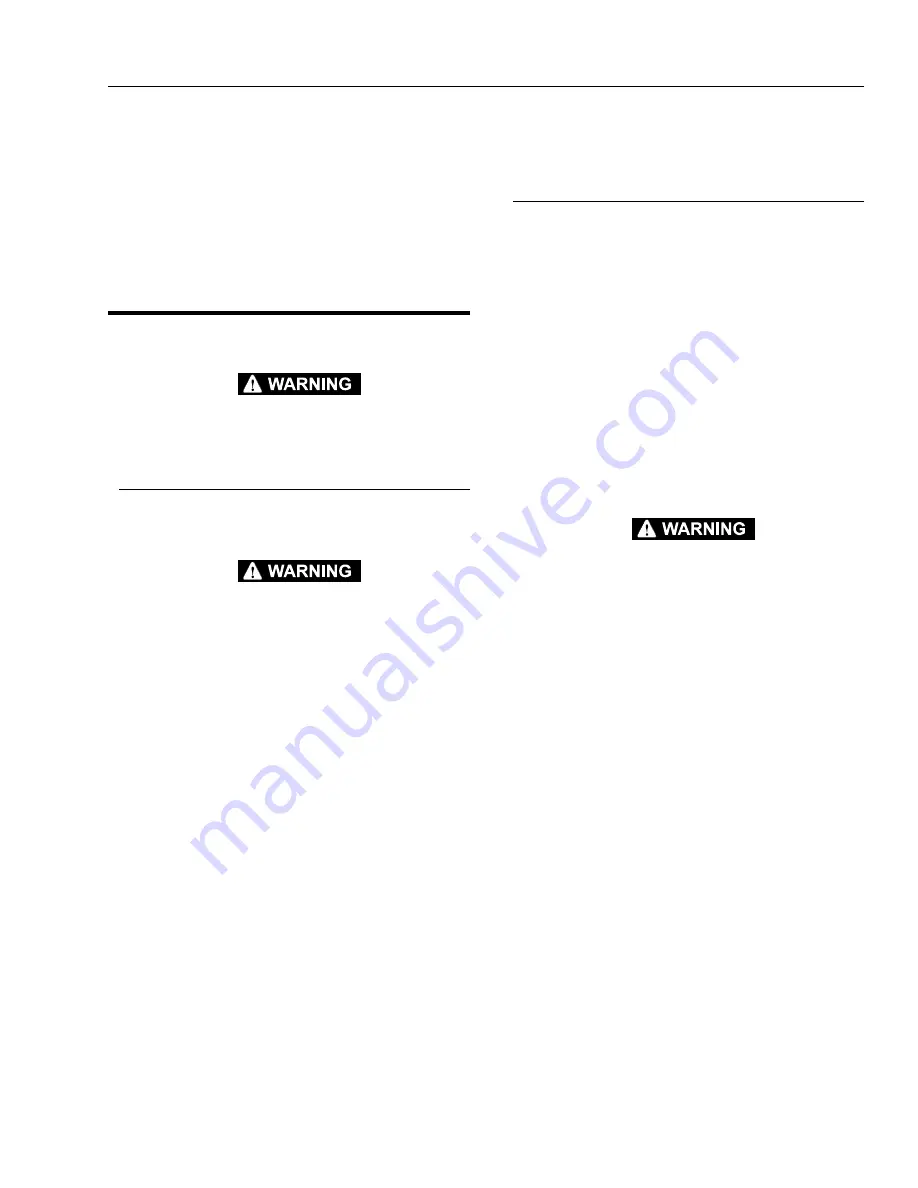
SECTION 2 - PREPARATION AND INSPECTION
3120880
– JLG Sizzor –
2-3
to the operator in the event he/she notices a condition that
requires prompt attention during the walk-around inspec-
tion or during operation until the proper service personnel
can be notified. The Service and Maintenance section pro-
vides specific torque values and periodic maintenance
procedures with a listing of individual components. Utiliz-
ing this torque chart in conjunction with preventive mainte-
nance section will enha nce saf ety, r eliab ility and
performance of the machine.
