controls the direction of travel as well as
the travelling speed.
2 Operating key “Lifting”
t
Lifts the lifting device.
3 Operating key “Lowering”
t
Lowers the lifting device.
4 Operating key “Horn”
t
Gives an audible warning signal.
5 Combined instrument
Information and service
indicator
o
o
Indicates the remaining capacity of the
battery and the hours of operation that the
truck has already performed
(see chapter D, section 6).
Indicates important driving and lifting para-
meters, warning messages, notes on
operation faults and service information
(see chapter E, section 5).
6 Steering
t
Steering the truck.
7 Key switch
t
Switches the control current on and off.
When the key is removed from the key
switch, the truck cannot be operated by
unauthorised persons.
8 Master switch
(emergency stop)
t
The circuit is interrupted, all electrical
functions are switched off and the truck is
automatically braked.
9 Dead man's switch
t
- released:
Driving function blocked or
truck is slowing down
- operated:
Driving function released
10 Sitting aid adjusting screw
t
Adjusting the inclination angle of the sitting
aid.
t
= Standard equipment
o
= Optional equipment
E 2
0799
.G
B
2
Description of the operating controls and indicators
Pos.
Bedien- bzw.
Anzeigeelement
Funktion
1 Controller
t
Controls the direction of travel as well as
the travelling speed.
2 Operating key “Lifting”
t
Lifts the lifting device.
3 Operating key “Lowering”
t
Lowers the lifting device.
4 Operating key “Horn”
t
Gives an audible warning signal.
5 Combined instrument
Information and service
indicator
o
o
Indicates the remaining capacity of the
battery and the hours of operation that the
truck has already performed
(see chapter D, section 6).
Indicates important driving and lifting para-
meters, warning messages, notes on
operation faults and service information
(see chapter E, section 5).
6 Steering
t
Steering the truck.
7 Key switch
t
Switches the control current on and off.
When the key is removed from the key
switch, the truck cannot be operated by
unauthorised persons.
8 Master switch
(emergency stop)
t
The circuit is interrupted, all electrical
functions are switched off and the truck is
automatically braked.
9 Dead man's switch
t
- released:
Driving function blocked or
truck is slowing down
- operated:
Driving function released
10 Sitting aid adjusting screw
t
Adjusting the inclination angle of the sitting
aid.
t
= Standard equipment
o
= Optional equipment
Summary of Contents for ese 20
Page 1: ...Operating instructions 50042902 ESE 20 G 04 99 07 99 ...
Page 3: ...0108 GB ...
Page 7: ...A 2 0499 GB ...
Page 26: ...E 3 0799 GB 2 3 1 5 10 6 7 8 9 4 ...
Page 28: ...E 5 0799 GB 7 8 9 4 1 ...
Page 53: ......