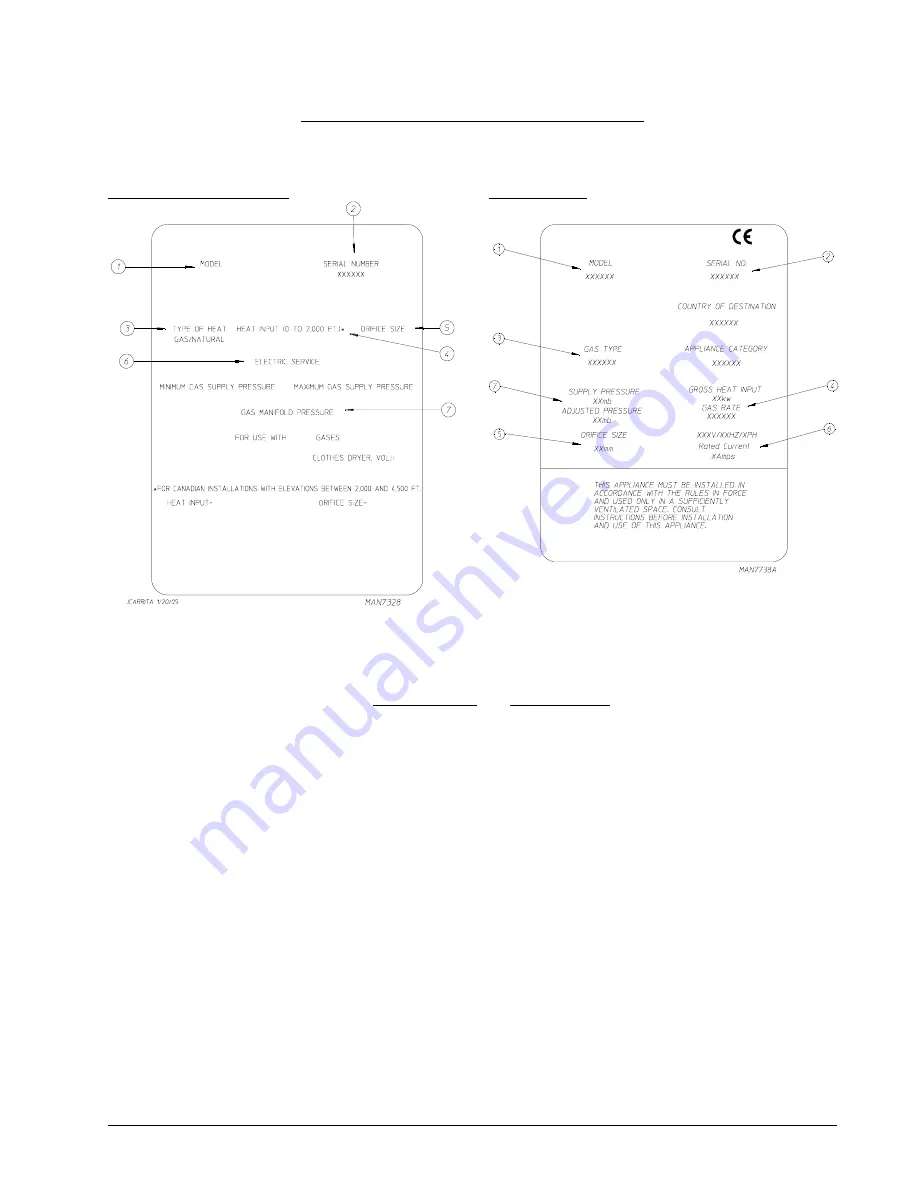
113372 - 16
Telephone: 01422 822282
41
When contacting JLA, certain information is required to ensure proper service/parts information from JLA.
This information is on the data label affixed to the upper left side panel area behind the top control (access) door.
When contacting JLA, please have the model number and serial number available.
1. MODEL NUMBER – This describes the style of dryer and type of heat (gas, electric, or steam).
2. SERIAL NUMBER – Allows the manufacturer to gather information on your particular dryer.
3. TYPE OF HEAT – This describes the type of heat for your particular dryer, gas (either natural gas or L.P.
gas), electric, or steam.
4. HEAT INPUT (For Gas Dryers) – This describes the heat input in British thermal units per hour (Btu/hr) or
kilowatts (kW).
5. ORIFICE SIZE (For Gas Dryers) – Gives the number drill size used.
6. ELECTRIC SERVICE – This describes the voltage and current rating for a particular model.
7. GAS MANIFOLD PRESSURE (For Gas Dryers) – This describes the manifold pressure taken at the gas
valve tap.
SECTION VII
DATA LABEL INFORMATION
STANDARD LABEL
CE LABEL
Summary of Contents for D75
Page 52: ...Part No 113372 16 11 12 15 ...