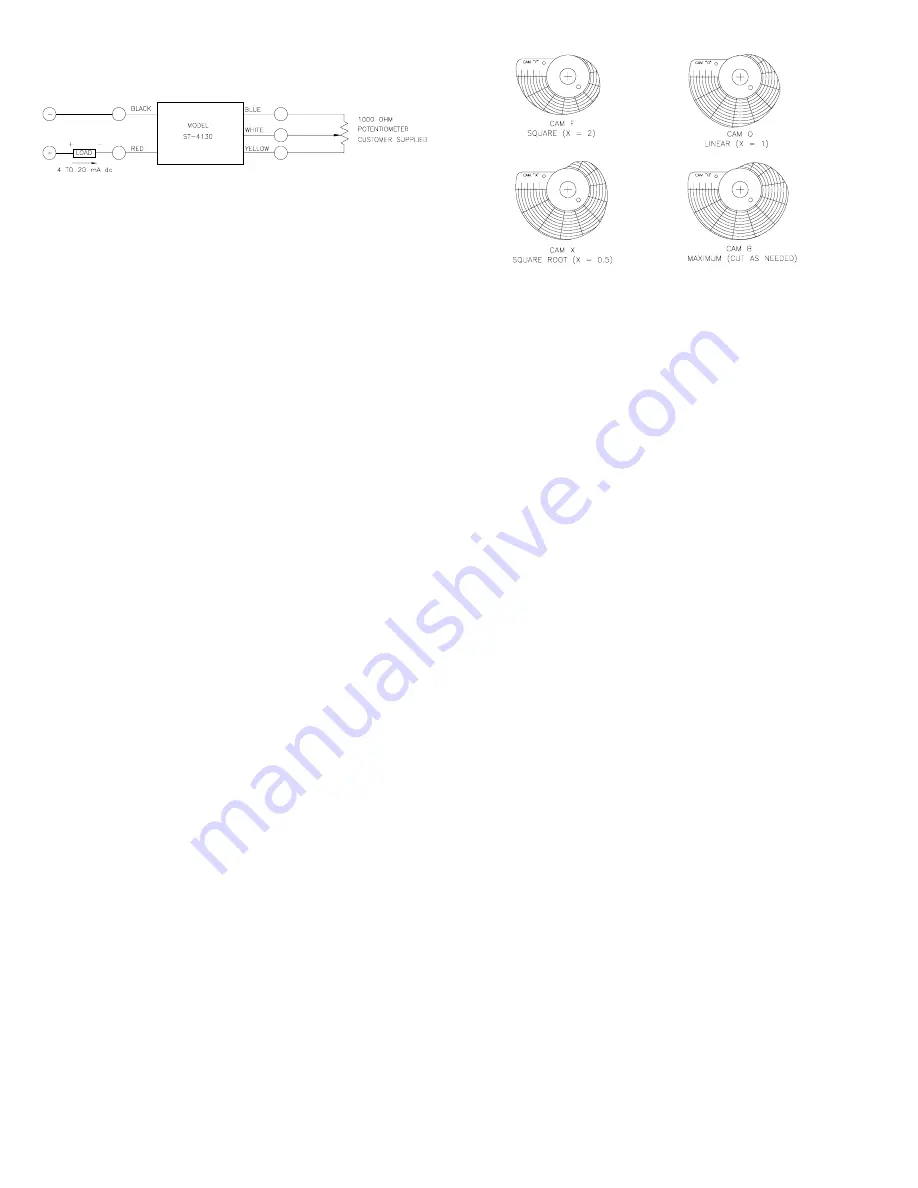
10
For the unit to function optimally, the 4mA end of the
feedback potentiometer must be preset to 50 ohms.
1. Position the actuator to the desired 4mA setting.
2. With potentiometer resistance at 50 ohms, adjust
ELEVATION for 4.0mA output.
3. Position the actuator to the desired 20mA setting.
4. Adjust RANGE for 20mA output.
5. Repeat steps 1 through 4 until desired accuracy is
achieved.
6. To reverse the 4 and 20mA output, interchange the BLUE
and YELLOW wires and return to step 1.
D. ACTUATOR WITH INTEGRAL AD-8130
SERVO AMPLIFIERS
Switch and feedback potentiometer alignment is accom-
plished in the same manner as actuator without amplifiers,
except motor power is supplied from the amplifier. Varying
the command signal input to the amplifier will allow reversal
of the rotation of the actuator output shaft to run to the
minimum/maximum switch settings. If the actuator does not
run to the limit switch, but stops short, the amplifier has
nulled and adjustments of span, elevation, loss of signal, or
feedback potentiometer may be required. Refer to IM-0607
for information on the AD-8130 amplifier.
The EC-10852 is for use with the AD-8130 servo amplifier
with LVDT (voltage feedback). The EC-10852 is used as the
HI and LO trim for the AD-8130. The AD-8130 is factory set
for operation with the EC-10852.
CAUTION: It is impor-
tant not to adjust the HI and LO trim on the AD-8130,
which are torque sealed at the factory
. For specific Setup
information and calibration, refer to the wiring diagram
supplied with your unit.
E. CHARACTERIZED CAM ADJUSTMENT
(OPTION)
The characterized feedback assembly is an option which
directly replaces the standard linear feedback potentiometer.
Prior to adjusting the cam, the end of travel limit
switches must be set and the proper cam installed for
your particular system requirements on the characterized
cam shaft. Four different cams are supplied with each
characterized assembly. The cams are printed on both
sides and may be flipped over to reverse the character-
ization action in relation to the output shaft rotation.
The cams are each printed with a letter O, F, or B
which indicate the cam type. Three of the cams are shaped
to correspond to X=2, 1, and 0.5 respectively in the equa-
tion:
% amplifier input = (% shaft rotation)x
The fourth cam is used for any value of x between 0.5 and 2
and must be cut by the user. For details on cutting this cam,
see To Shape Feedback Cam.
a. Run the actuator to the zero or minimum position limit.
While running, observe the direction of character cam
rotation.
b. Is the cam rotating in the direction of 100-0 for your
system requirement? If not, remove the thumb screw and
flip the cam over. Tighten the screw.
c. Have you selected the proper cam for the system require-
ment? If not, remove the thumb screw and change the
cam, installing the cam the same as in (b) above. (Green
or Black side up.)
d. Loosen three screws and remove the cam assembly.
e. Rotate the cam until the zero on the cam is in line with
the center line of the potentiometer or LVDT shaft.
f. Potentiometers need no further adjustment.
g. LVDT contactless feedback may require fine zeroing.
i. Apply power to the LVDT and monitor the output
with a volt meter.
ii. Loosen the two body clamp screws and slide the
body of the LVDT to obtain zero output.
iii. Tighten the body clamp screws.
iv. If a finer adjustment is desired, loosen the nut on
the LVDT shaft and turn the shaft slightly one
way or the other and tighten the nut.
TO SHAPE FEEDBACK CAM
With characterized feedback, one of the four cams supplied
(cam B), is partially shaped. For installation, it must be cut to
its final shape by the user. This cam is used if none of the
other three cams produces the desired input-output relation-
ship where:
% amplifier input = (% shaft position)X
Two typical conditions where the user might want to use the
fourth cam are:
1.In equation above, if the value of X is not equal to 0.5 or 2.
Summary of Contents for SM-1715
Page 23: ...23...