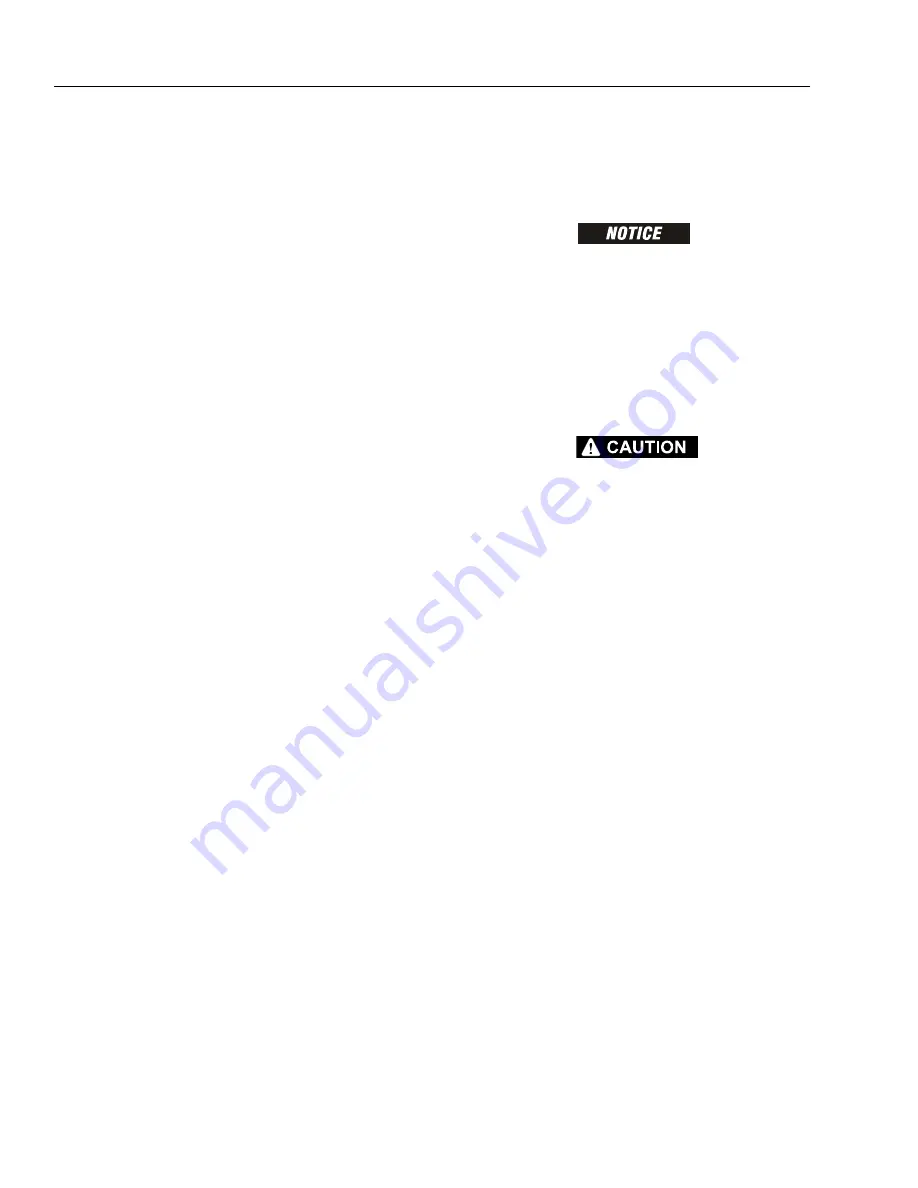
SECTION 3 - CHASSIS & TURNTABLE
3-12
– JLG Lift –
3121160
3.5 DRIVE BRAKE - AUSCO (PRIOR TO S/N
56875)
Disassembly
1.
With shaft protrusion downward, disassemble the
parts in the following order; bolts (24 alternately,
washers (23), power plate (21), and gasket.
2.
Remove the following parts; stationary discs (14),
rotating discs (12), primary disc (11), torque pins (3),
springs (8&9), and the spring retainer (7).
NOTE:
If the bearing and seal are removed for any reason,
both must be replaced.
3.
Further disassembly is not recommended and
should not be attempted unless necessary to
replace the bearing (4), the seal (6), or the shaft (10).
If further disassembly is needed, proceed as follows;
a.
The shaft (10) may be removed by pressing on
the end of the shaft with a shop press.
b.
Using an appropriate tool, pry the seal (6) out
from the inside of the brake. Take care not to
damage the bore. Remove the retaining ring (5).
Tap the bearing (4) out with a plastic mallet.
4.
Remove the piston (15) from the power plate (21) by
introducing low pressure air into the hydraulic inlet
and make sure the piston is directed away from the
operator. Remove the o-rings (17&19) and backup
rings (16&18) from the piston O.D. and I.D. grooves.
Do not remove backup rings (16&18) unless
replacement is necessary because they will be dam-
aged. With shaft protrusion downward, remove the
end cover (13) by removing capscrews (12).
Inspection
1.
Clean all parts thoroughly.
2.
Closely inspect all parts for excessive wear, cracks
and chips. Replace parts as necessary.
3.
Discard seals and o-rings.
4.
Closely inspect bearings and bearing contact sur-
faces. Replace as necessary.
