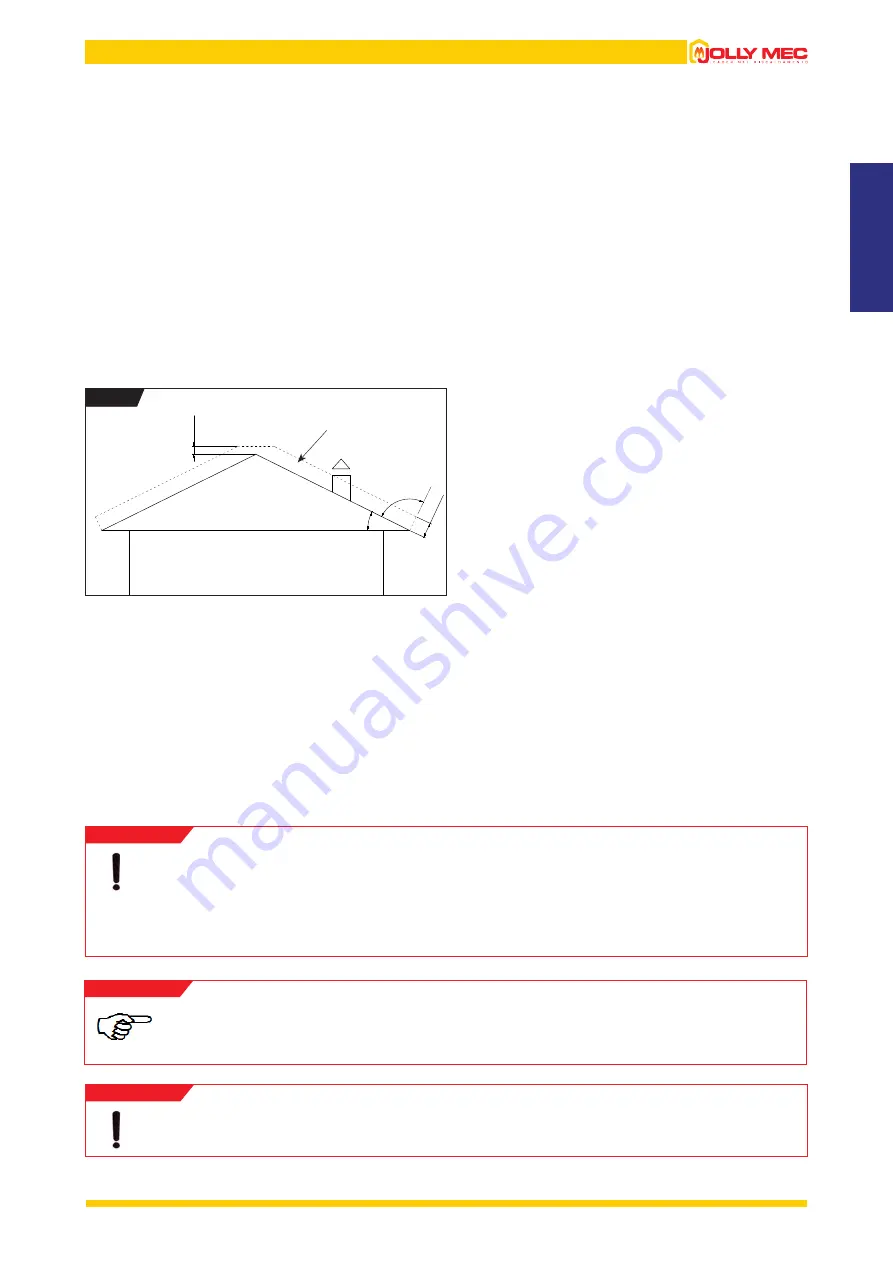
25
ENGLISH
07.3 INSTALLATION ROOM VENTILATION
According to reference regulation UNI10683, 4 Pa depression must be verified between the installation room interior and exterior.
Prepare adequate ventilation openings in the room where the product is installed to permit at least 50 m³/h clean comburent air flow not
taken from polluted rooms. The ventilation openings, if fitted with insect-proof mesh, must be easily removable and undergo periodic
cleaning to ensure clear air flow passage.
If the comburent air inlet is directly connected to the stove, it may be necessary to make adjustments to the control unit, especially during
the start-up phase, as the temperature and humidity of outdoor air not only varies during the period of use of the product, but also come
into direct contact with the pellets and the ignition element, generating different fuel burning times.
Jolly Mec allows the ducting system at the input of the combustion air within and not over the following limits: the length can’t be longer
that 1000 mm, the diameter has to have at least the same section of the stove/boiler connection, it is possible only one 90° change of
direction, the center-to-center distance of the combustion air input pipe can be ± 300 mm.
It is only recommended to connect the comburent air ducting system to the stove if absolutely necessary. Very
cold air and humidity may cause difficulties during the stove ignition phase.
NOTE
As for the fuel product exhaust system, air vents are also extremely important and must be given the appropriate
consideration and respect.
The installer is directly liable for all electrical system parts, generation hook-up to the system, ventilation and the fume
exhaust system and MUST, at the end of installation work, issue a declaration of conformity as per Ministerial Decree 37/08.
On the other hand, the purchaser MUST assign all work to a qualified professional technician.
The device must be installed and used in accordance with all local and national laws and EC Regulations
WARNING
It is not allowed to install coaxial systems for the smoke output.
WARNING
Supporting the weight of the flue with the appliance union is strictly forbidden. Use specific stands or independent supports for this
purpose.
To install other combustion devices in the same room where the pellet appliance is installed, refer to UNI 10683 and UNI 7129 installation
regulations.
The minimum flue height must be over 3,0 m.
Blocking of wall exhaust terminals at any height and any distance from openings, doors and/or windows is not permitted and a very
important rule to follow.
Installation of external fireplaces must be performed using insulated double-walled pipes, to prevent the formation of condensate; it must
also be possible to inspect the base of the fireplace for routine maintenance which must be done at least once a year.
A windproof chimney cap must be installed; in the presence of adverse weather conditions, especially high winds, this accessory allows
the stove flue draught system to operate much easier.
A minimum flue draught between 10 and 14 Pa must be guaranteed. This value must be measured using specific and controlled
instruments each time the appliance and flue undergo maintenance. With strong winds and the chimney cap installed in the reflux area
(see
F
ig
.4
, zone bordered by the dotted line A for roofs with ß>10° slant) of the roof or without complying with the distances foreseen
by UNI 10683 situations may arise where the stove does not work which will trigger the no depression alarm. It is not possible to make
corrections or reset the stove operating values to override the alarm.
.
130 cm
.
50 cm
ß>10°
A
90°
F
ig
. 4