2.7
BATTERY MAINTENANCE AND
CHARGING
TO AVOID INJURY FROM AN EXPLOSION, DO NOT SMOKE OR
ALLOW SPARKS OR A FLAME NEAR BATTERY DURING SERVIC-
ING.
Battery Maintenance, Quarterly
1.
Open battery compartment cover to allow access to
battery terminals and vent caps.
WHEN ADDING WATER TO BATTERIES, ADD WATER UNTIL ELEC-
TROLYTE COVERS PLATES. DO NOT CHARGE BATTERIES
UNLESS ELECTROLYTE COVERS PLATES.
NOTE: When adding distilled water to batteries, non-metallic
containers and/or funnels must be used.
To avoid electrolyte overflow, add distilled water to
batteries after charging.
When adding water to the battery, fill only to level
indicated.
2.
Remove all vent caps and inspect electrolyte level of
each cell. Electrolyte level should be to the ring
approximately one inch from top of battery. Fill bat-
teries with distilled water only. Replace and secure
all vent caps.
3.
(Remove battery cables from each battery post one
at a time, negative first. Clean cables with acid neu-
tralizing solution (e.g. baking soda and water or
ammonia) and wire brush. Replace cables and/or
cable clamp bolts as required.
4.
Clean battery post with wire brush then re-connect
cable to post. Coat non-contact surfaces with no-ox-
id “A” compound, mineral grease or petroleum jelly.
5.
When all cables and terminal posts have been
cleaned, ensure all cables are properly positioned
and do not get pinched. Close battery compartment
cover.
6.
Start hydraulic system and ensure that it functions
properly.
Battery Charging, Daily
NOTE: To avoid excessive battery charging time, do not
allow batteries to become completely discharged.
To avoid electrolyte overflow, add distilled water to
batteries after charging.
When adding water to the battery, fill only to level
indicated.
1.
Charge batteries at the end of each work day, or
when machine performance is significantly reduced
due to batteries becoming discharged.
2.
Charge batteries in accordance with the following
procedure:
a. Position the Platform/Ground Select Switch to
the off position.
b. Open battery compartment, and battery charger
compartment covers.
WHEN BATTERY CHARGER IS TO BE USED, CHARGING HAR-
NESS MUST BE PLUGGED INTO A GROUNDED 110 VOLT RECEP-
TA C L E . I F R E C E P TA C L E I S N O T G R O U N D E D A N D A
MALFUNCTION SHOULD OCCUR, THE MACHINE COULD CAUSE
SERIOUS ELECTRICAL SHOCK.
c. Remove charging harness cable and connect to
a 220 volt receptacle.
d. Allow batteries to charge until ammeter on
charger, if equipped, is reading zero (0). Normal
charging time is 8-10 hours.
NOTE: When batteries are completely charged, disconnect
charging harness cable from receptacle. Store
charging harness cable.
e. Ensure battery cables are positioned and are not
pinched. Close and secure all compartment
doors.
3.
The battery packs on each side of the frame are
designed to be easily removed so that a machine
can have two sets of them in order to keep the
machine functioning longer. Disconnect the cable
quick connects, and remove the two clevis pins on
top of the frame. Now, using the forklift pockets
under the packs, have a forklift move them to a
place where they can be recharged. The new battery
packs can be installed by reversing the above pro-
cedure.
NOTE: Battery packs are interchangeable.
Summary of Contents for 3369 electric
Page 1: ...Operators and Safety Manual Model 3369electric 3969electric 3120880 March 8 2000...
Page 4: ...FOREWORD b JLG Sizzor 3120880 This page left blank intentionally...
Page 22: ...SECTION 2 PREPARATION AND INSPECTION 2 8 JLG Sizzor 3120880 Figure 2 3 Torque Chart...
Page 28: ...SECTION 3 USER RESPONSIBILITIES AND MACHINE CONTROL 3 6 JLG Sizzor 3120880 Figure 3 5 Symbols...
Page 36: ...SECTION 5 OPTIONAL EQUIPMENT 5 2 JLG Sizzor 3120880 This page left blank intentionally...
Page 42: ......
Page 43: ......