NOTE:
Bearings may be reused if, after thorough inspection,
they are inspection, they are found to be in good
condition.
Assembly
NOTE:
Lubricate all seals and o-rings with clean hydraulic
oil prior to assembly.
THERE MAY BE MORE PARTS IN A SERVICE KIT THAN YOUR
BRAKE REQUIRES. CHECK THE PARTS LIST CAREFULLY FOR THE
EXACT QUANTITY. IN THE CASE OF SPRINGS, SPACE THE
SPRINGS AS SHOWN IN FIGURE 3-4.
1.
Worn o-rings and damaged or worn Teflon backup
rings must be replaced prior to assembly.
2.
The cylinder of the power plate, piston, and o-rings
must be clean prior to assembly and pre-lubed with
the system hydraulic fluid.
THE DEPTH THE PISTON IS INSTALLED INTO THE POWER PLATE
IS CRITICAL. THE SURFACE OF THE PISTON AT THE CUTOUTS
MUST BE FLUSH TO 0.120 IN.(3.0 MM) BELOW THE SURFACE OF
THE POWER PLATE. DO NOT EXCEED THE 0.120"(3.0 MM) DEPTH
OR THE PISTON WILL COCK RESULTING IN COMPLETE LOSS OF
BRAKING.
3.
Assemble the piston (15) into the power plate (21)
using a shop press, being careful not to damage the
o-rings or Teflon back-up rings. Visually align the
center of the cutouts in the piston with the torque pin
(3) holes in the power plate (21).
4.
For replacement of the seal;
a.
Use a shop press to install the bearing (4) into
the housing. Press the outer surface of the bear-
ing only. Install the retaining ring (5) into the
groove.
b.
Press the seal (6) into the housing (1) until it is
flush with the face of the housing. The lip of the
seal must face towards the bearing.
5.
Press the shaft into the housing until it stops on the
bearing. Support the inner race of the bearing dur-
ing the press operation.
6.
Rotating discs must be clean and dry. The lining
material and mating surfaces of the stationary discs
must be thoroughly clean and free of debris. Worn
or scored rotating discs must be replaced.
7.
Install bolts (24) with washers (23) in the power plate
(21. Tighten sequentially, one turn at a time, until the
power plate is properly seated. Torque 105-115 Ft.
Lbs.(142.4-155.9 Nm)
Summary of Contents for 740A
Page 1: ...Service and Maintenance Manual Models 740A 740AJ P N 3121160 January 8 2013 ...
Page 2: ......
Page 52: ...SECTION 2 GENERAL 2 12 JLG Lift 3121160 NOTES ...
Page 109: ...SECTION 3 CHASSIS TURNTABLE 3121160 JLG Lift 3 57 Figure 3 39 Swing Hub ...
Page 135: ...SECTION 3 CHASSIS TURNTABLE 3121160 JLG Lift 3 83 Figure 3 48 Rotary Coupling Port Location ...
Page 153: ...SECTION 3 CHASSIS TURNTABLE 3121160 JLG Lift 3 101 Figure 3 54 EFI Component Location ...
Page 156: ...SECTION 3 CHASSIS TURNTABLE 3 104 JLG Lift 3121160 Figure 3 55 ECM EPM Identification ECM EPM ...
Page 173: ...SECTION 3 CHASSIS TURNTABLE 3121160 JLG Lift 3 121 Figure 3 65 EMR2 Fault Codes Sheet 1 of 5 ...
Page 174: ...SECTION 3 CHASSIS TURNTABLE 3 122 JLG Lift 3121160 Figure 3 66 EMR2 Fault Codes Sheet 2 of 5 ...
Page 175: ...SECTION 3 CHASSIS TURNTABLE 3121160 JLG Lift 3 123 Figure 3 67 EMR2 Fault Codes Sheet 3 of 5 ...
Page 176: ...SECTION 3 CHASSIS TURNTABLE 3 124 JLG Lift 3121160 Figure 3 68 EMR2 Fault Codes Sheet 4 of 5 ...
Page 177: ...SECTION 3 CHASSIS TURNTABLE 3121160 JLG Lift 3 125 Figure 3 69 EMR2 Fault Codes Sheet 5 of 5 ...
Page 244: ...SECTION 4 BOOM PLATFORM 4 28 JLG Lift 3121160 Figure 4 14 Rotator Assembly HELAC ...
Page 286: ...SECTION 4 BOOM PLATFORM 4 70 JLG Lift 3121160 NOTES ...
Page 307: ...SECTION 5 HYDRAULICS 3121160 JLG Lift 5 21 Figure 5 17 Variable Displacement Pump Rexroth ...
Page 316: ...SECTION 5 HYDRAULICS 5 30 JLG Lift 3121160 NOTES ...
Page 319: ...SECTION 6 JLG CONTROL SYSTEM 3121160 JLG Lift 6 3 Figure 6 2 ADE Block Diagram ...
Page 328: ...SECTION 6 JLG CONTROL SYSTEM 6 12 JLG Lift 3121160 Figure 6 11 Control Module Location ...
Page 374: ...SECTION 6 JLG CONTROL SYSTEM 6 58 JLG Lift 3121160 NOTES ...
Page 406: ...SECTION 7 BASIC ELECTRICAL INFORMATION SCHEMATICS 7 32 JLG Lift 3121160 NOTES ...
Page 407: ......