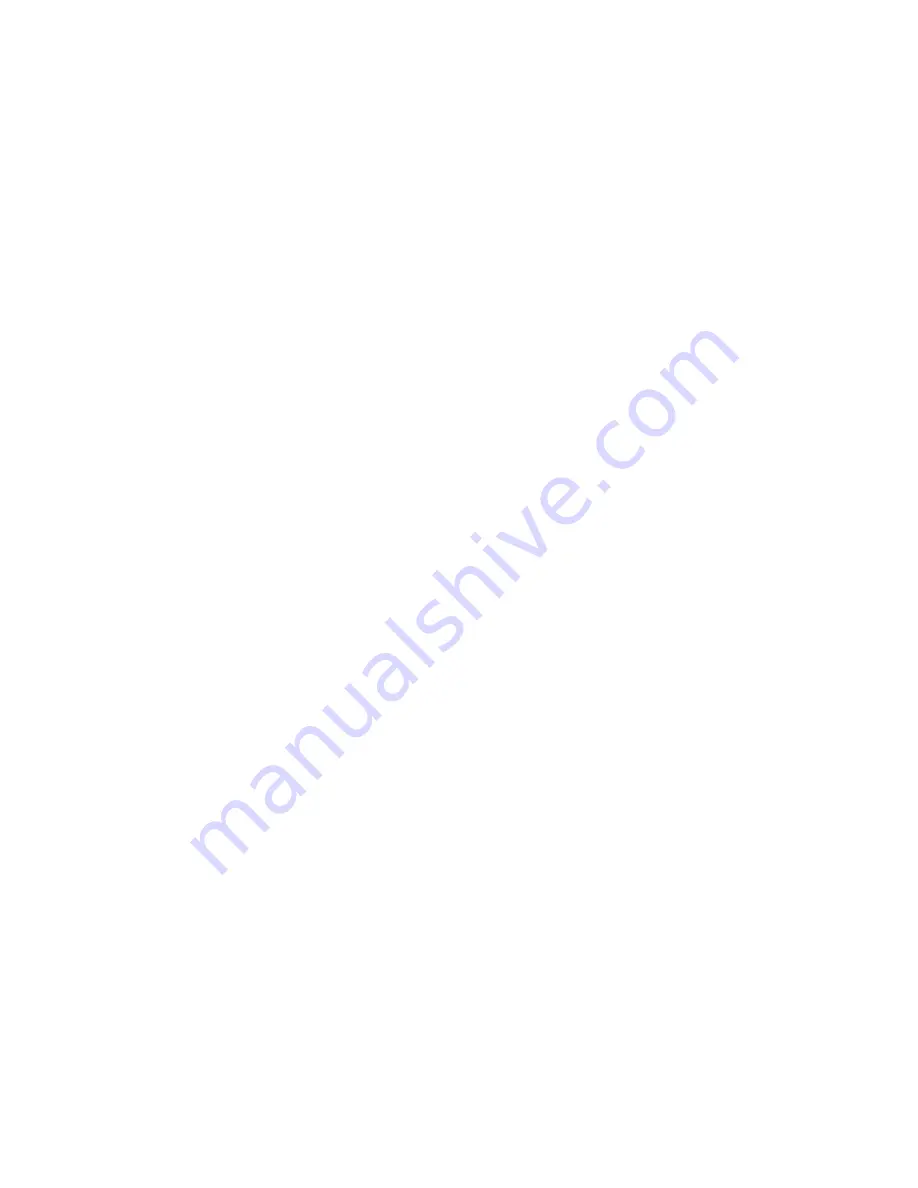
20
MOTOR REPLACEMENT
1. Disconnect all power to the actuator.
2. Remove screws, washers and rear cover.
3. Disconnect actuator output shaft from driven
device and remove actuator from mount.
4. Remove bolts, washers, and front gear case cover.
Note location of all gearing.
5. Remove motor pinion.
6. Remove brake assembly from top of motor.
7. Disconnect motor wires - note colors.
8. Remove motor.
9. Reverse the procedure to install new motor. (Clean
and regrease all gearing, check bushings and
bearings, lubricate bushings with SAE-10, non-
detergent oil.)
10. Reinstall the actuator.
POWER GEARING REPLACEMENT
1. Perform steps 1,3 & 4 of Motor Replacement.
2. Remove defective gear(s) and replace with new.
3. Ensure all gearing and oilite bushings are properly
lubricated as detailed above.
4. Install front cover and Reinstall actuator.
POSITION LIMIT SWITCH REPLACEMENT
1. Disconnect all power to the actuator.
2. Remove rear cover.
3. Remove two screws and washers from appropriate
switch on assembly.
4. Install new switch and transfer wires from old
switch one at a time.
5. No realignment should be necessary.
FEEDBACK POTENTIOMETER REPLACEMENT
A. One Turn Linear Potentiometer
1. Disconnect all power to the actuator.
2. Remove screws, washers, and rear cover.
3. Remove three screws holding potentiometer and
disc to housing.
4. Pull potentiometer and disc out of housing.
5. Measure location of gear from mounting disc to
farthest face of gear and note measurement.
6. Loosen set screws and remove gear.
7. Remove nut and washer holding potentiometer to
disc.
8. Cut shaft of new potentiometer to same length as
old.
9. Mount new potentiometer on disc, tighten potenti-
ometer nut, install gear to measured dimension
from step 5.
10. Install assembly in housing and tighten screws.
11. Using a 25 watt solder iron, remove wires from old
potentiometer one at a time and solder to corre-
sponding terminals on new potentiometer.
12. Align potentiometer and install cover.
B. Characterized Potentiometer
1. Disconnect power and remove rear cover.
2. Remove three screws and pull potentiometer off of
pins.
3. Install new potentiometer and tighten screws.
4. Using a 25 watt solder iron, remove wires from old
potentiometer one at a time and solder to corre-
sponding terminals on new potentiometer.
CAUTION - DO NOT USE EXCESSIVE HEAT
WHEN SOLDERING.
5. Align potentiometer and install cover.
C. LVDT Assembly Replacement
1. Same as Characterized Potentiometer replacement
above.
2. Align LVDT body for zero output (see alignment
procedure, characterized cam adjustment on page
12, step G).
Maintenance
Summary of Contents for SM-1715
Page 23: ...23...