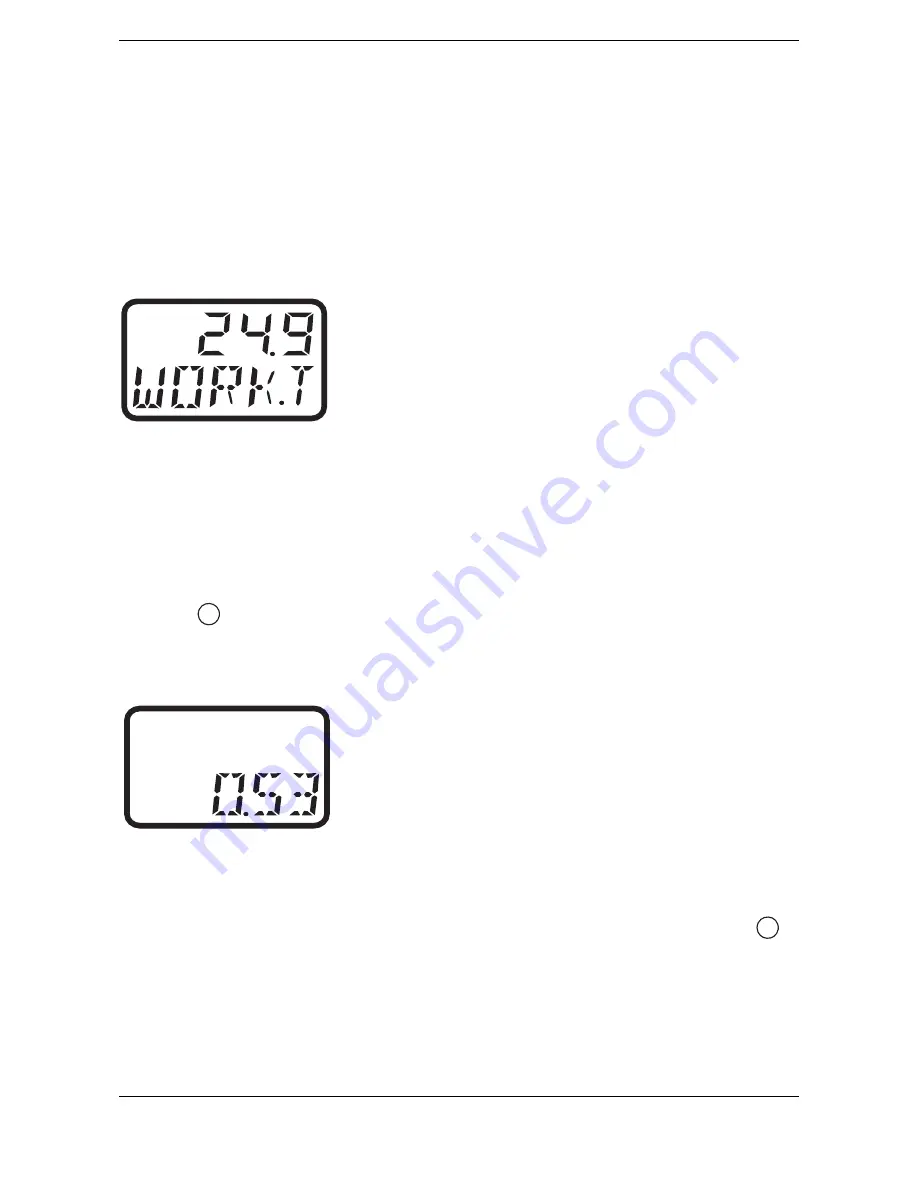
47
8.5 Calibrating the temperature coefficient using
manual temperature entry
Note
During calibration, the reference temperature and the working
temperature can be approached in any sequence.
✱
Immerse the conductivity cell and the temperature sensor in the
medium to be measured.
WORK.T shows you that the working temperature that will be used
later on has to be entered.
Note
The reference and working temperatures must differ by at least 5°C.
✱
Enter the working temperature (e.g. 40.0 for 40.0°C), continue
with .
✱
Temper the medium to be measured to the reference
temperature.
- The uncompensated conductivity is shown in the bottom line in
the LC display.
✱
The current value can be accepted immediately by pressing
(for less than 1 second).
blinks
P
P
Summary of Contents for ecoTRANS Lf 03
Page 2: ......
Page 17: ...17 6 5 The operator level USER...
Page 18: ...18 6 6 The administrator level ADMIN...
Page 67: ......
Page 68: ......