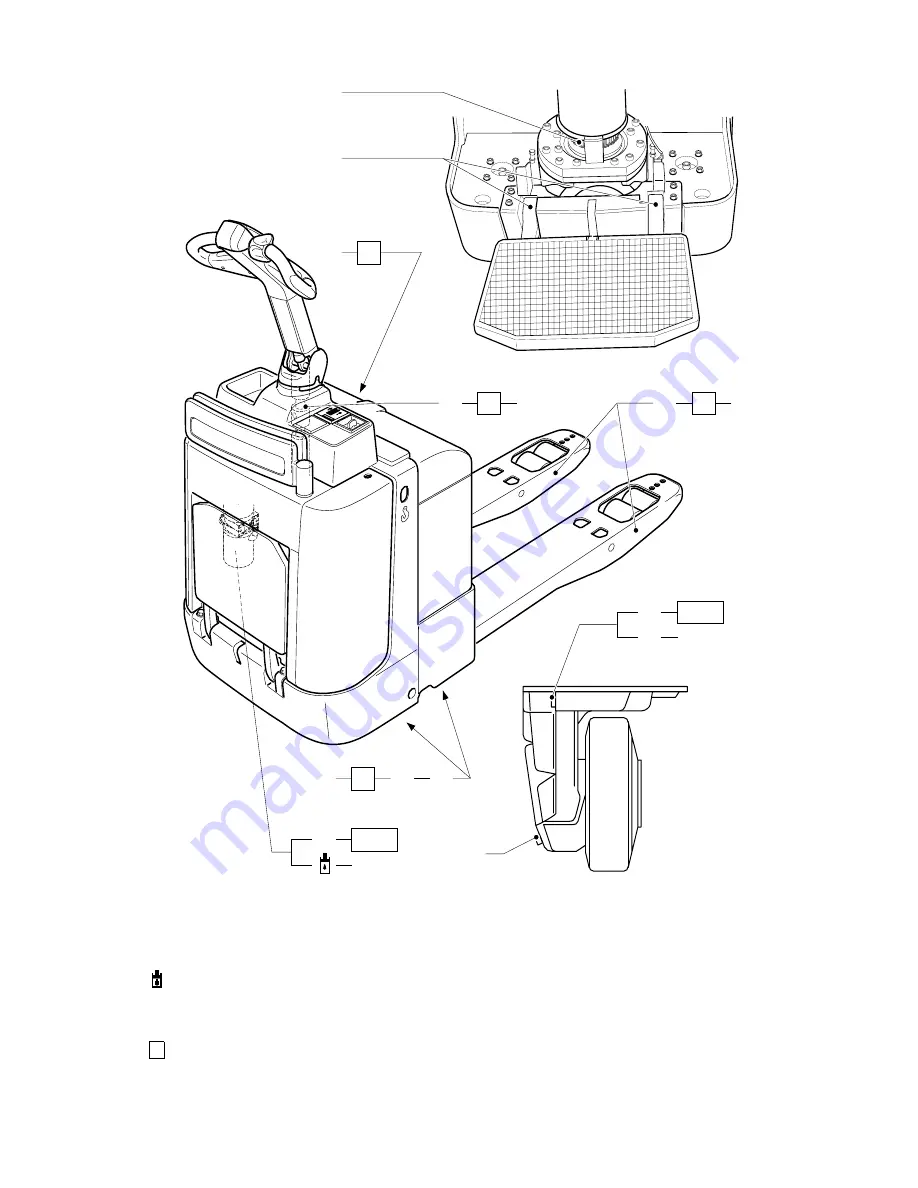
F 6
0106
.GB
5
Lubrication schedule
g
Slide surfaces
1) Compound for cold store usage 1:1
s
Grease nipple
Filler plug for hydraulic oil
2) 1.25 l - 1.3 l
depending on the transmission variant
(level must always reach the lower edge
of the filler neck)
b
Filler plug for transmission oil
a
Drain plug for transmission oil
Cold store operation
E
s
F
A
0,7l
A+C
1)
b
B
B+C
1)
G
C
a
E
F
E
F
s
g
E
s
F
1,25l - 1,3l
2)
F 6
0106
.GB
5
Lubrication schedule
g
Slide surfaces
1) Compound for cold store usage 1:1
s
Grease nipple
Filler plug for hydraulic oil
2) 1.25 l - 1.3 l
depending on the transmission variant
(level must always reach the lower edge
of the filler neck)
b
Filler plug for transmission oil
a
Drain plug for transmission oil
Cold store operation
E
s
F
A
0,7l
A+C
1)
b
B
B+C
1)
G
C
a
E
F
E
F
s
g
E
s
F
1,25l - 1,3l
2)
Summary of Contents for ERE 224
Page 1: ...Operating instructions 50468220 ERE 224 G 09 05 01 06...
Page 3: ...0108 GB...
Page 7: ...1003 GB I 4...
Page 9: ...0506 GB 2...
Page 11: ...0600 GB A 2...
Page 19: ...09 05 GB B 8...
Page 23: ...1003 GB C 4...
Page 32: ...E 3 1003 GB 1 11 12 11 12 10 2 6 7 8 10 13 3 4 5 5 5 15 16 17 18 19 9 11 12 11 12 10 10 9 14...
Page 34: ...E 5 1003 GB 1 11 12 11 12 10 2 6 7 8 10 13 3 4 5 5 5 15 16 17 18 19 9 11 12 11 12 10 10 9 14...
Page 38: ...E 9 1003 GB 5 15 14 9 16 19 1 B B B F R V 0 4 9 2 1 2 2 R V 3 13...
Page 40: ...E 11 1003 GB 5 15 14 9 16 19 1 B B B F R V 0 4 9 2 1 2 2 R V 3 13...
Page 42: ...E 13 1003 GB 5 15 14 9 16 19 1 B B B F R V 0 4 9 2 1 2 2 R V 3 13...
Page 57: ......
Page 87: ...0506 GB 18...