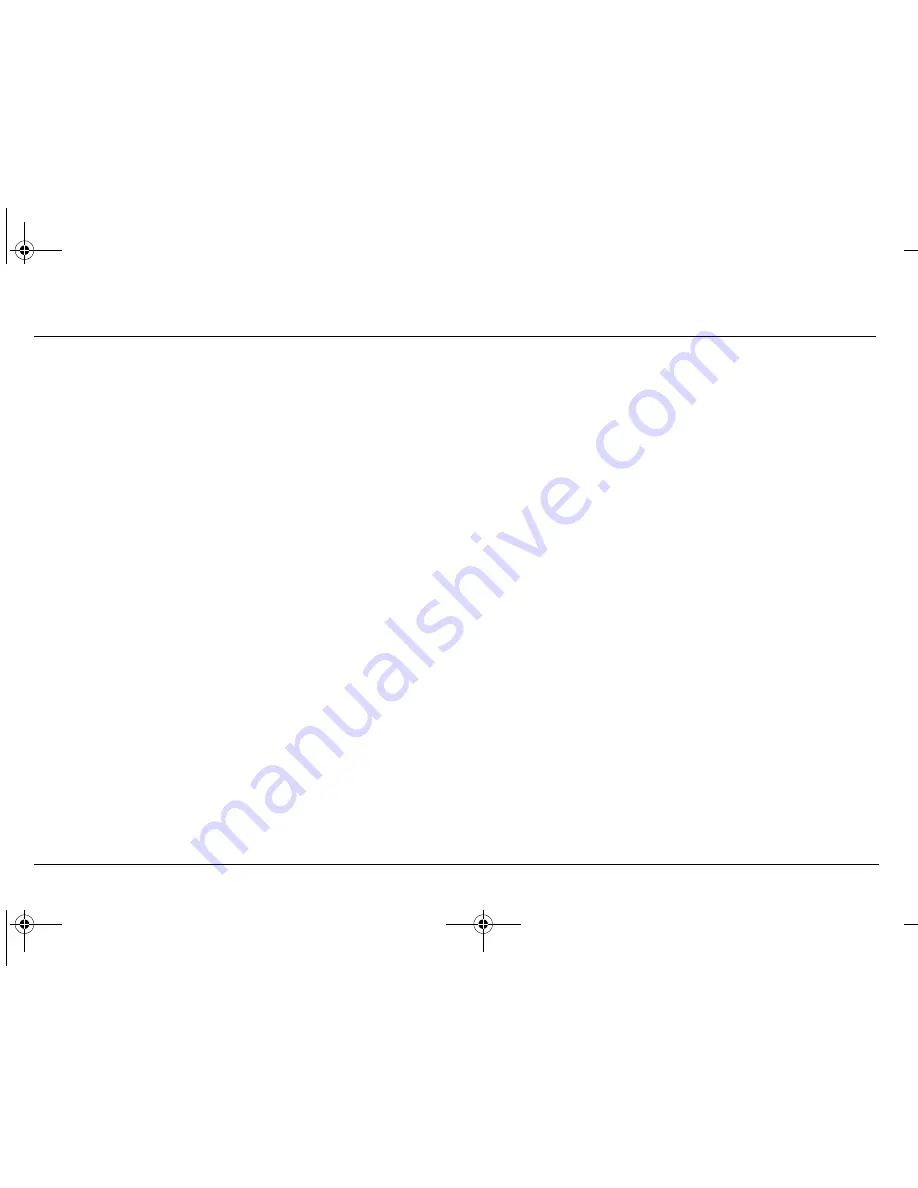
SECTION 1 - SAFETY PRECAUTIONS
1001070451
LIFTPOD by JLG
1-877-254-3876
1-8
www.liftpod.com
1-877-2-LIFTPOD
• Check work area clearances above, on sides, and bottom
of platform while moving, lifting or lowering platform.
• During operation keep all body parts inside platform rail-
ing.
• Exercise extreme caution at all times to prevent obstacles
from striking or interfering with operating controls and per-
sons in the platform.
• Ensure that operators of other overhead and floor level
machines are aware of the aerial work platform's pres-
ence. Disconnect power to overhead cranes.
• Warn personnel not to work, stand, or walk under a raised
platform. Position barricades on floor as necessary.
1.4 MOVING, LIFTING AND REPOSITIONING
General
Never allow personnel in platform while moving, lifting or reposi-
tioning the machine.
This machine shall not be towed by a vehicle.
Ensure platform is fully retracted and completely empty of tools
prior to disassembly, lifting or hauling.
Remove powerpack and tool tray (if fitted) from platform when
transporting in a vehicle.
Refer to the Machine Operation section of this manual for lifting
information.
Additional Safety Information
• Do not use machine as ground for welding.
• Keep all naked flames and sharp edges away from ropes.
• Do not attempt to transport assembled machinery by fork-
lift.
FS.book Page 8 Wednesday, February 11, 2009 11:54 AM